38mm CTI and AeroPak motors come buy default with approx 1.4 grams of Black Powder for their ejection charges. Based on this and the fact my rocket has half of volume blocked off by engine block, I decided to start my ejection charge tests at 0.75 grams. Ultimately I got up to 1.76 grams of BP. This post discusses this in detail.
How the system is packed.
This is probably the best place to describe how the recovery system was packed, because the tests identified a possible issue with the set-up.
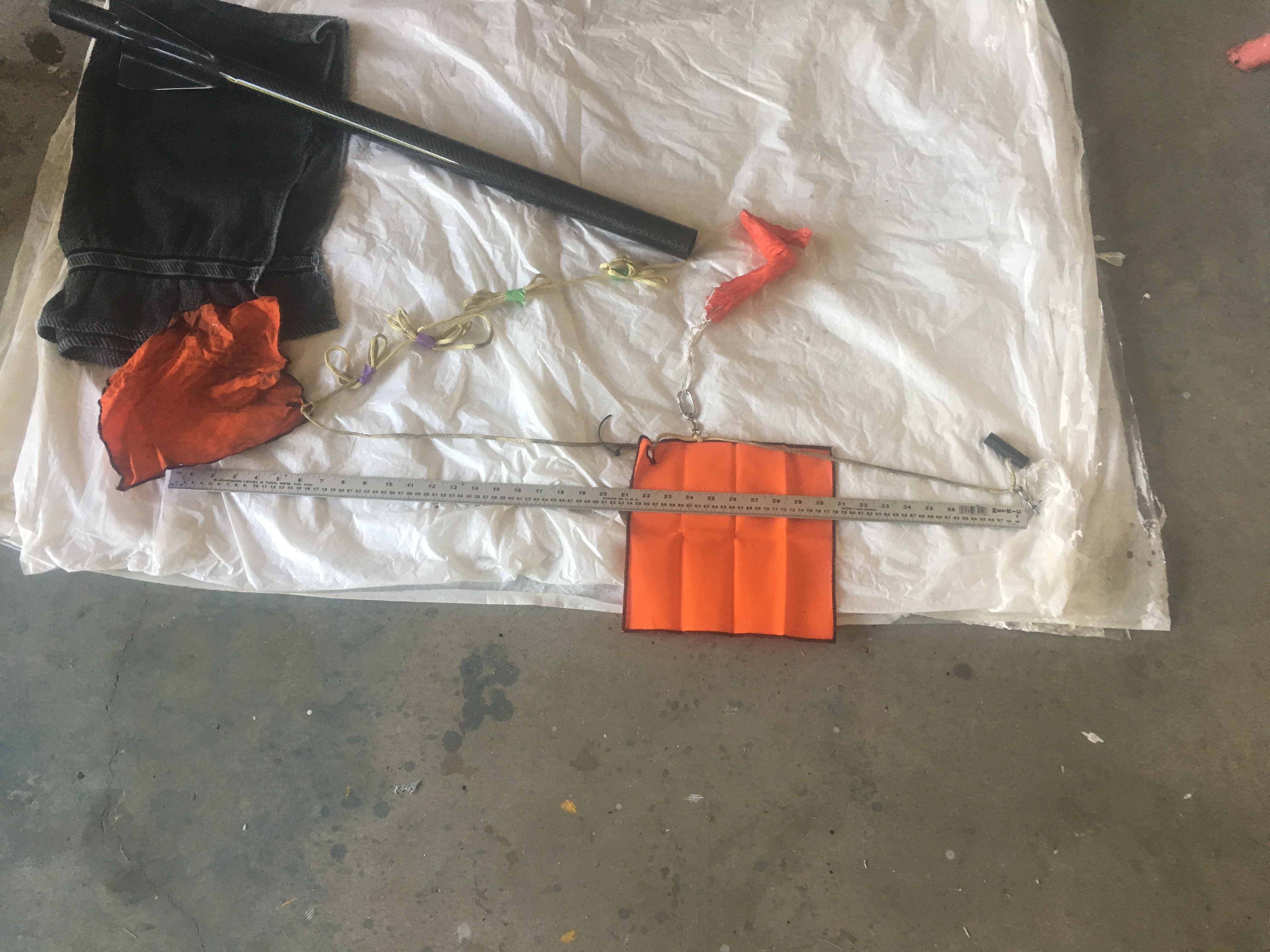
You will notice in this photo there are TWO Nomex blankets. The left oneĀ covers the shock-cord (but its primary purpose is add additional drag) and the other Nomex blank