The problem
I have had issues with the BeagleBone Black turning off after a period of operation. The exact reason I’m not too sure. The rest of the electronics seemed to be on, but I admit I did not check to see if the Sync light remained on the Radio modem.
Some investigations revealed that the BBB PSU voltage was at times dropping down to as far as 4.75 volts. I am pretty sure that the BeagleBone Black has an operating voltage from 4.75 to 5.25 volts. This I suspect is the culprit.
This issue started happening after I pushed the radio up to 30dbi. i.e. the battery has to provide even more power, which I suspect is leaving the BBB with less juice.
I was also concerned now that the BBB battery life, was a lot less than needed for a few good hours of trekking, following the balloon. I decided that an overhaul was required. I did not however, want to go back to two Pb/Acid Gel batteries. Each ways about 750grams, and the two is just too much of a burden.
The Solution
I decided that I would need to remove the Linear Voltage Regulator and batteries.
I initially thought I might be able to use the Switch Mode PSU that was used to power the RFD900 modem, but discovered it is producing 5.3 volts out and the BBB has some protection in it to not turn on. So this didn’t work.
Components of the final solution were:-
- A 3S LiPo battery – higher voltage and amperage
- Build and install a Switch Mode PSU
The 3S has a voltage of 11.1 volts (though is more when fully charged). Minimum voltage is 9 volts. This works well because the Switch Mode PSU needs input voltage of ~8 volts or more.
The 3S battery weighs 250grams, which is a lot more than the 75 grams the other batteries weighed, but is considerably less than the Pb/Acid batteries.
Below are some pictures of the result of all this work.
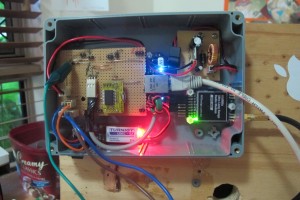
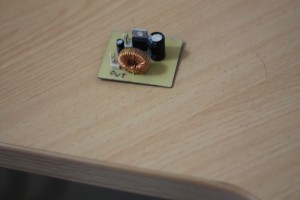
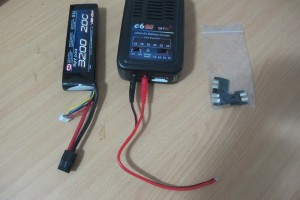