I wrote a single page e-mail to family on the days proceedings. I decided I would share this here on the blog.
The days proceedings
Jeremy, Grandma Patsy and I got up at some crazy time 04:30 for Grandma Patsy and 05:00 for Jeremy and myself.
We had a quick bit of breakfeast - weetbix…teas and other foods.
Then I loaded all the boxes (which I had left near the front door) into the roomy Toyota Kluger… and then we set off.
We all spotted some Hot air balloons as we started our ~60min journey to Cedar Grove Road. Most of the trip was in lovely rural surroundings.
About 1/2 way into the trip we all stopped off at a small cafe in Canungra called the “Outpost Cafe”.
There Grandma Patsy got a coffee – flat white – hot in a take-away cup, and I got two slices of toast with Vegemite…sharing the facilities
with middle-aged(and older) “friendly” bikies.
Then after the usual pit stop activities, we resumed our drive.
Eventually we got to Jimboomba…I was a little anxious because the road seemed to go on forever and was wondering if I’d missed some vital turn-off.
I had nothing to worry about. About 10 min later, we spied the launch site. The first thing I could see were blue portaloos. I was delighted to see them.
2 mins later we were driving into a paddock. Grandma Patsy did the honors opening the gate and then we were back together. Thanks Grandma Patsy 🙂
We met up with about 4 other chaps who kindly suggested we not park so close to the toilets. We took their advice and parked further away.
There was no equipment at this stage…and it became apparent that the arrival of the equipment was lagging. Eventually a huge truck made its way and before we knew it, Jeremy and myself were helping set up all the equipment. We stuck mostly to erecting several Gazebos. Jeremy was terrific getting the pegs and hammering them in.
We got our equipment on to a table…one nice chap said…possession is nine / tenths of the law….
Then someone stole the two tables from under us!!
Fortunately, someone loaned a table and the Tarp I brought all the way from Cairns, suddenly became valuable property!
8:30 came and the launches started. Dave, Lake, Reef and Vanessa’s father arrived…and eagerly watched. At various occasions I helped them set-up their rockets. Jeremy gave up waiting for me to get him a motor….I suggested he approach Blake with some money and ask him for some advice on what motor he required. Blake helped Jeremy with the motor purchase and I helped Jeremy assemble the motor. Jeremy’s flight went really well.
For about 4 hours I set-up the rocket. Everyone was looking in…Jeremy was taking photos. Grandma Patsy helped as much as possible, making sure no one got too close. I was a little nervous having this awesomely powerful motor on the table and people casually walking past it. But we were following procedures to a tee.
I had my instruction manual with check-boxes and pictures…and only after inspecting all components, did I actually start assembling components. So many things were checked and re-checked.
Then at about 12:30….the launch pad that I wanted to use was vacated…their rocket went up…and then splashed down into the Logan river….(only about 4 hrs later did some university students practice their swimming skills to pull that rocket…a 4 metre beast…from the river. Lucky they don’t have crocodiles down this way!!).
I didn’t take any photos myself… I wanted to see it through my own eyes and be in the moment…so to speak.
Recovery
After the flight, Jeremy, Lake and myself bounded up the paddock, through long grass to recover it. 30 min later, we were talking back….Lake was holding the Nose cone, Jeremy was holding the large Parachute and I holding the rest of the “bits” as best as I could….across the muddy river bed in my best Black shoes (well almost the best…the ones I wear to Darwin for work).
Hot, tired, sweaty and alive. 2 litres of fluids later…felt a bit more alive…Sweet feeling of success.
It was not quite over though….
Videos
I do have a few small videos of the launch.
Here is a larger video – with more details on the whole build/launch.
Alas I do not have photos or videos of it coming down…. But I assure you….it was seamless.
Here are the best screenshots I got of it coming down.
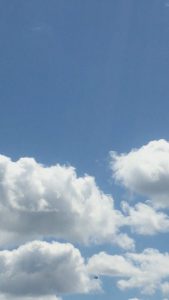
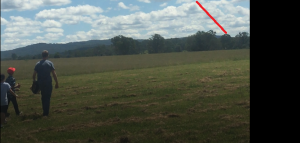
Flight Data
As you can see, it reached an altitude of 3528 feet. Very impressive.