protects the parachute. The right Nomex blanket is held in place with a Cable Cutter, the right is simply wrapped into a bundle.
The parachute is on a Swivel and uses a 4mm Quick-Link. The Shock-cord is 5 metres in length, with 0.5 meters inside the air-frame. Notice the use of Z-Folds.
How the Parachute is folded
Here are some photos of how it was folded.
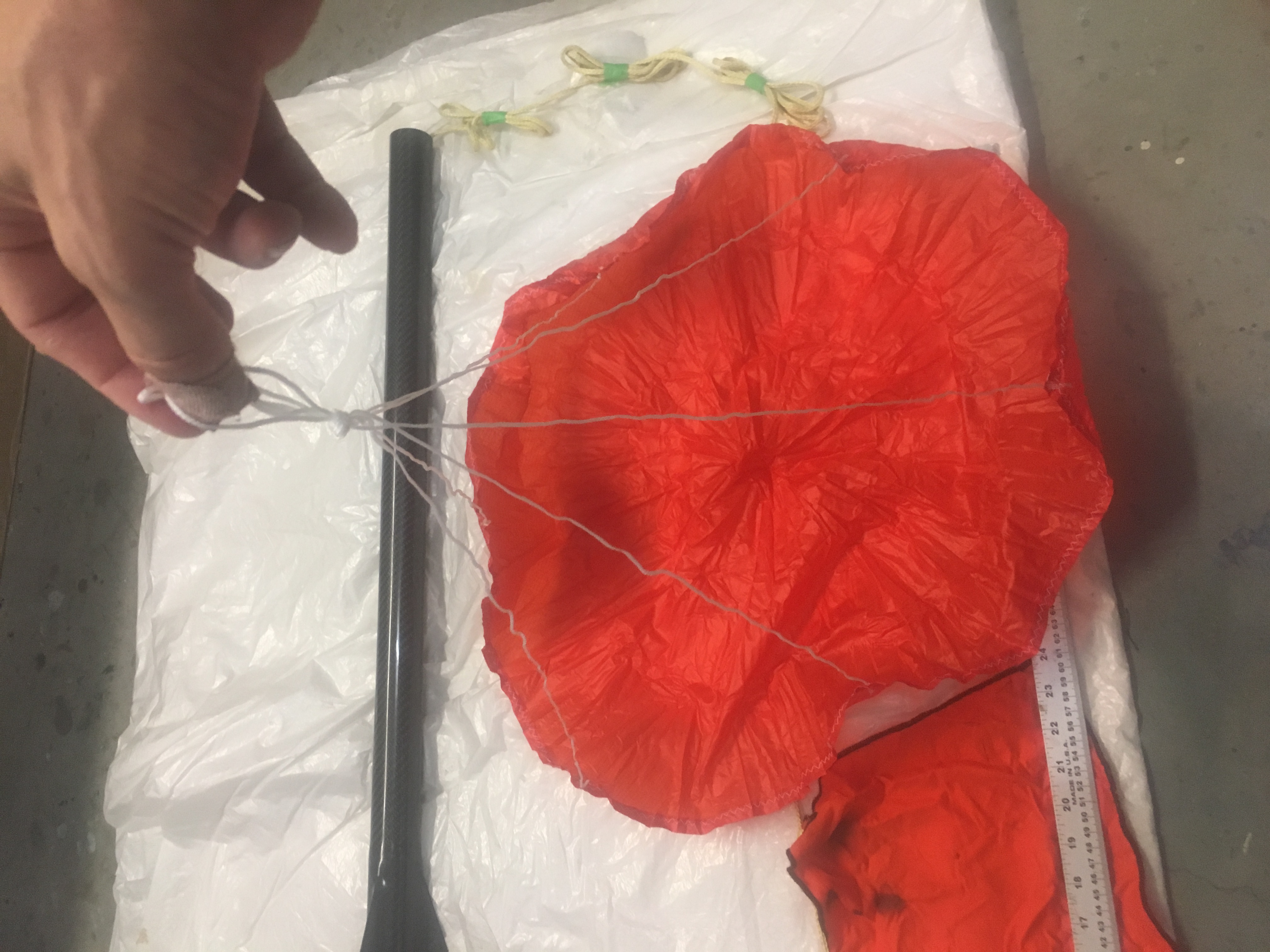
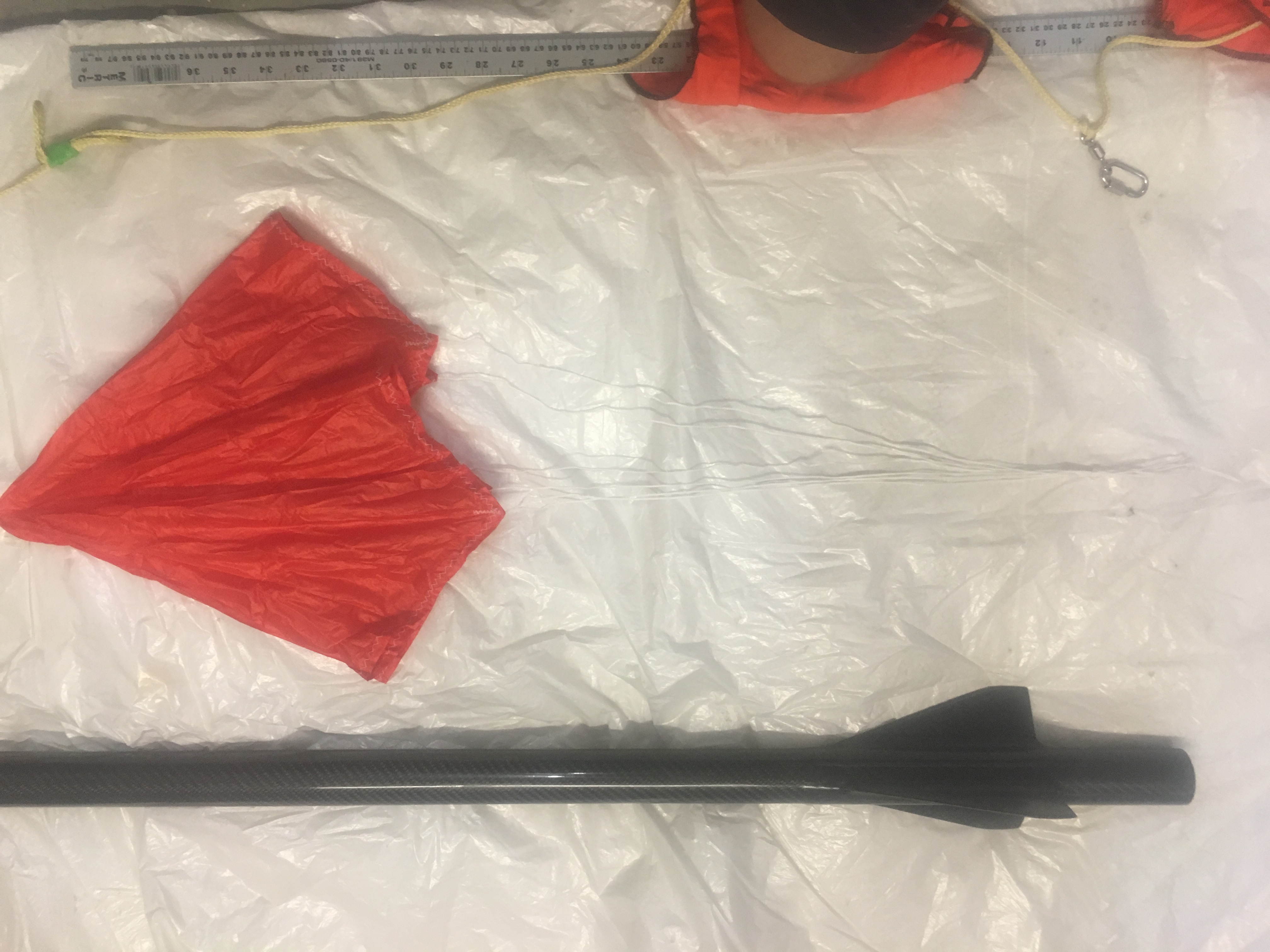
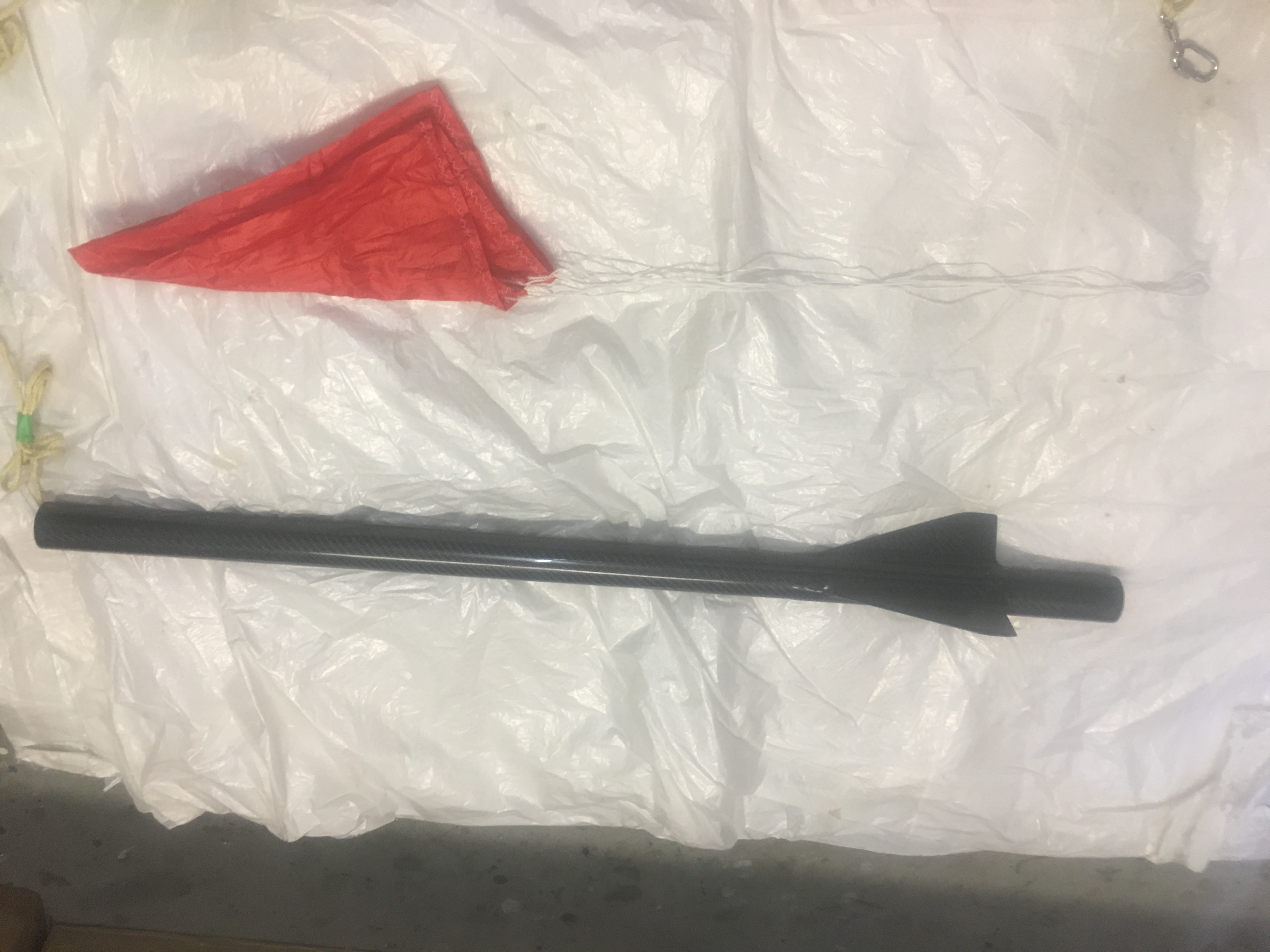
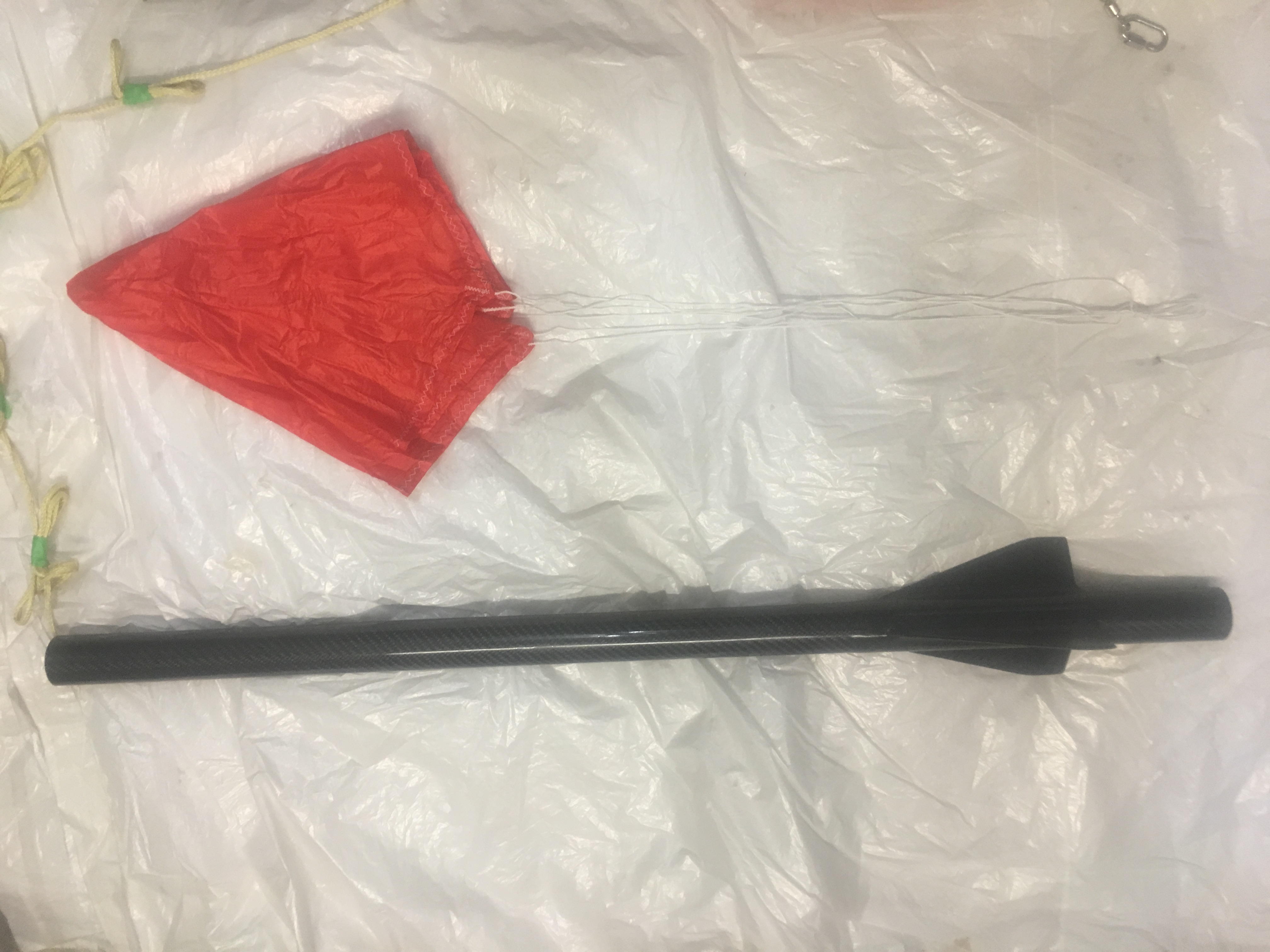
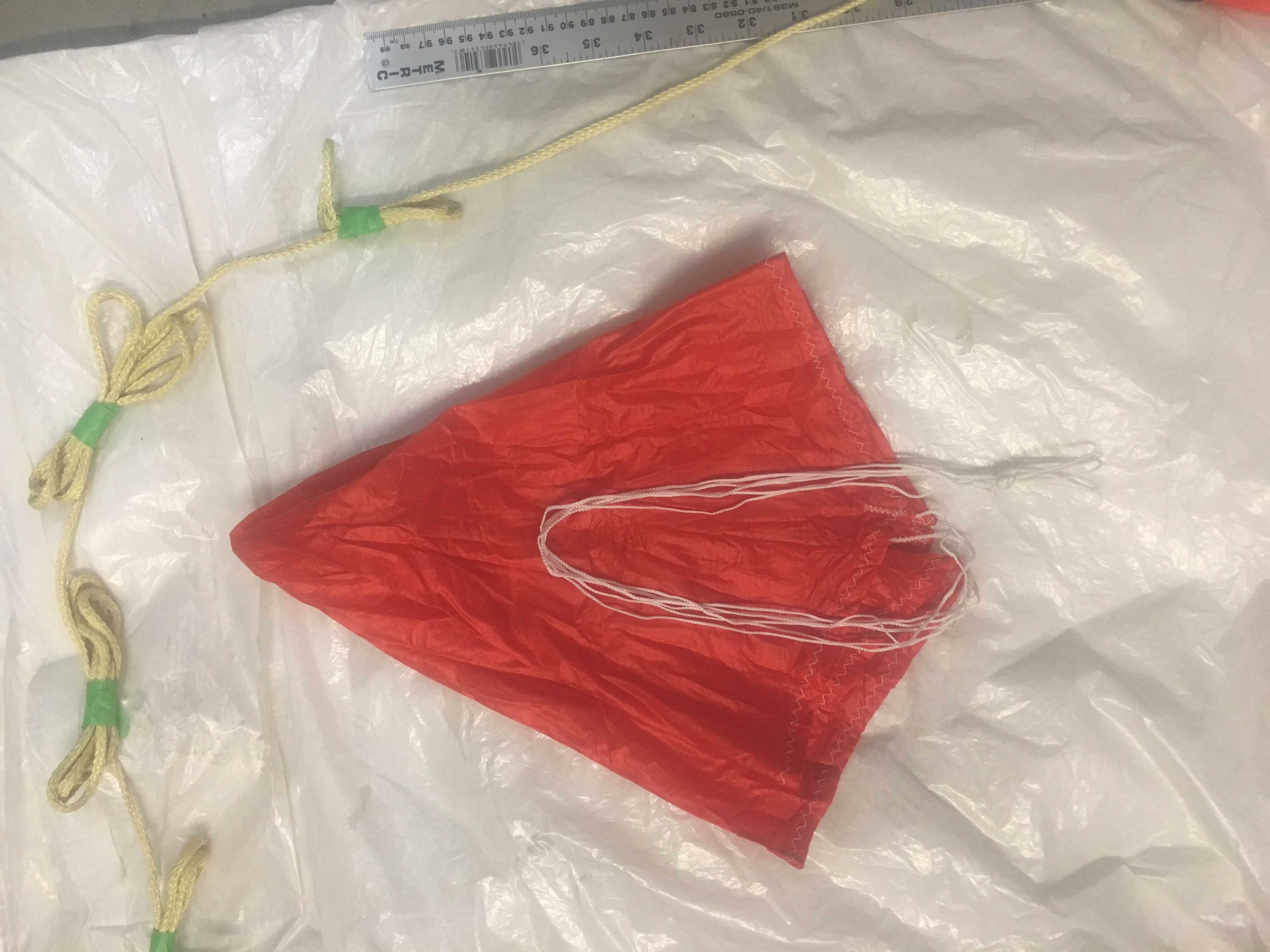
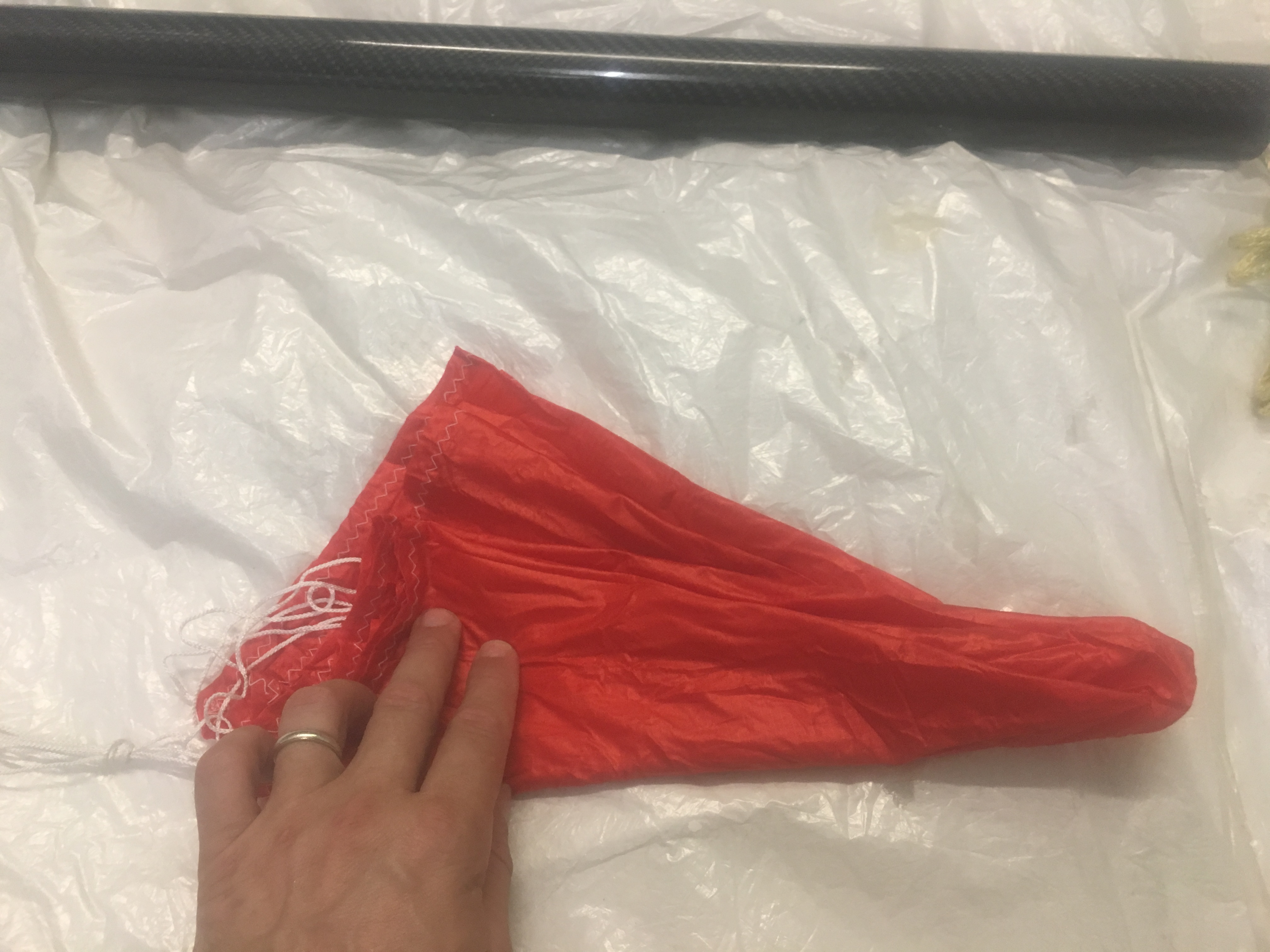
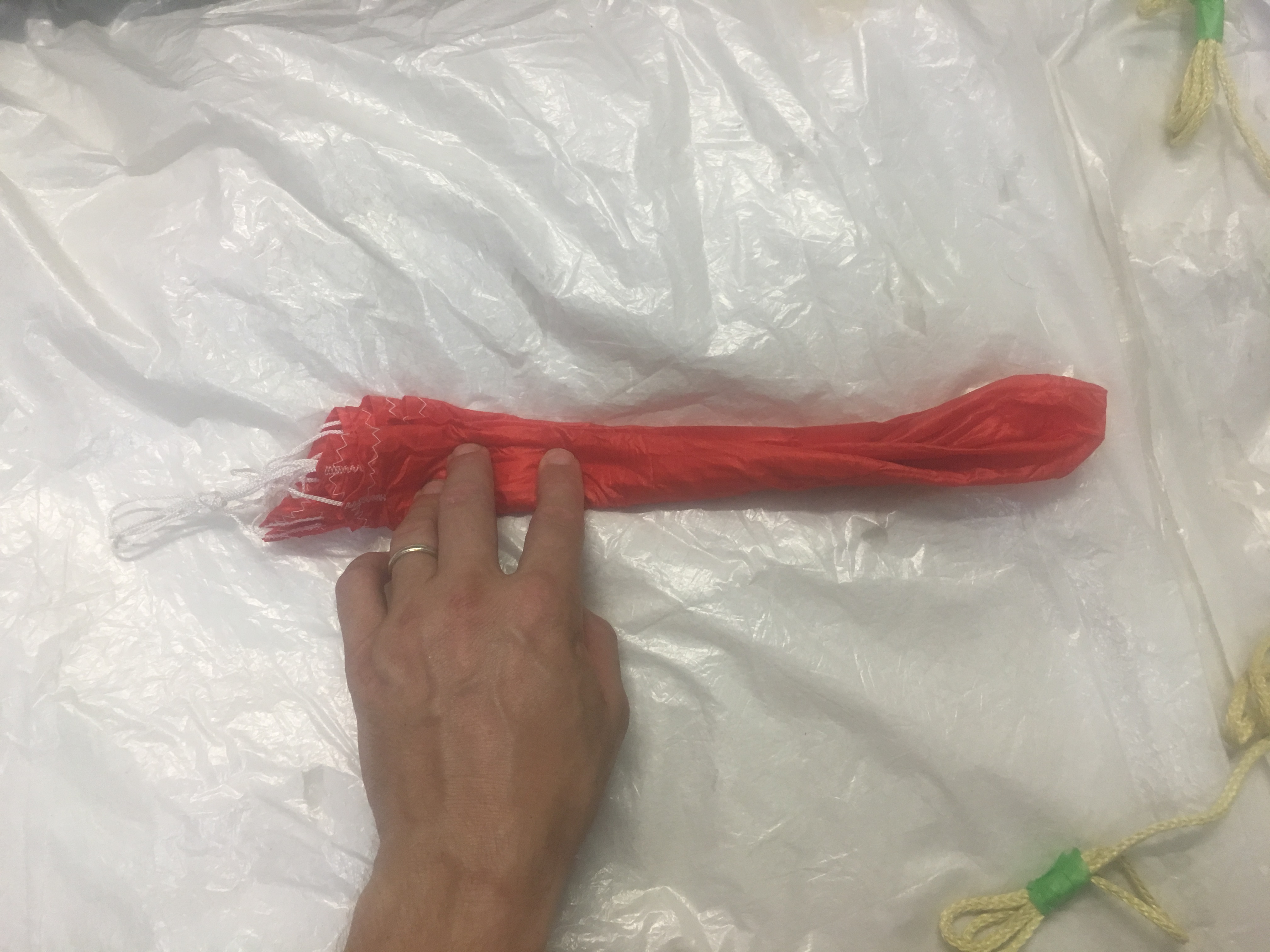
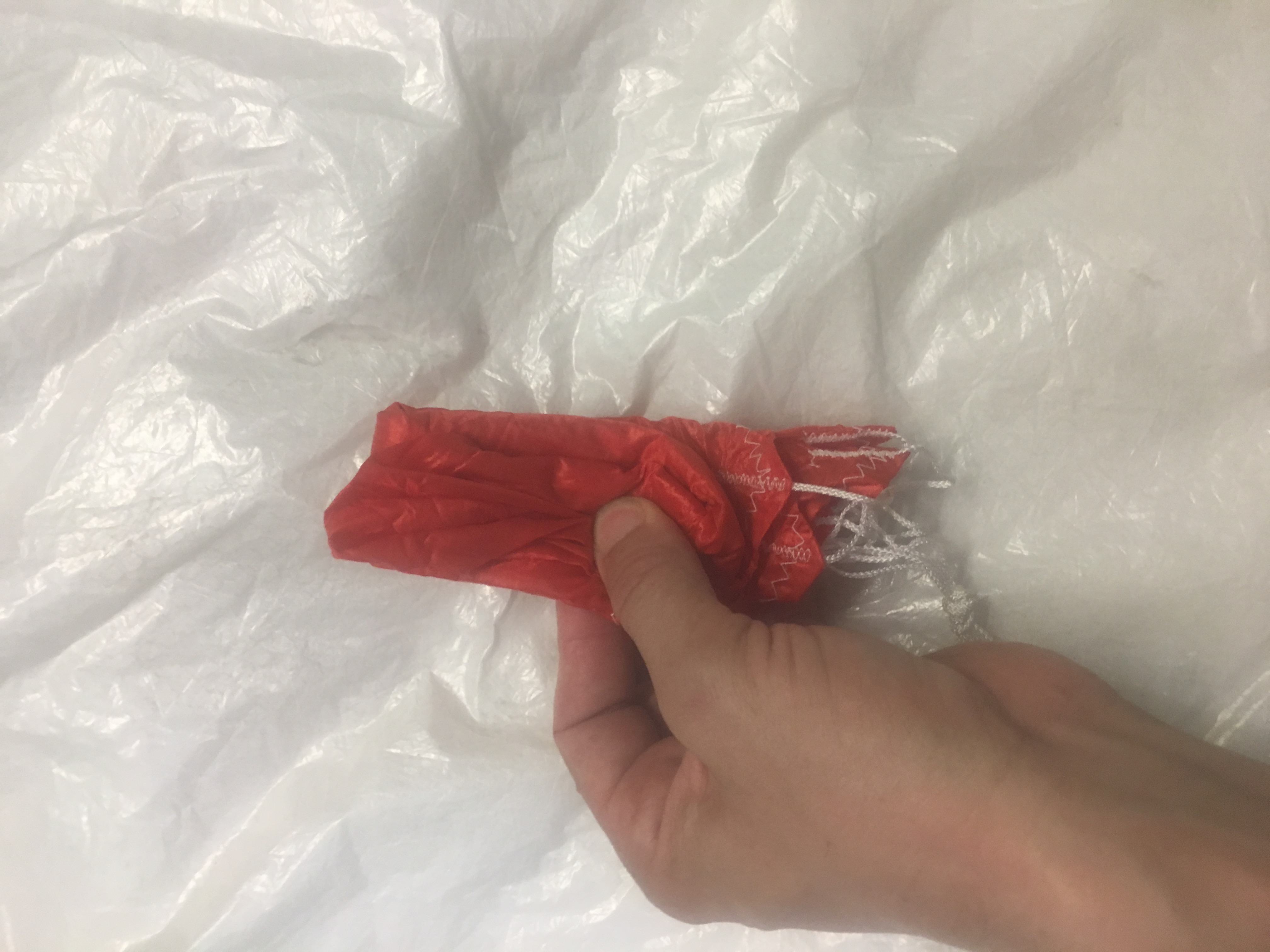
Protecting Parachute with Nomex Blanket
