A decision has been made to wind our own NoseCone. (Why Stop at the air-frame?)
The Design
Decided that a conical Nose cone is probably the best one to go for – because we can define the the surface with simple equations and thus create program that will move the resin bath, rotate the mandrel and turn the dispenser with “relative” ease. It is still a challenging task.
Mandrel Construction
We are going for 3-D printed Mandrel . Being so big, it has to be split up into many smaller pieces and installed on a 12mm Steel shaft.
WP 3D Thingviewer Lite need Javascript to work.
Please activate and reload the page.
I ended up replacing the last “12mm” cylindrical section and replacing it with a modified version. This was done because we realised that because the carbon fiber layup at the tip is going to be thicker than at the other end, we need to compensate for this with a narrower Mandrel – else we will NOT get the cone shape we are after. The Nose Cone would have been concave.
The Laydown of Carbon Fiber
Working out the mathematics for laying down the Carbon Fiber has been a challenge. The Carbon Fiber needs to follow straight lines (geodesics) to ensure minimal slippage of Carbon Fiber to produce the best Nose Cone possible.
There is more to the conical section of the Nose Cone, there is also the Cylindrical part. The Carbon Fiber from the Cylindrical part needs to “marry up” with the Carbon Fiber of the Cone part – no horribly bunching up. i.e. we need to continuous (well-formed) surface to wind around and for the CF Angle (with respect to the mandrel axis) to be the same at the interface.
Initially, we tried:-
- 0 degrees
- 90 degrees
- 180 degrees
- 270 degrees
- 360 degrees (back to the beginning)
On the 5th pass, we move the Advancement angle amount. Then I thought it would be good to try and reduce the bunching of Carbon Fiber at the tip by having some adjacent CF. By having adjacent, we effectively double the width of the Carbon Fiber.
- 0 degrees – 160mm from tip
- 0 degrees – 165mm from tip
- 90 degrees – 160mm from tip
- 90 degrees – 165mm from tip
- 180 degrees – 160mm from tip
- 180 degrees – 165mm from tip
- 270 degrees – 160mm from tip
- 270 degrees – 165mm from tip
- <<ADVANCE TWO x advancement amounts>>
- 360 degrees (back to the beginning)
In 2-D it looks like: –
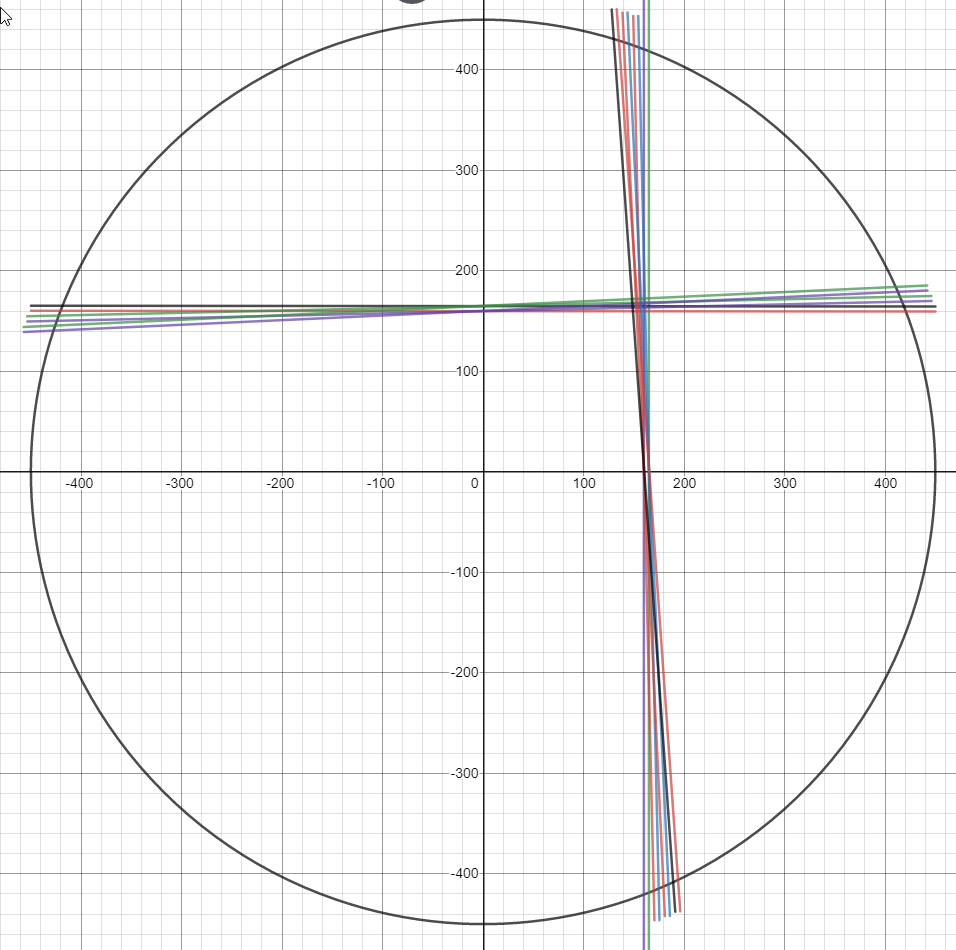
In the end, decided to not have adjacent CF laydowns and instead space them around the whole Nose Cone. This seems to produce a more even layup.
