The Cable Cutter
The Cable Cutter I purchased from Aerocon Systems has cambered edges as shown in photo below.
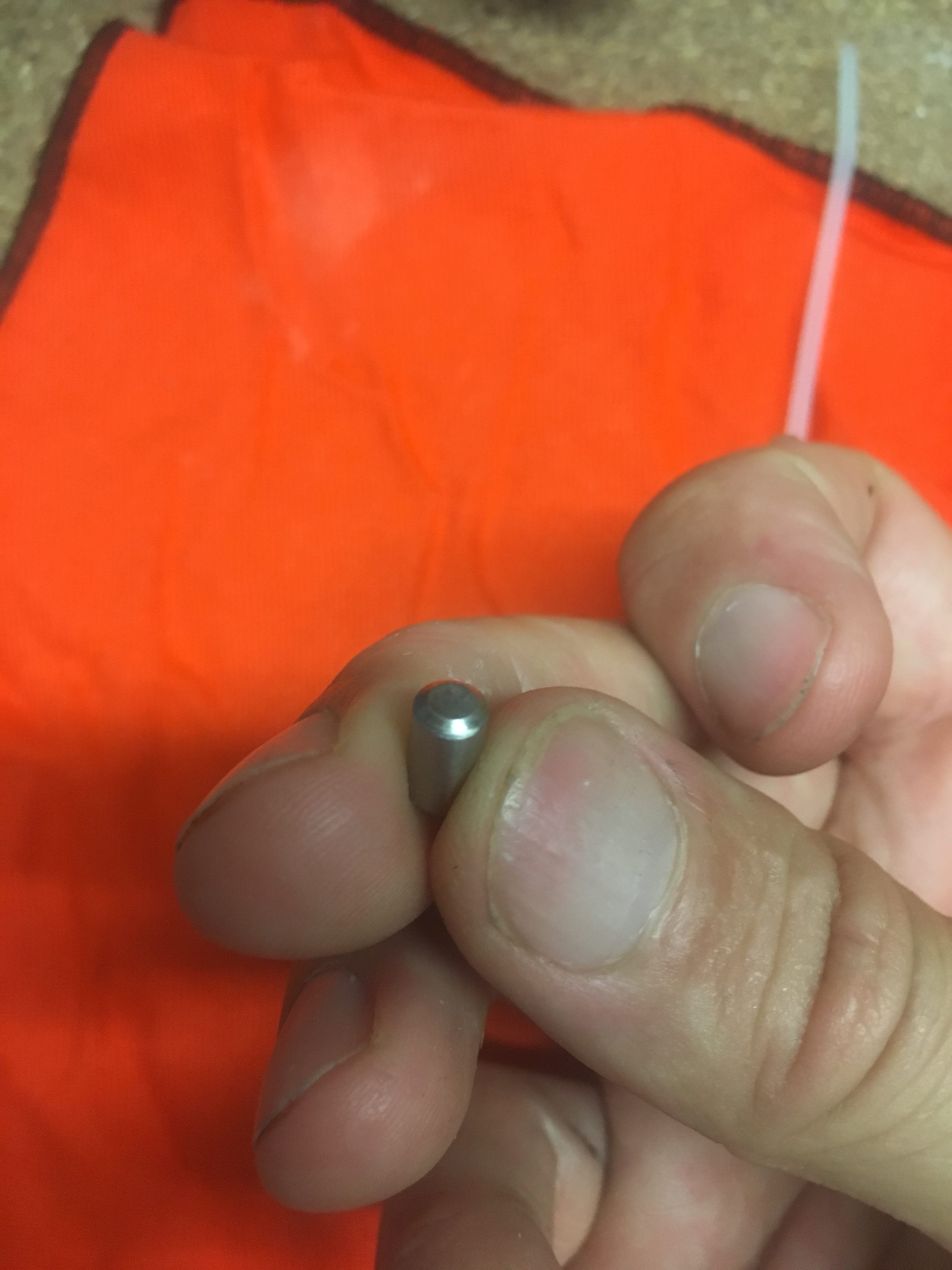
According the supplier, this is normal of these cutters now and is on purpose because the Aluminum cartridge gets damaged from the sharp edge of the piston when too much Black Powder is inserted.
