The only way to succeed is to not shy away from setting major goals. In particular, the next launch is going to build significantly on the previous launch. The goals of the next launch are to:-
- Miniturise the PCB significantly
- Use smaller ‘solder-on’ LIPO Batteries
- Design PCBs, so they can be daisy chained. This is so that when we get our ‘five’ PCBs from the PCB manufacturer, we don’t use one and waste four. We would be using 2, or possibly 3 of the PCB in the next flight
- Make the PCB more configurable/flexible in how they can be used.
- Resolve issue with Air Pressure sensor
- Utilise greater memory storage with i2c fRAM
- Use a Accelerometer/Gyroscope (instead of just a gyroscope)
- Utilise a system to swivel masses around using servos at 0.25 seconds into flight (after some of the motion has dampened down). We want to do this to measure the effect on the flight of the rocket…and so compare to previous results.
This is certainly a huge leap, but not unobtainable. There are many independent parts…some might succeed, while others might fail. So there is sure to be some success, somewhere.
We would need to use a 3-D Printer to turn this into reality.
We are initially going to do a mock-up using Perspex and some electronics in a breadboard. We will initially concentrate on the Servos and their ability to move quickly and consistently. If this works okay, then we will go about :-
- Designing a special case PCB
- Purchasing a 3-D Printer to create the mechanical device
Below is a screenshot of the design inside Blender.
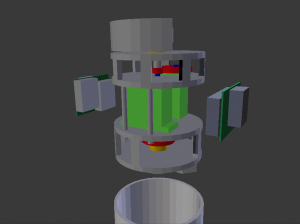