The next step is to profile the fins and to score/sand the roots and tangs. Some important decisions to make are:-
- How to evenly sand the surface of the fins (so it is symmetrical)
- What profile is required – at leading edge and trailing edge.
- How to score the fins
We concentrate on the first two here.
Fin Symmetry
When I examined the fins, the first thing I noted was that the chamfer in them is not symmetrical to begin with. This is unfortunate, but I’m just going to have to work with it.
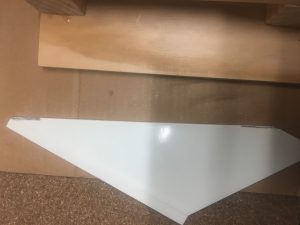
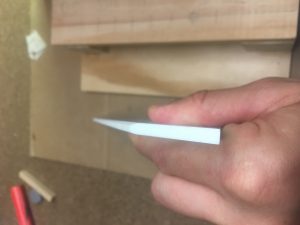
Well, that is something we will need to work with. I had a vision of a semi-circle shaped leading edge, but this is probably not possible now. Will probably make them parabolic, or elliptical in shape.
The tools to sand down the fins
The first tool I created to sand down fins was the following:-
The problem with this is that the sandpaper lifts off from the surface and interferes with the sanding process. The area of sandpaper available sanding is reduced because it needs to be sandwiched between the pieces of wood. Because the longest section of fin to be sanded is 250mm, this means we can’t sand the edge down (along the whole length) in the same stroke. This is a big disadvantage, and was one of the identified issues we wanted to solve.
Some tests were done to see if we could get a nice job done using wood and it looks like it “should” work. See below:-
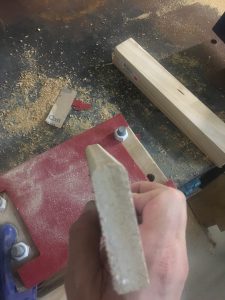
As you can see, the edges look very well curved. I did this curve by doing sanding at ~30 degrees, ~45 degrees, ~60 degrees. Then I did a ‘curving’ action to try and get it rounded. This makes a ‘semi-circle’ like edge.
I decided to build a simpler sanding plate. I needed:-
- Sandpaper
- Spray Glue
- Plywood
- Clamps
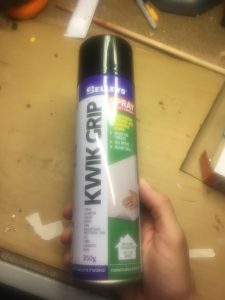
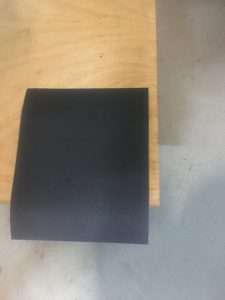
I followed the instructions very carefully. Spraying both the sandpaper and plywood, then letting them sit for 10 minutes. Then I put the two together and I clamped them over night. I decided to put 80-grit sand-paper on one side and 240-grit sand paper on the other side.
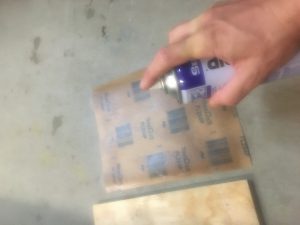
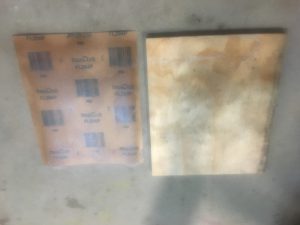
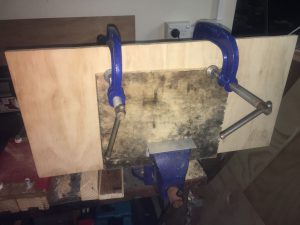
Here is the end result.
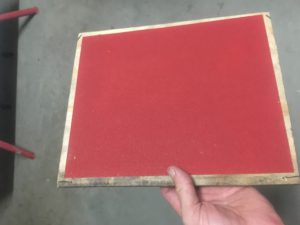
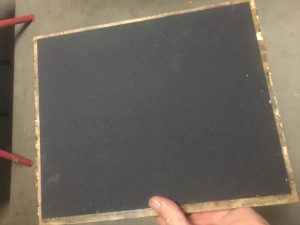
Notice how there is some bare plywood accessible on the edge of the sanding board. We have drilled some holes into this can can mount this to a large piece of plywood. This allows mounting the sanding board on a solid (non-moving) bench. See below.
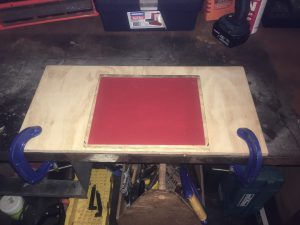