Creating a Cutting Edge
I decided that I would introduce some sharp edges because it just didn’t cut on my first test; and if it doesn’t cut the cable tie, it is of no use to me. So I drilled about 3mm into each end with a 2.5mm drill bit. Then I used a counter-sink bit to create a bit of a ‘crater’ with a sharp edge. See photo below.
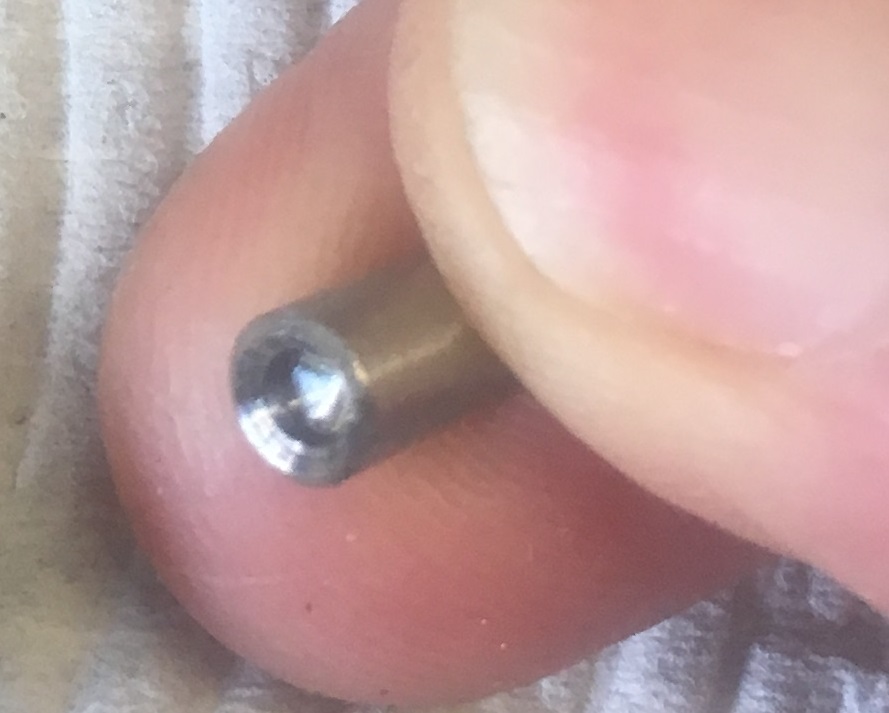
Precise steps were:-
I did this in the vice, very carefully using Aluminum brackets to not distort the steel piston. I marked the center point using pencil under magi light. Then I used punch to mark the center.
I went straight to the 2.5mm drill – special tip and used cutting fluid. It drilled just fine. Then after drilling to a depth ~3mm I used a countersink drill bit to go about 1mm in, to get a “cutting edge” just inside the main diameter.