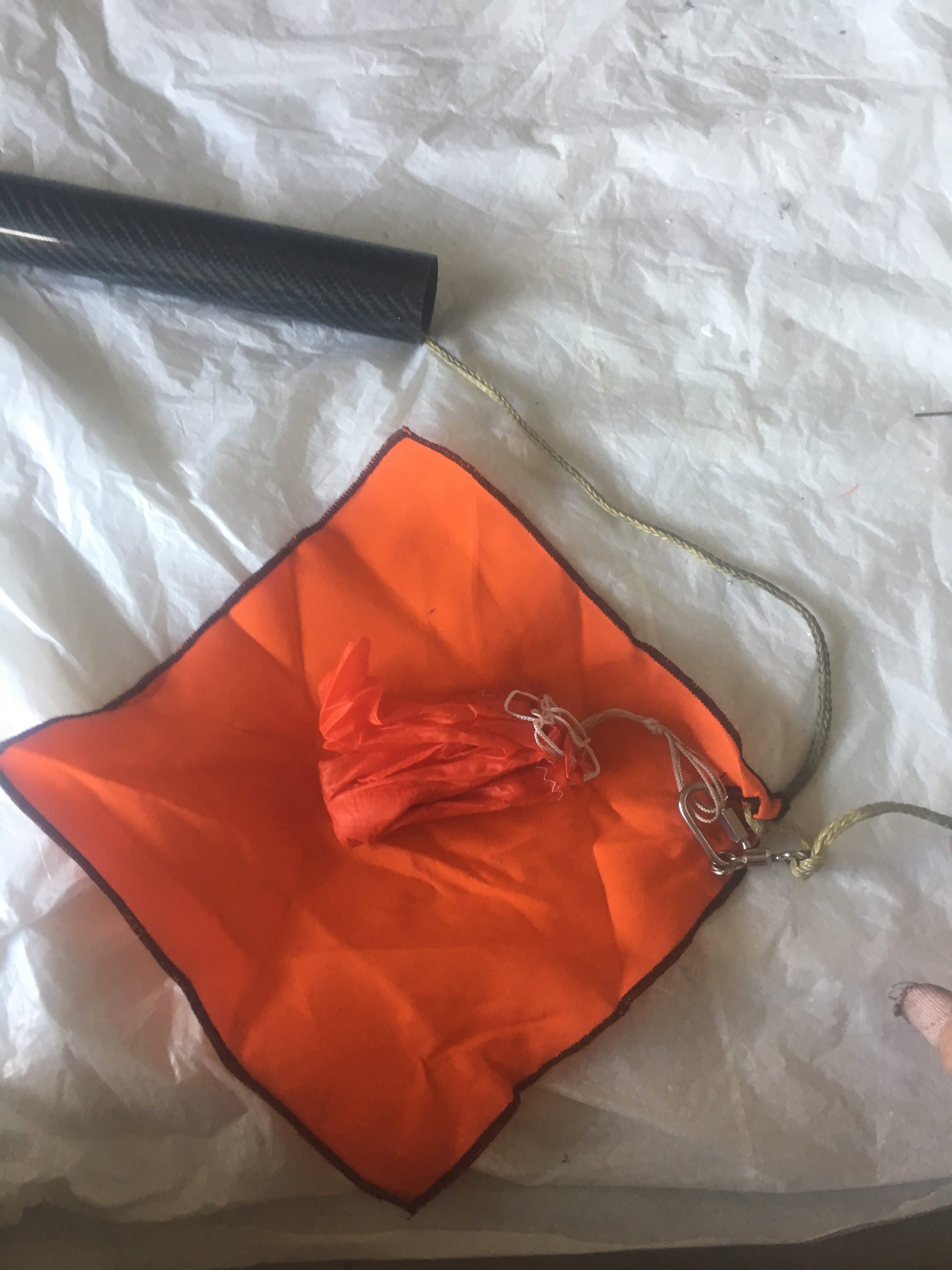
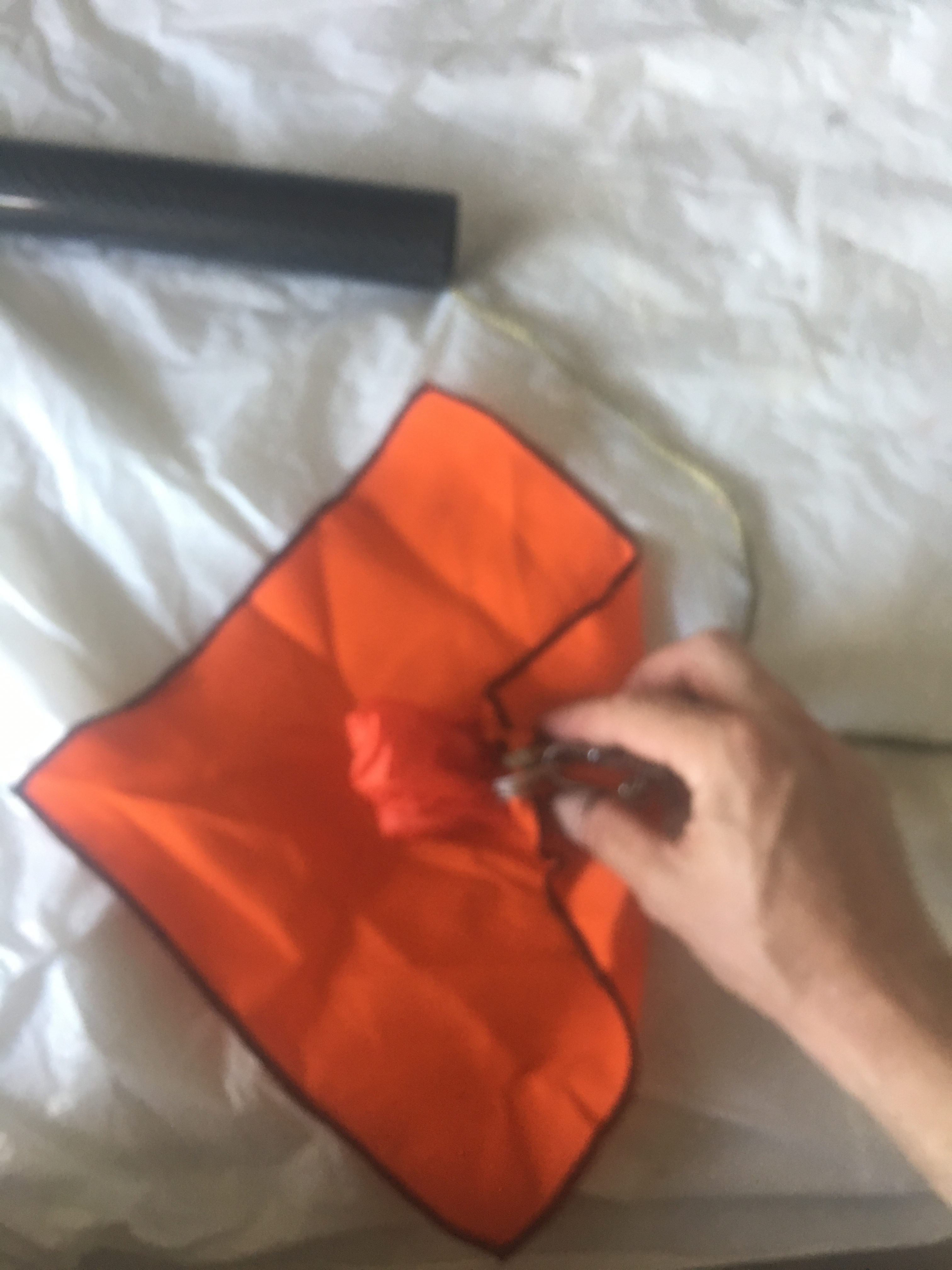
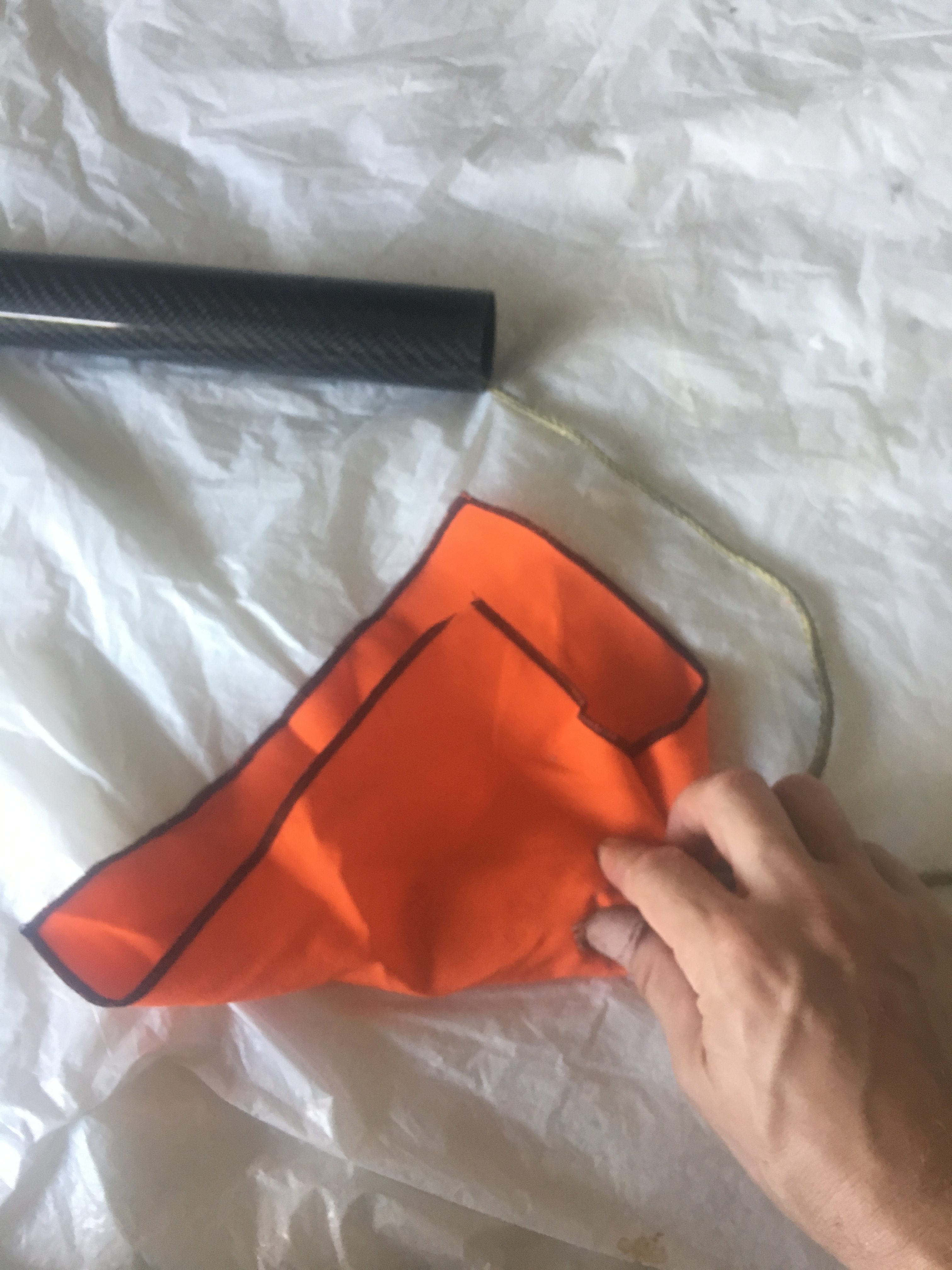
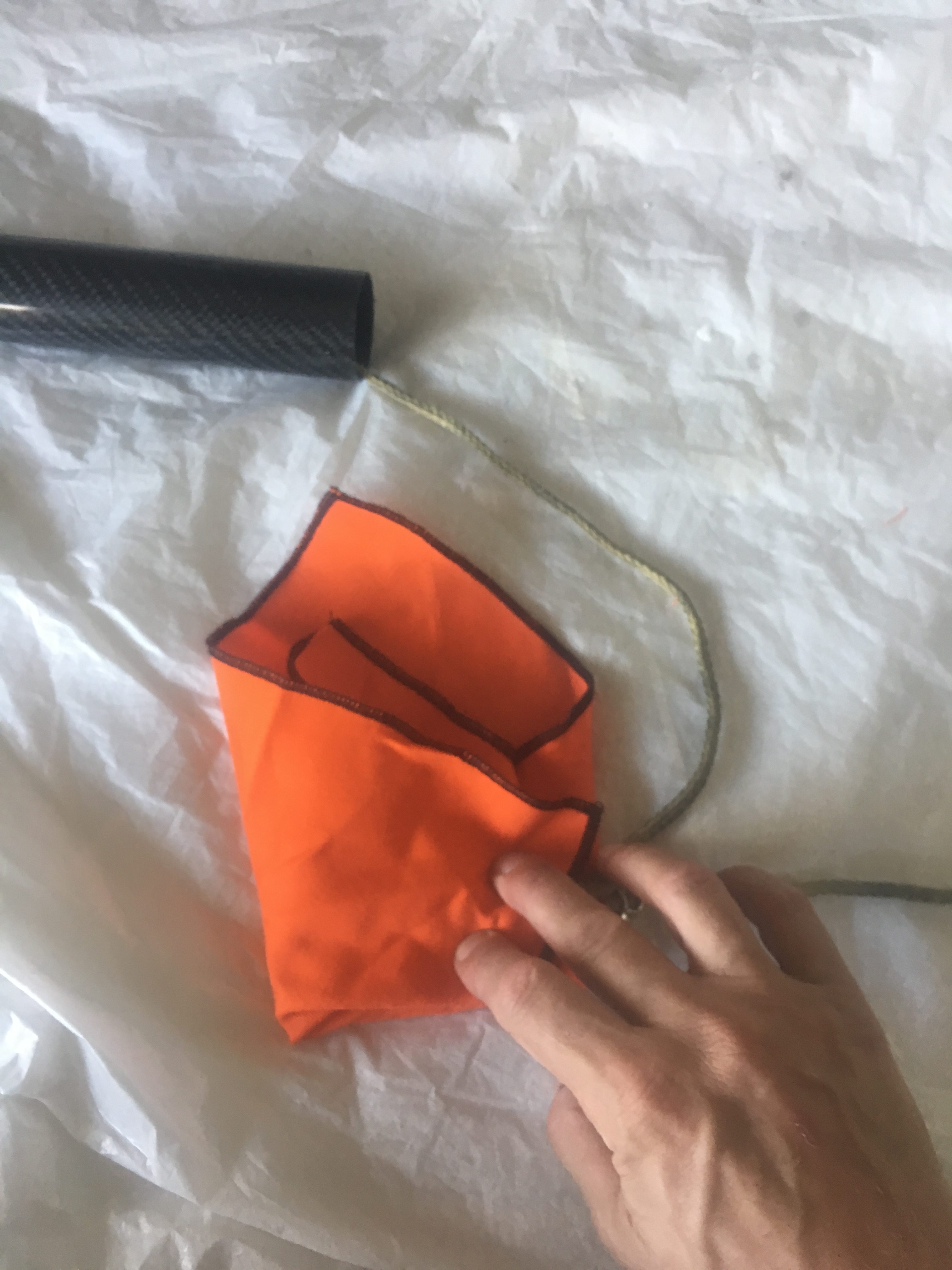
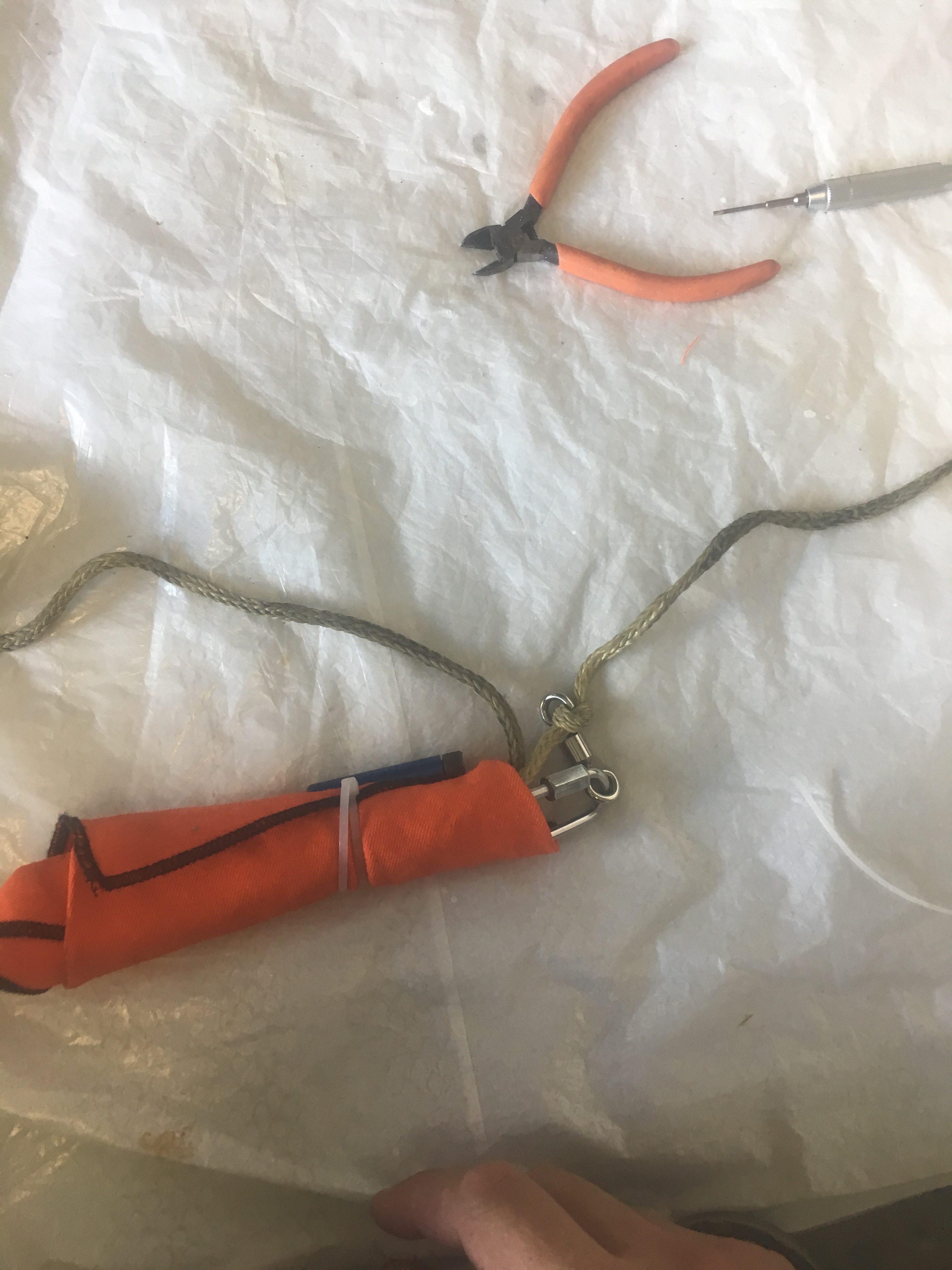
I made double sure that the parachute was attached to the shock-cord and the quick link was taped up.
Loading the recovery systems into the Air-frame.