Assembly
I assembled as follows:-
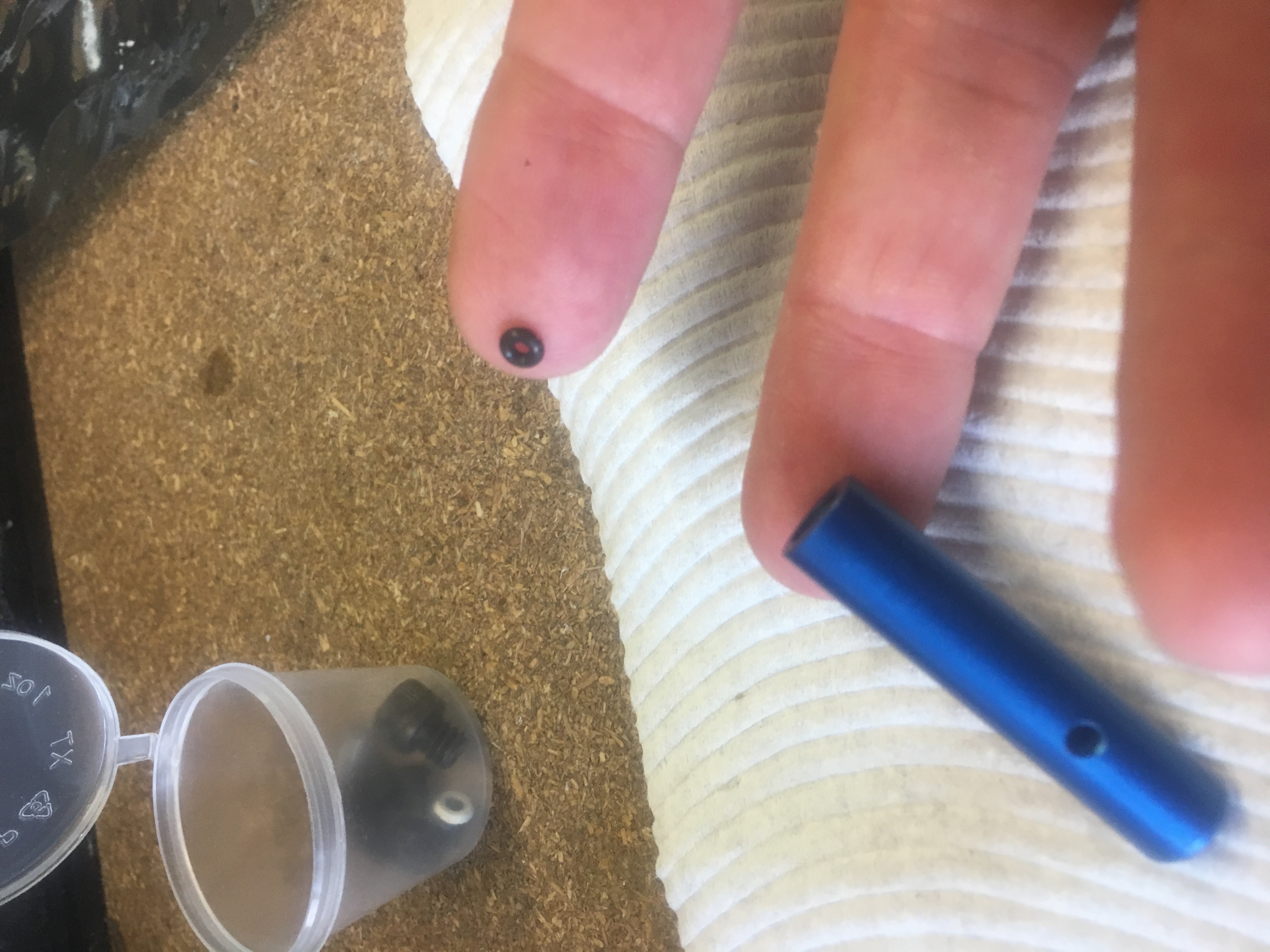
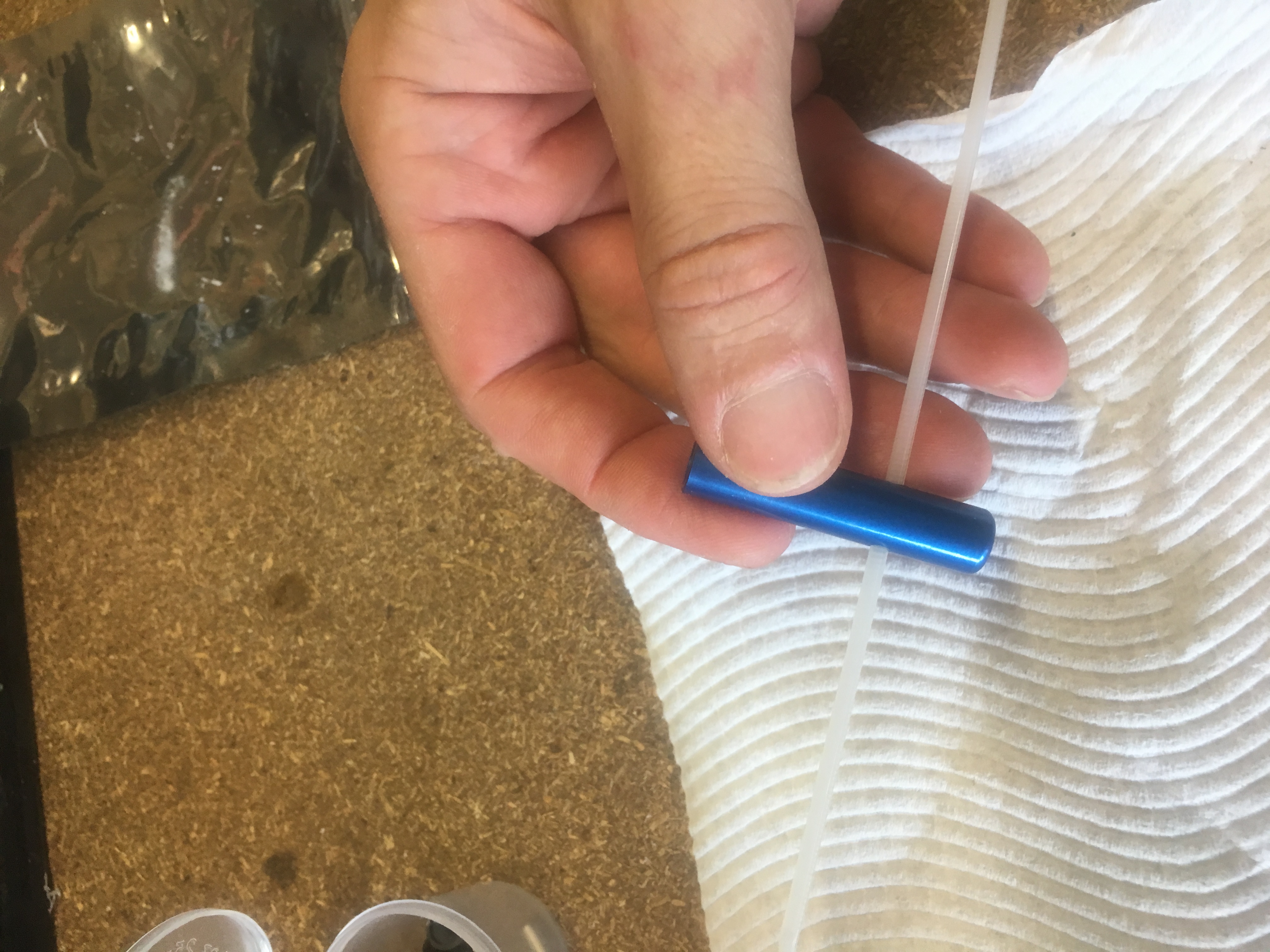
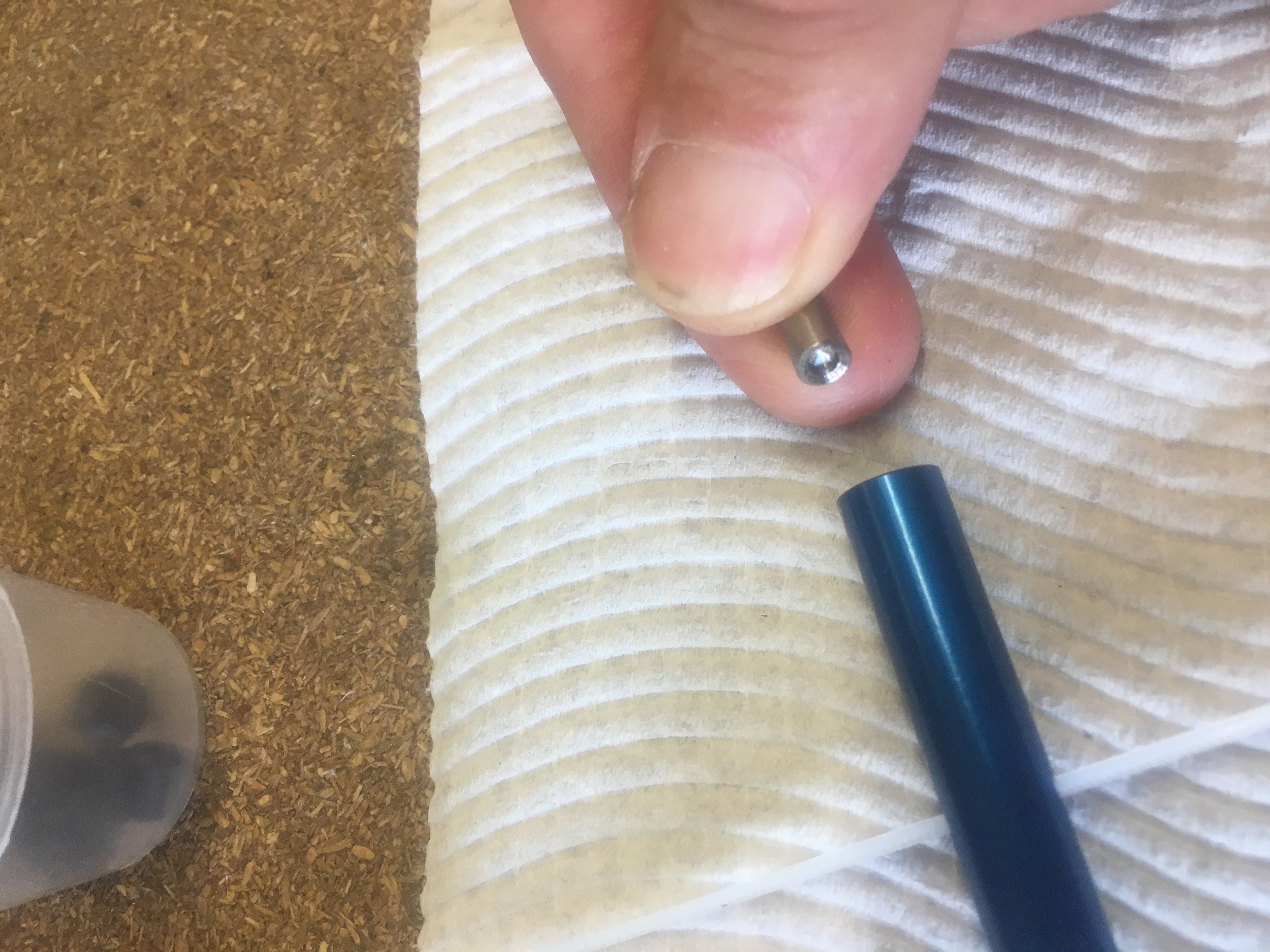
Next I straighted out the e-Match and took the red plastic protector off it. Then I rolled on a small O-ring. The O-ring has two functions:-
- To help seal the cylinder, reduce amount of gas coming out
- To stop shorting of the igniter contacts on the hex screw end bit.