Here are some photos of how I did it.
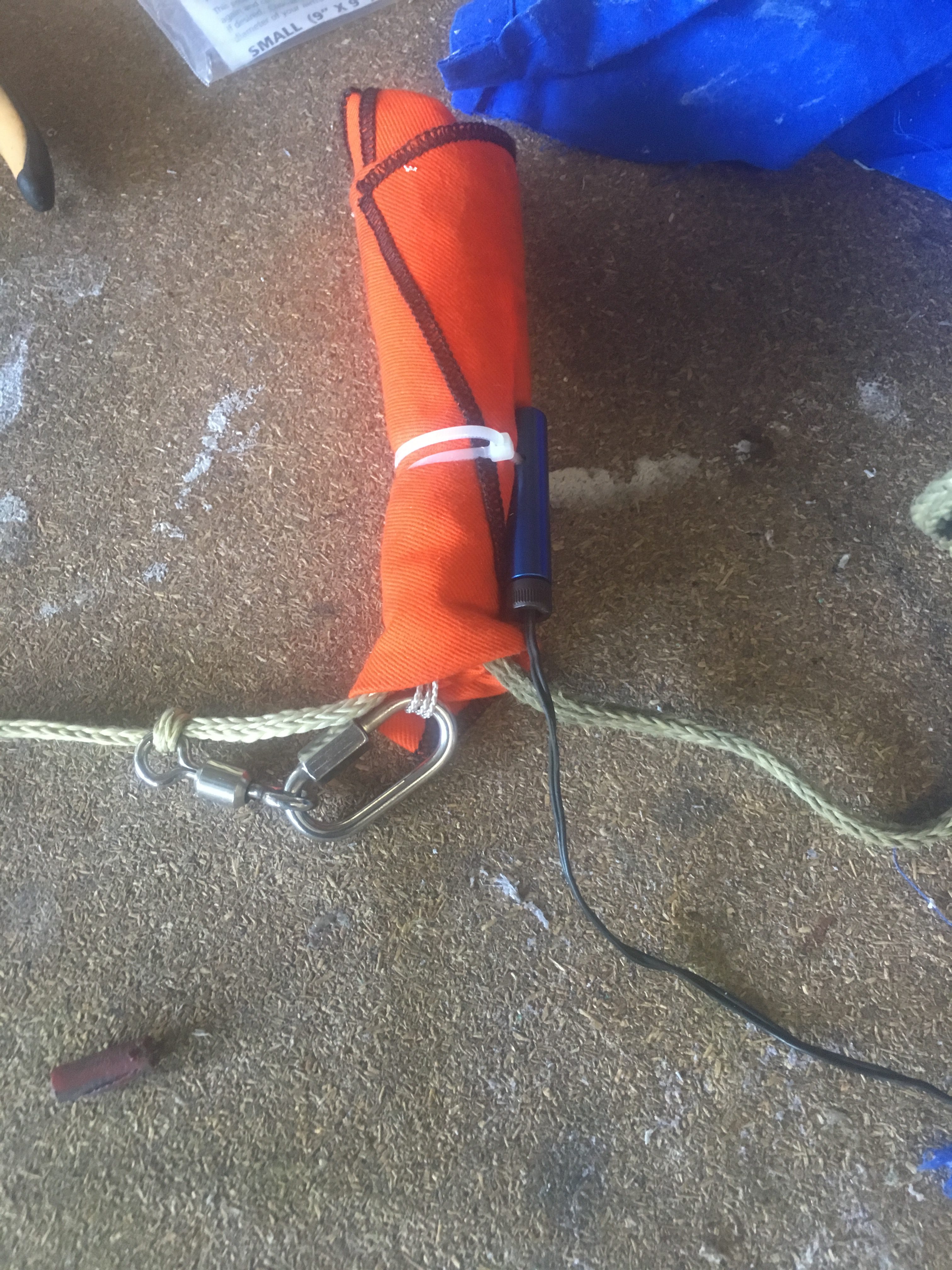
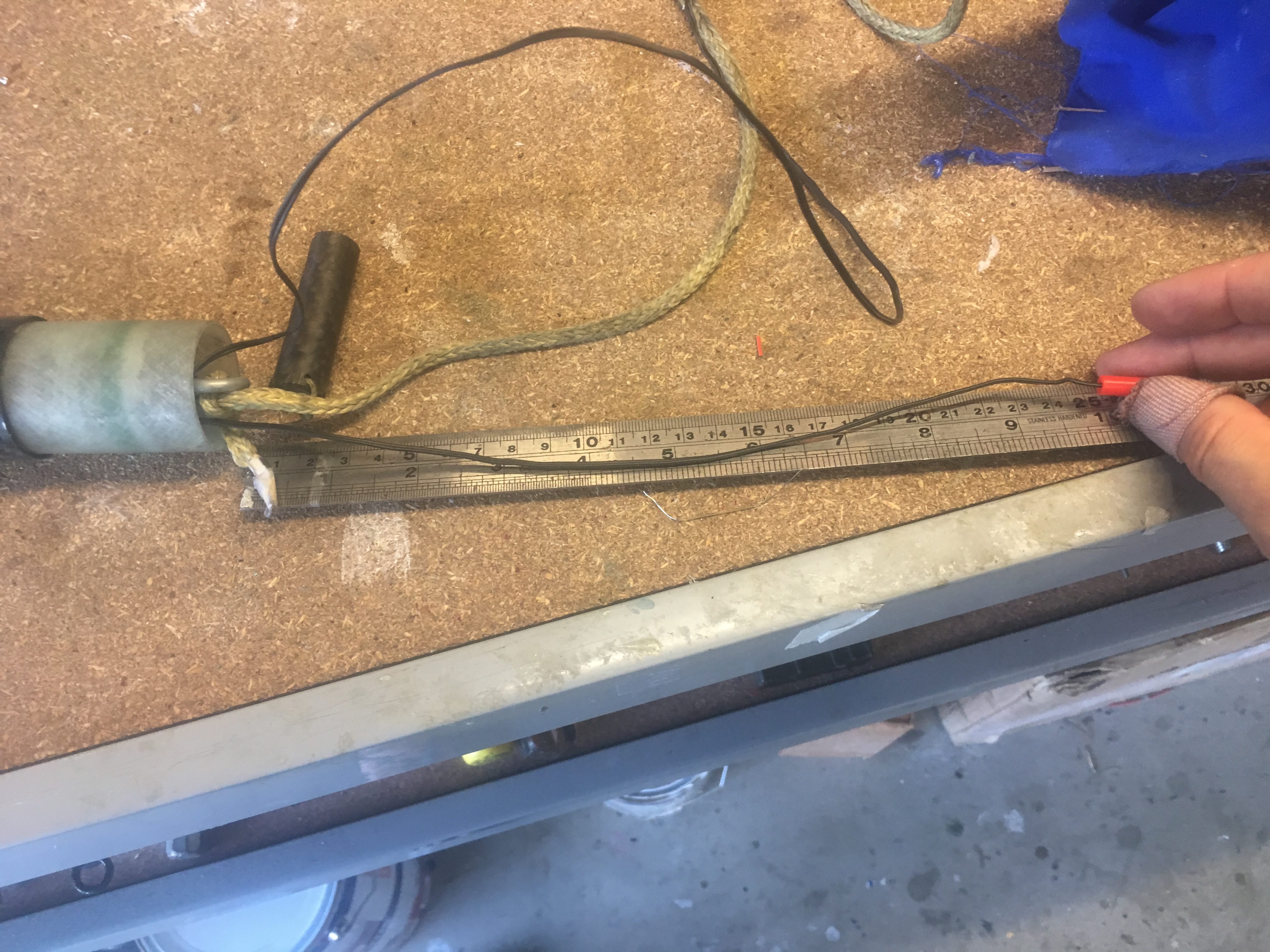
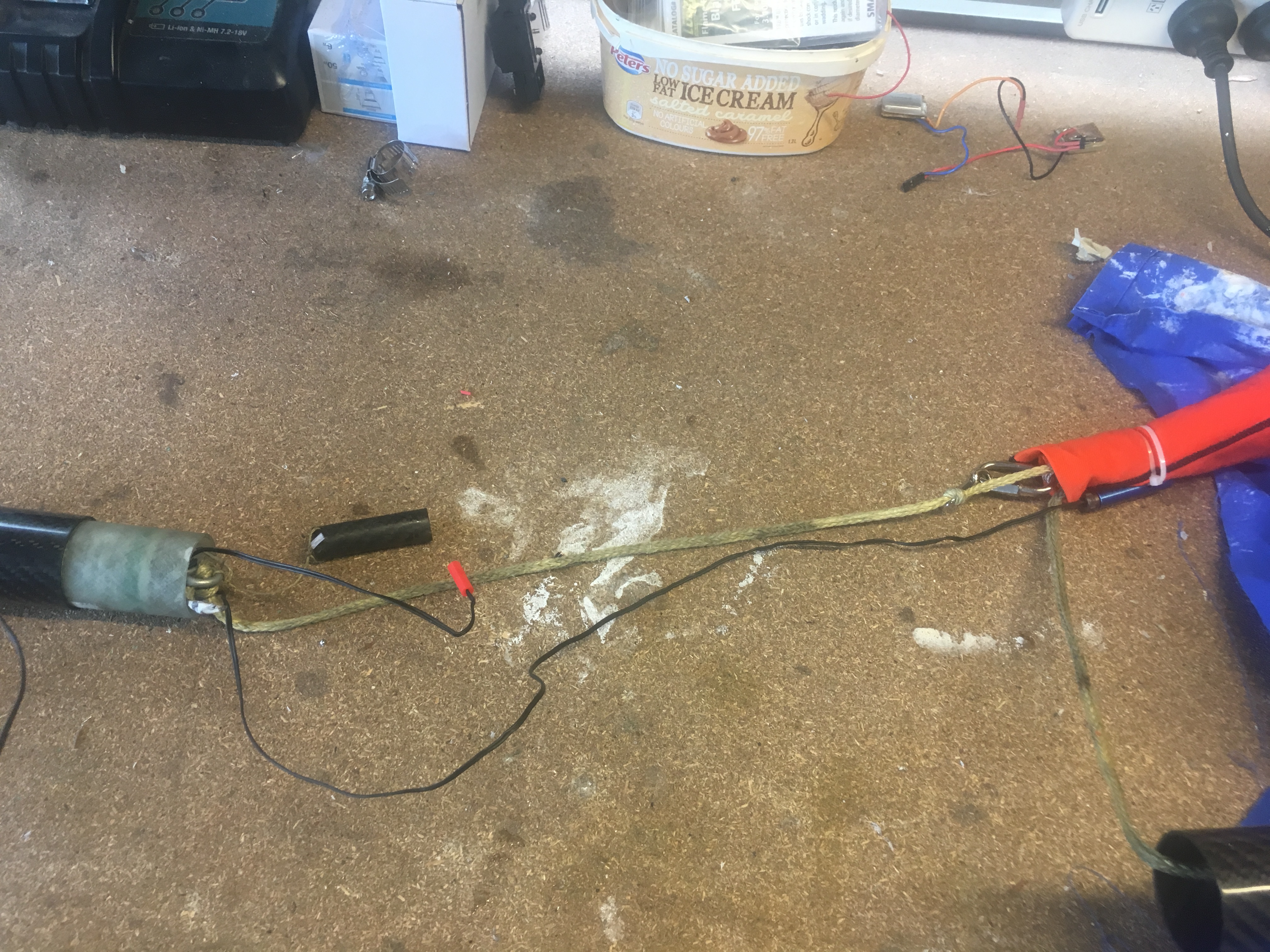
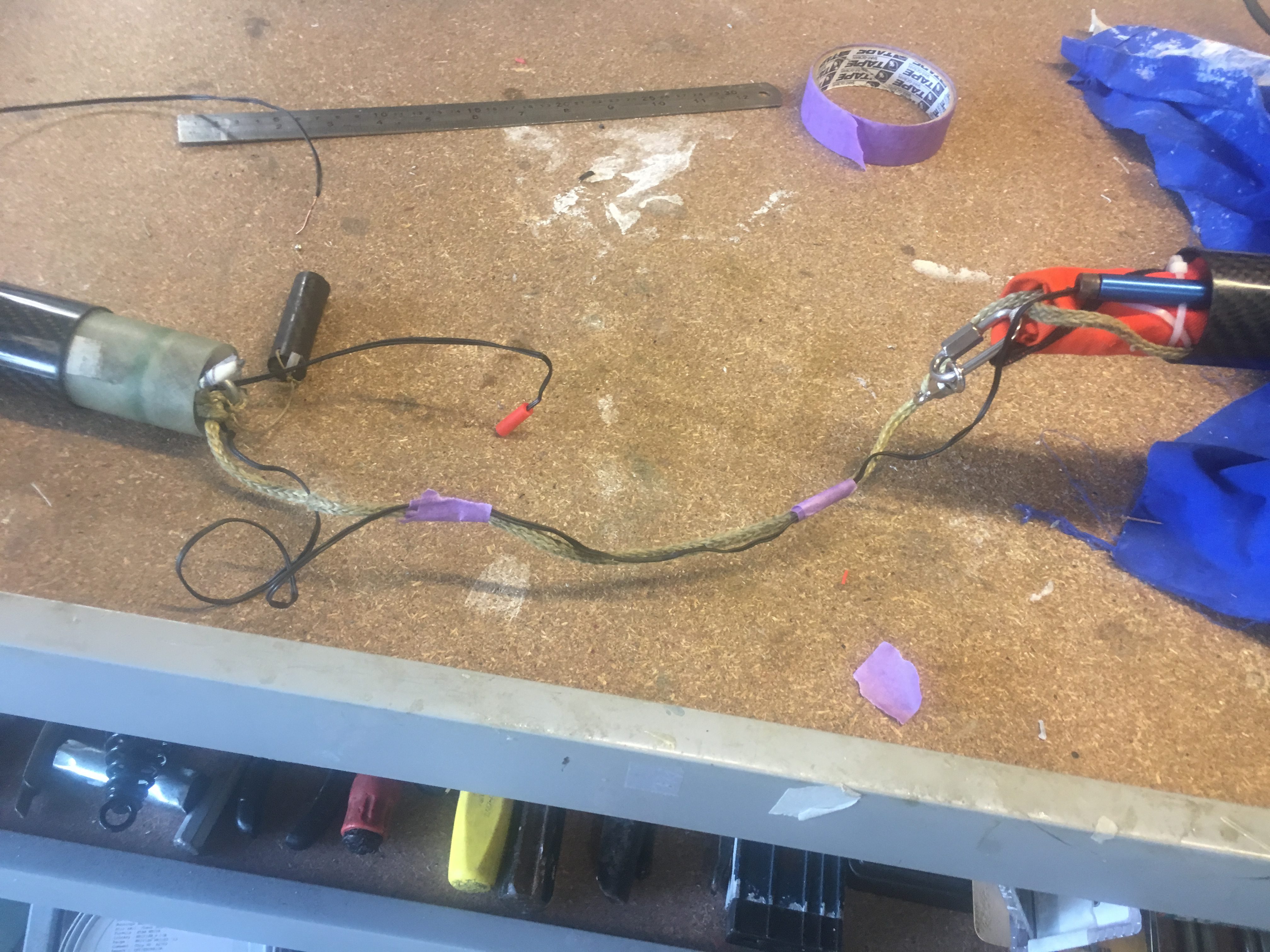
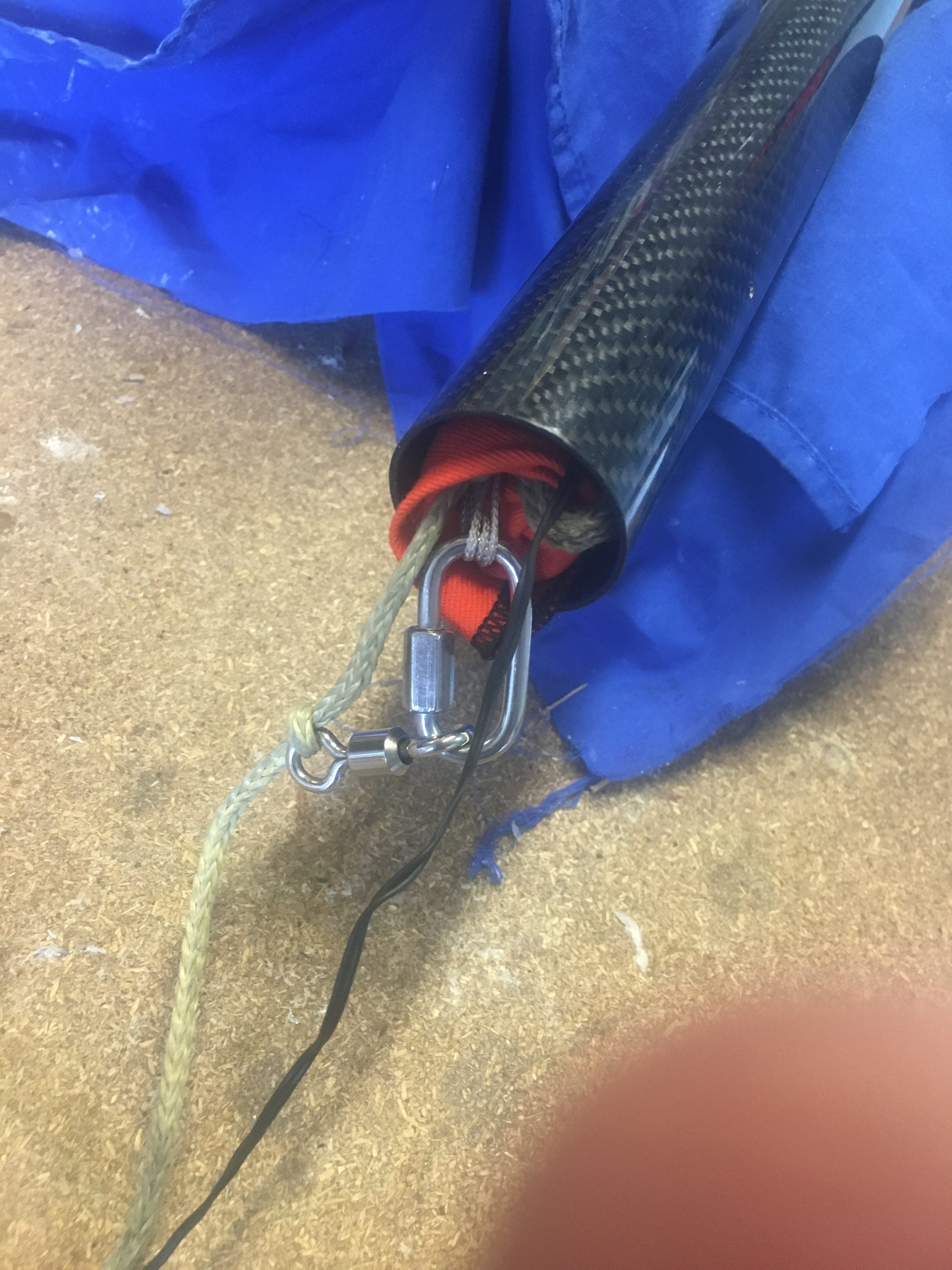
Results of the Ejection Test
After the test we observed:-
- No tangles. Great!