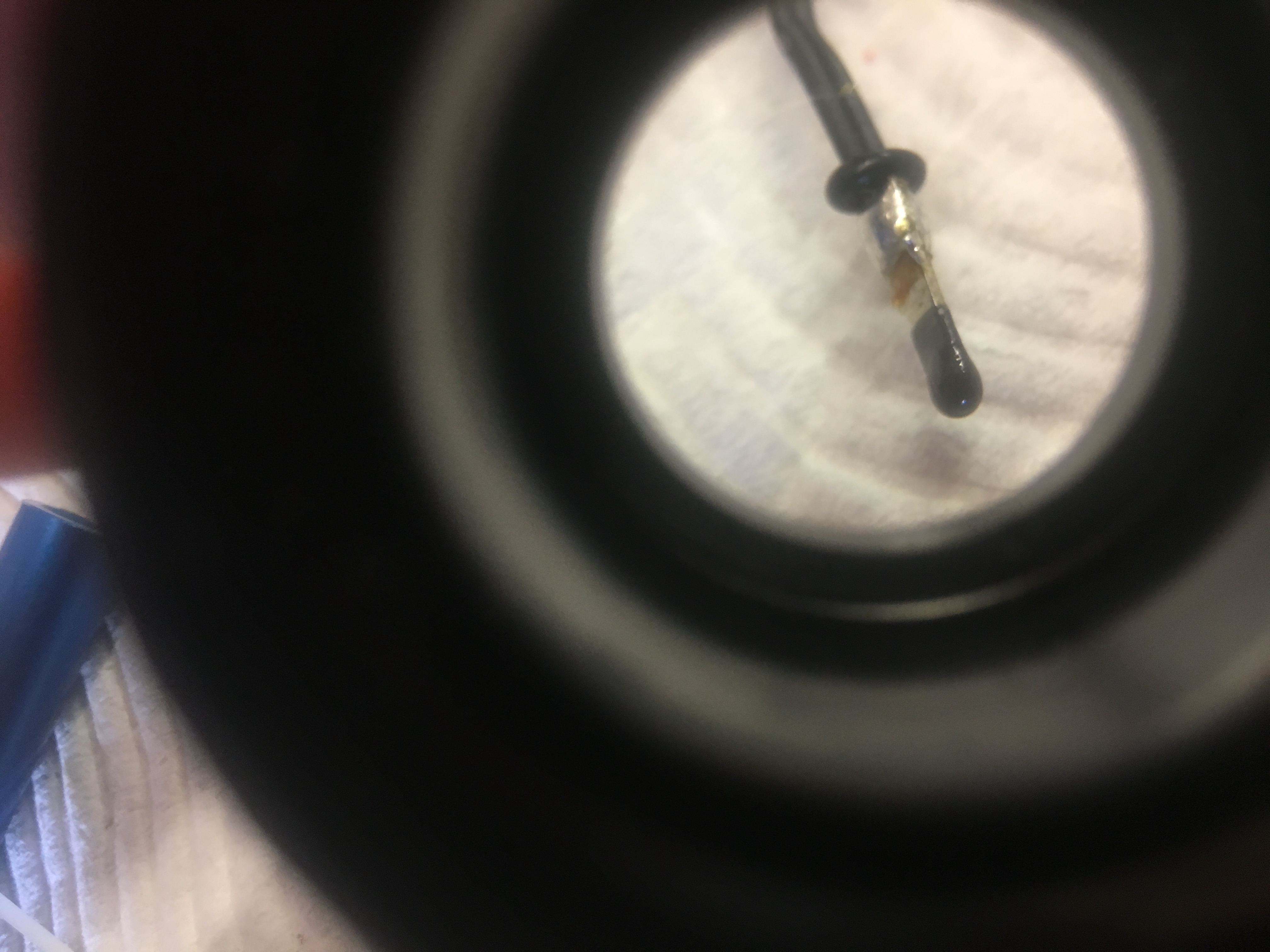
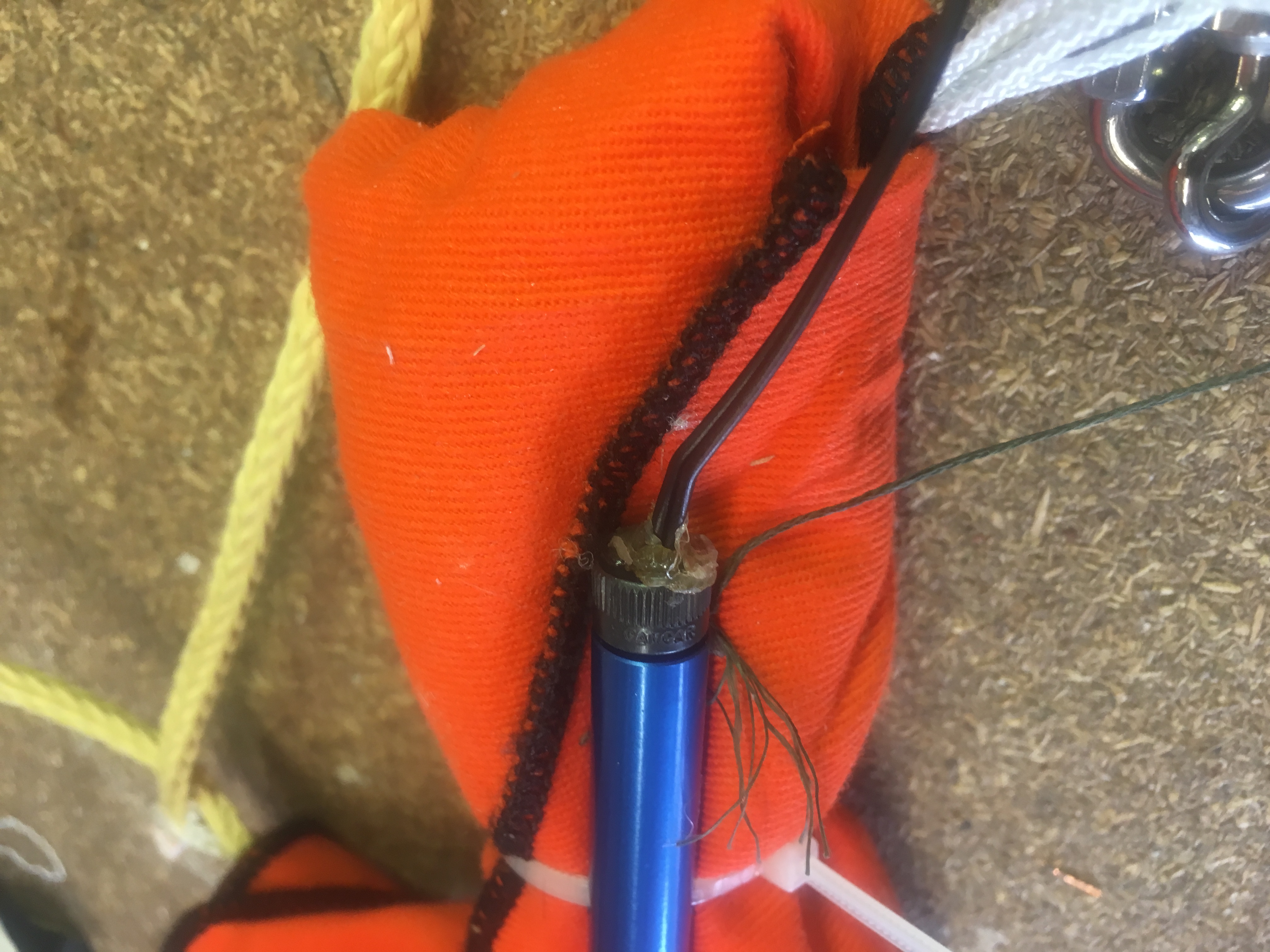
I then melted some hot glue on the end.
Then afterwards, I removed the screw bit…and put the measured 0.1 grams of black powder in.