- One of the Z-folds opened up, two left to open up (This is good). The reason this is good is because we expect the load to be “fairly” significant when the parachute inflates and these Z-folds will help reduce load on the rocket components.
- There was no damage to any component (though the charge well is showing some wear after three tests. It is still in good enough condition for use in launches.
- The Cable Cutter still attached to the parachute
- The e-match wiring in-tact
Here are some photos and a movie.
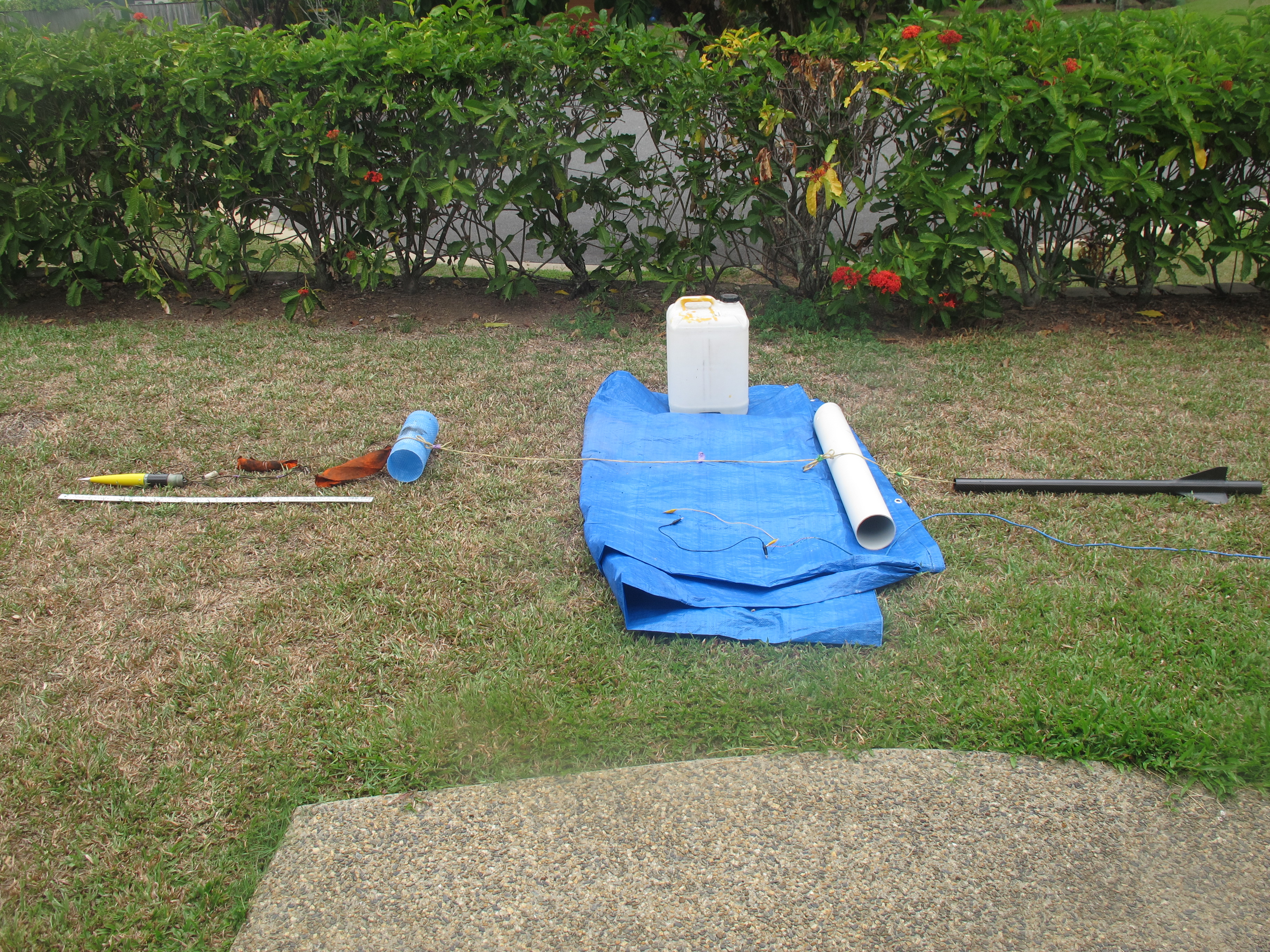
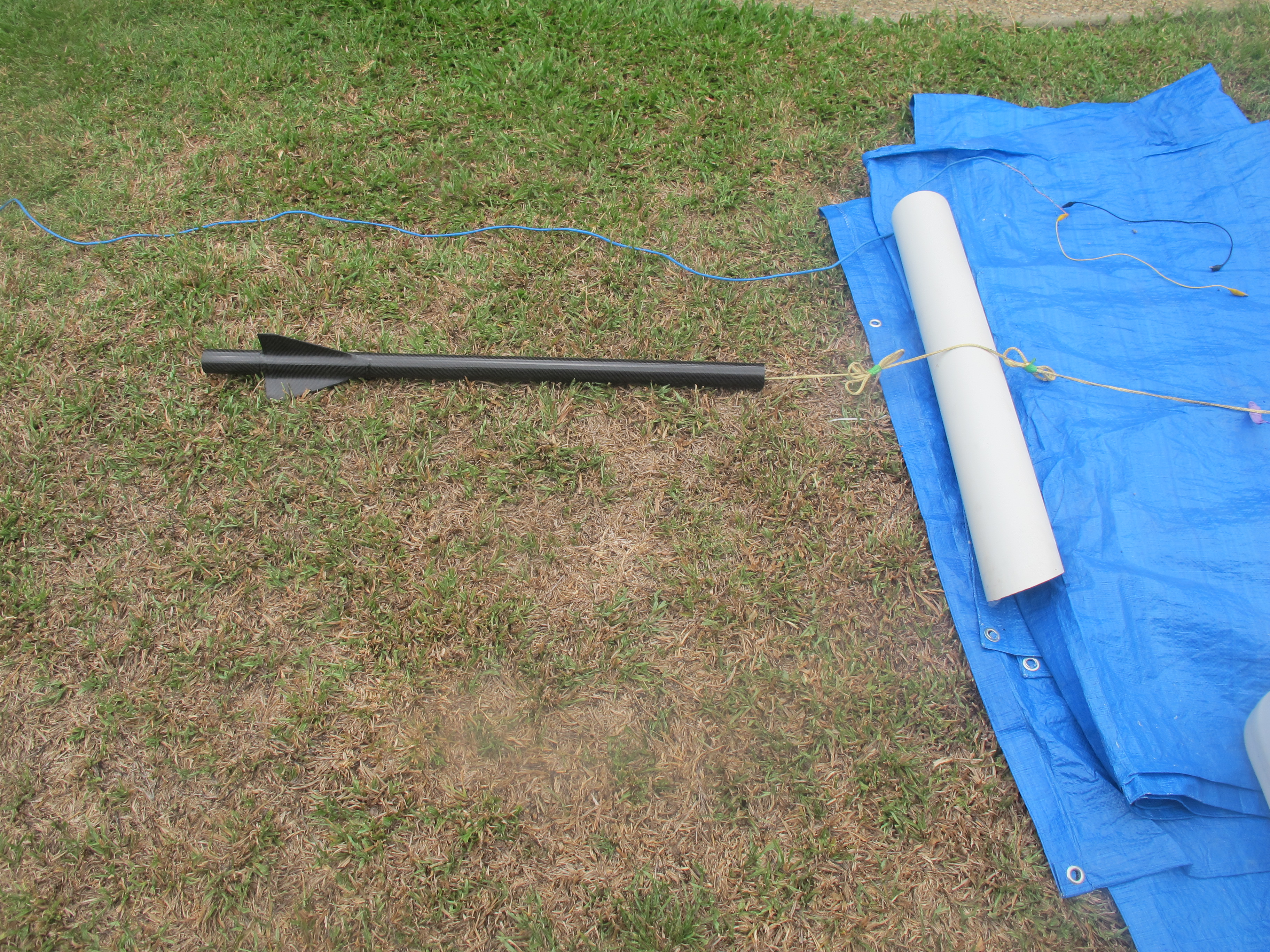
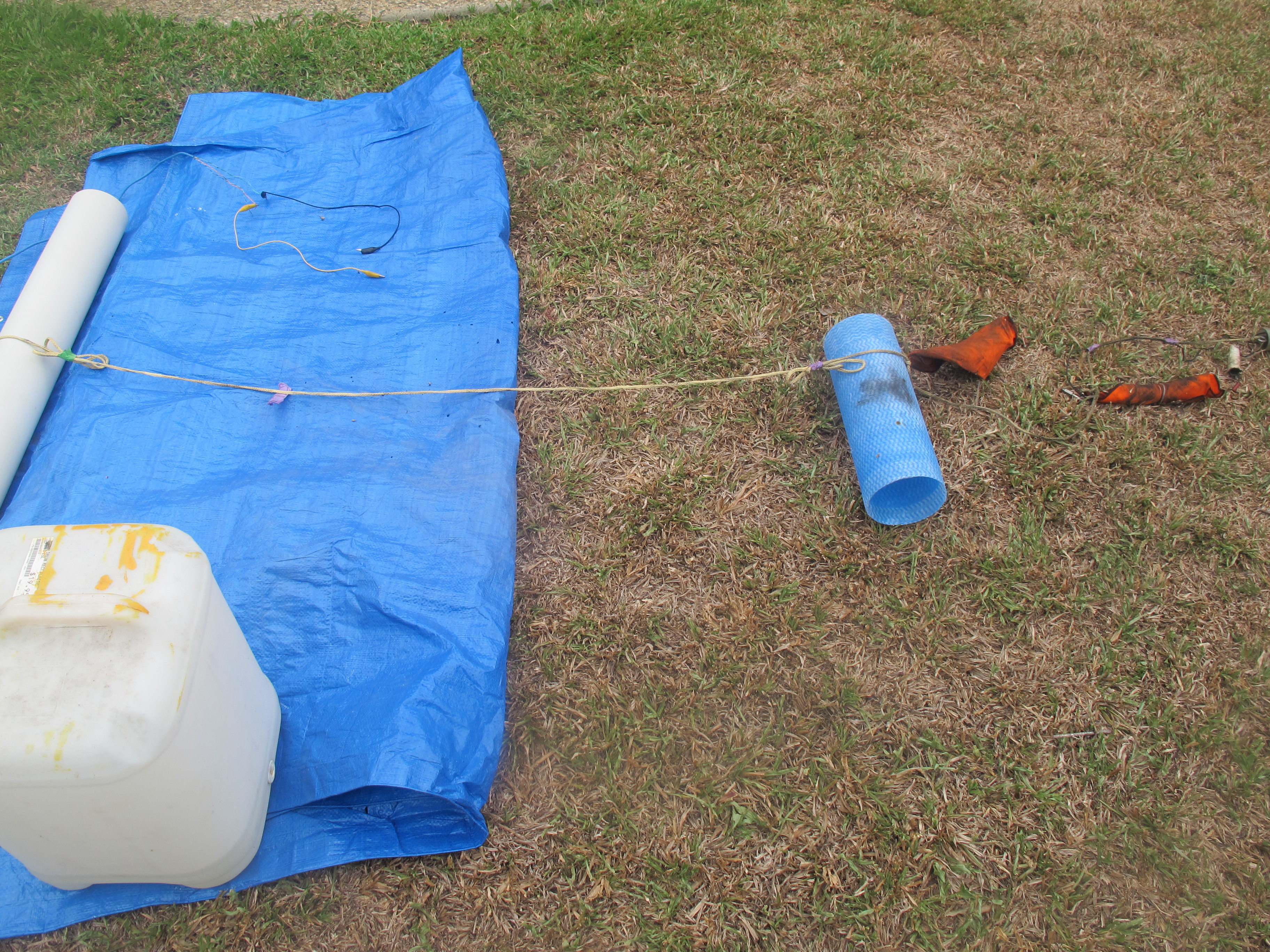

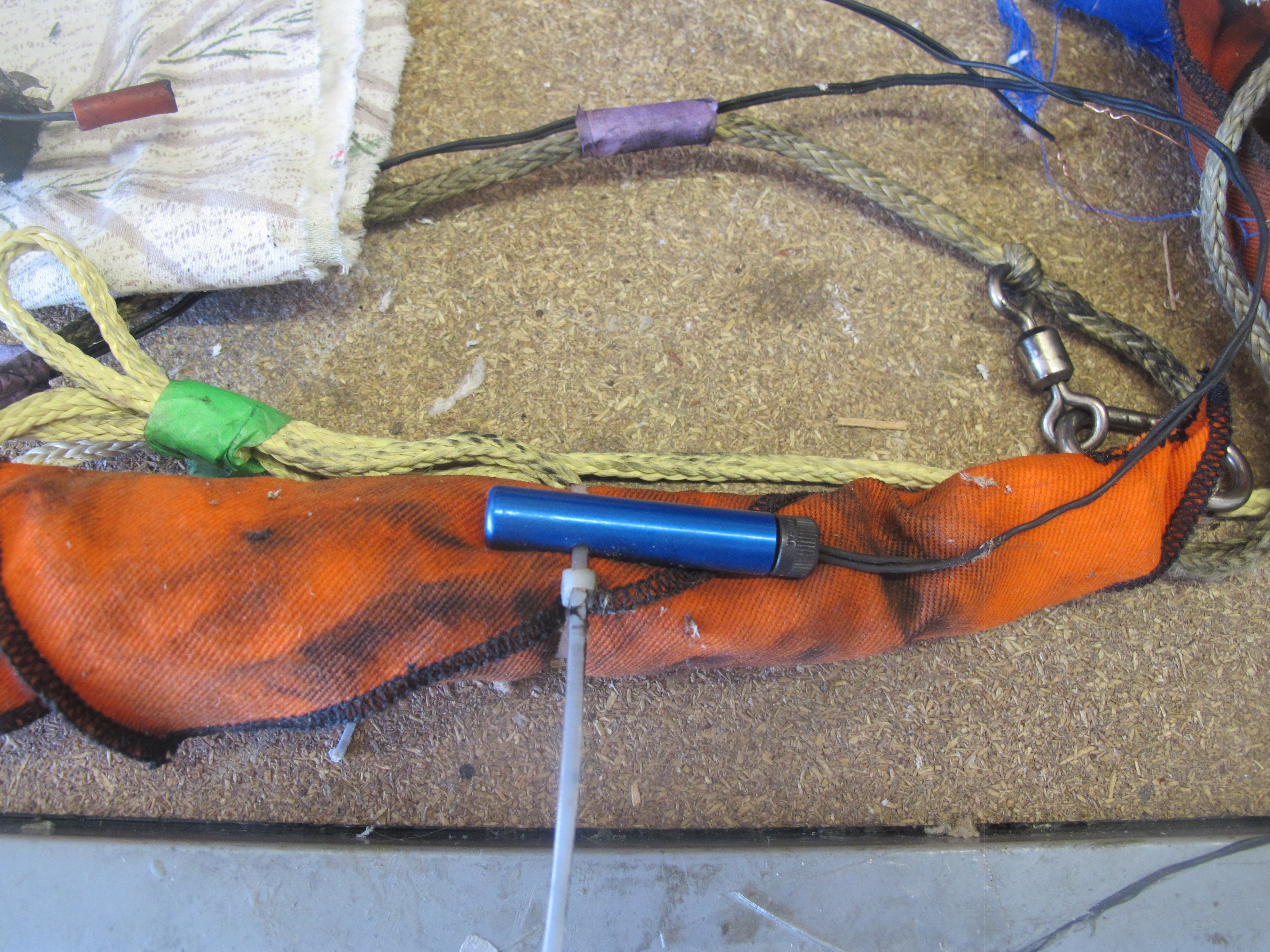
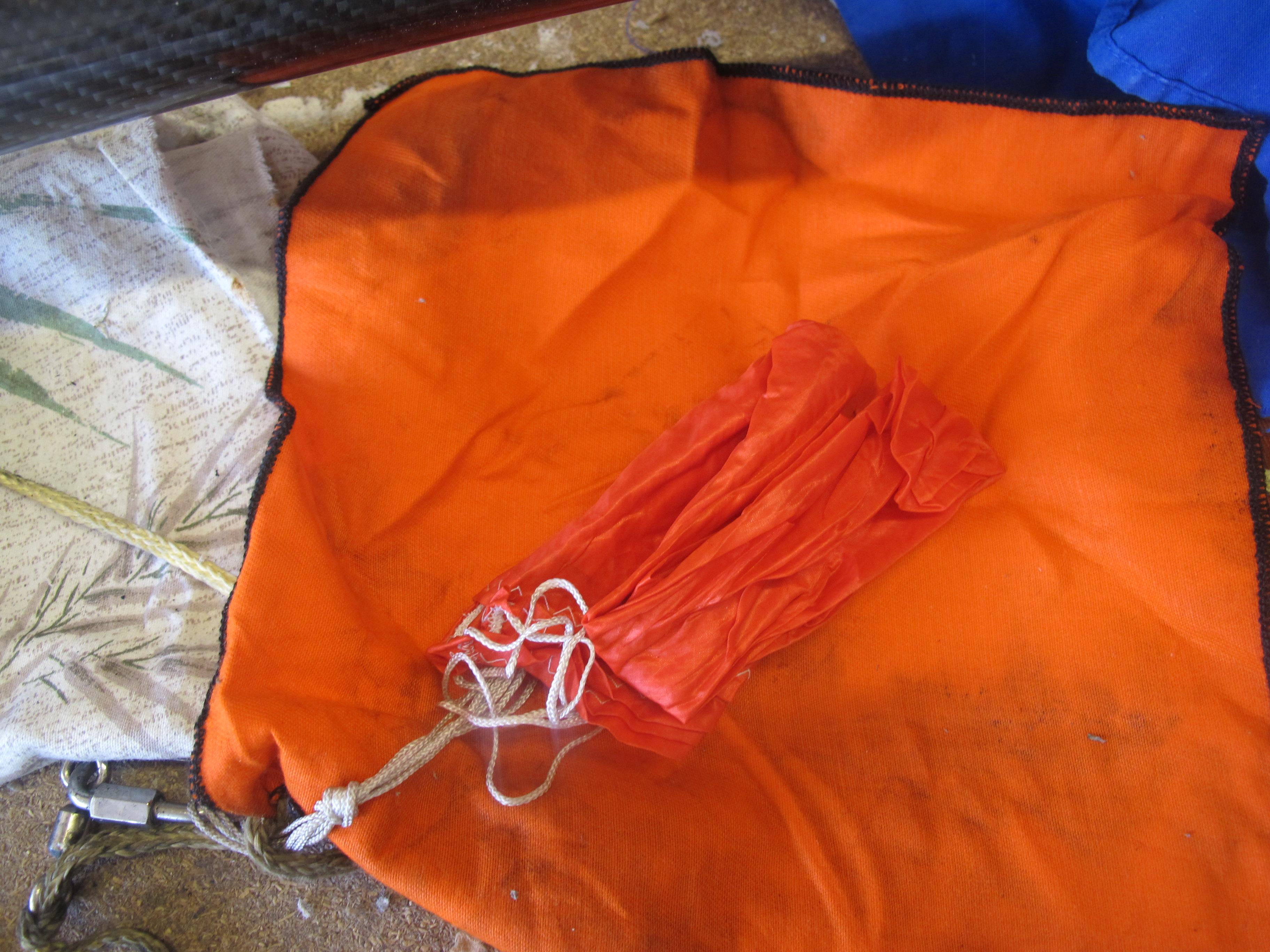