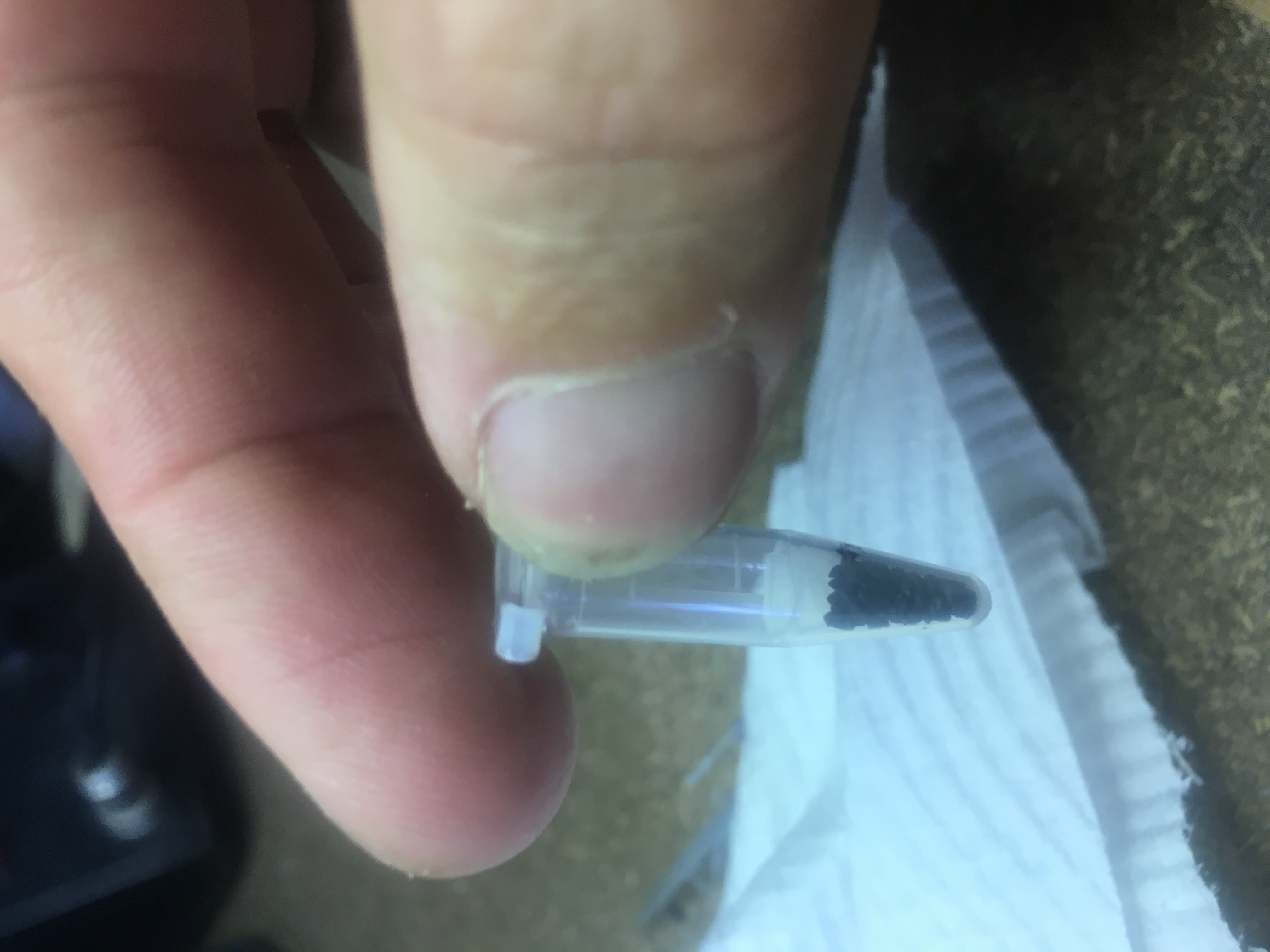
Then I screwed it back together again.
The test
Below is a video of the test.
Very happy with it!