It was calculated that we needed 45.1 passes to cover the Cone. We decided to go for 48. This is a nice number and the additional passes ensure coverage.
We use a function to help “spread” the laydowns around the nose cone, so it wasn’t one next to the previous one.
So it was
Pass | Place |
---|---|
1 | 2 |
2 | 15 |
3 | 28 |
4 | 41 |
5 | 6 |
6 | 19 |
7 | 32 |
8 | 45 |
9 | 10 |
10 | 23 |
etc.
So For Pass 1, we would move 2 x (360 / 45) = 16 degrees. Then for the Second Pass, we would do it at 15 x (360 / 45) = 120 degrees… and so on.
How did we calculate this?
We have two functions that we use to generate this value.
(1) y = (pass -1)* 12 + pass
(2) z = (y/48 - floor(y/48))*48 + 1
The second function just ensures that the offset value is the smallest offset value. i.e. it doesn’t rotate the spindle around excessively.
How did I get this function?
I just played with it a little until I got something that looks like it might spread it out AND very importantly, cover the ENTIRE mandrel after ~48 passes.
The Result
Here are lots of photos.
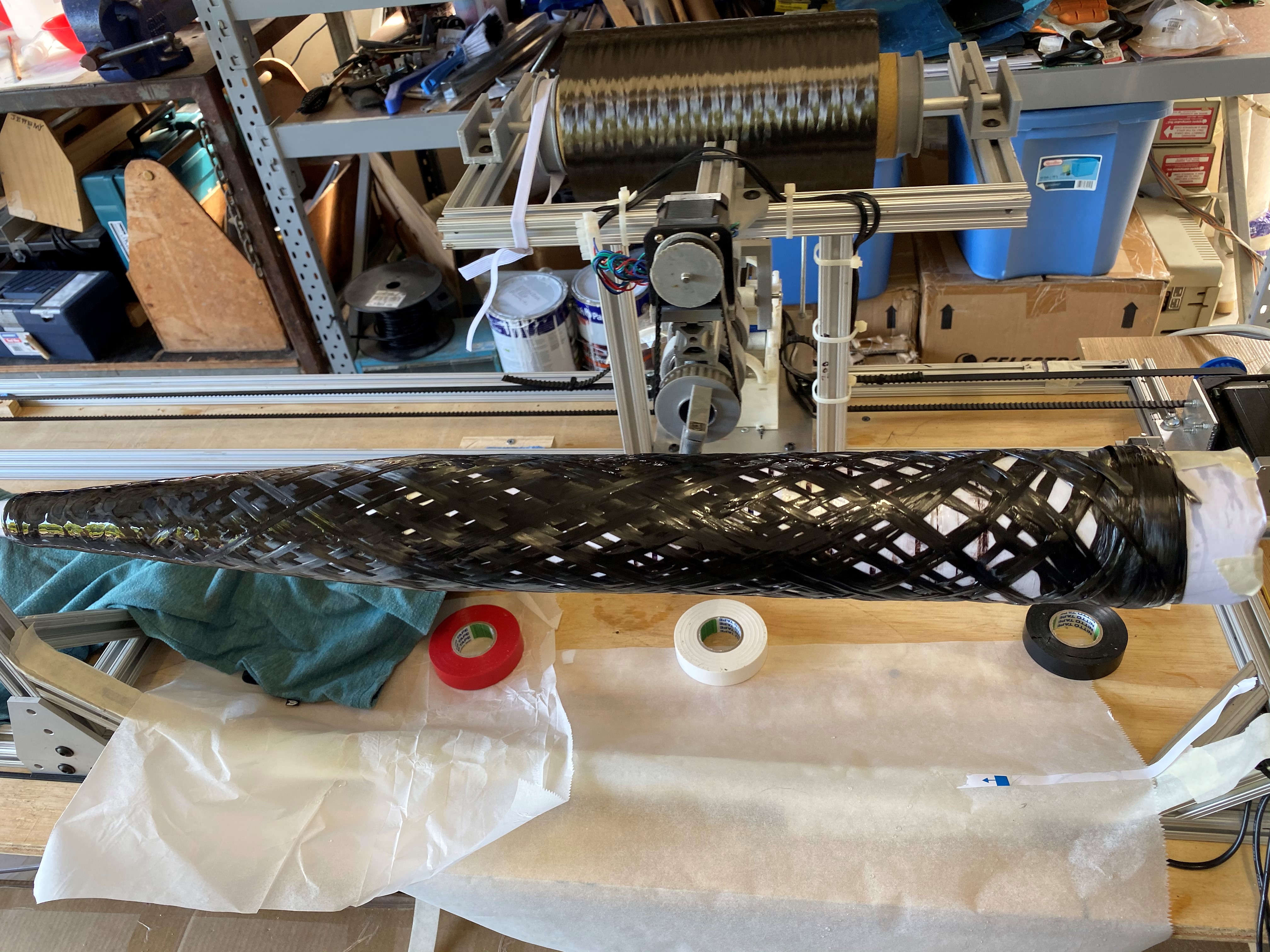
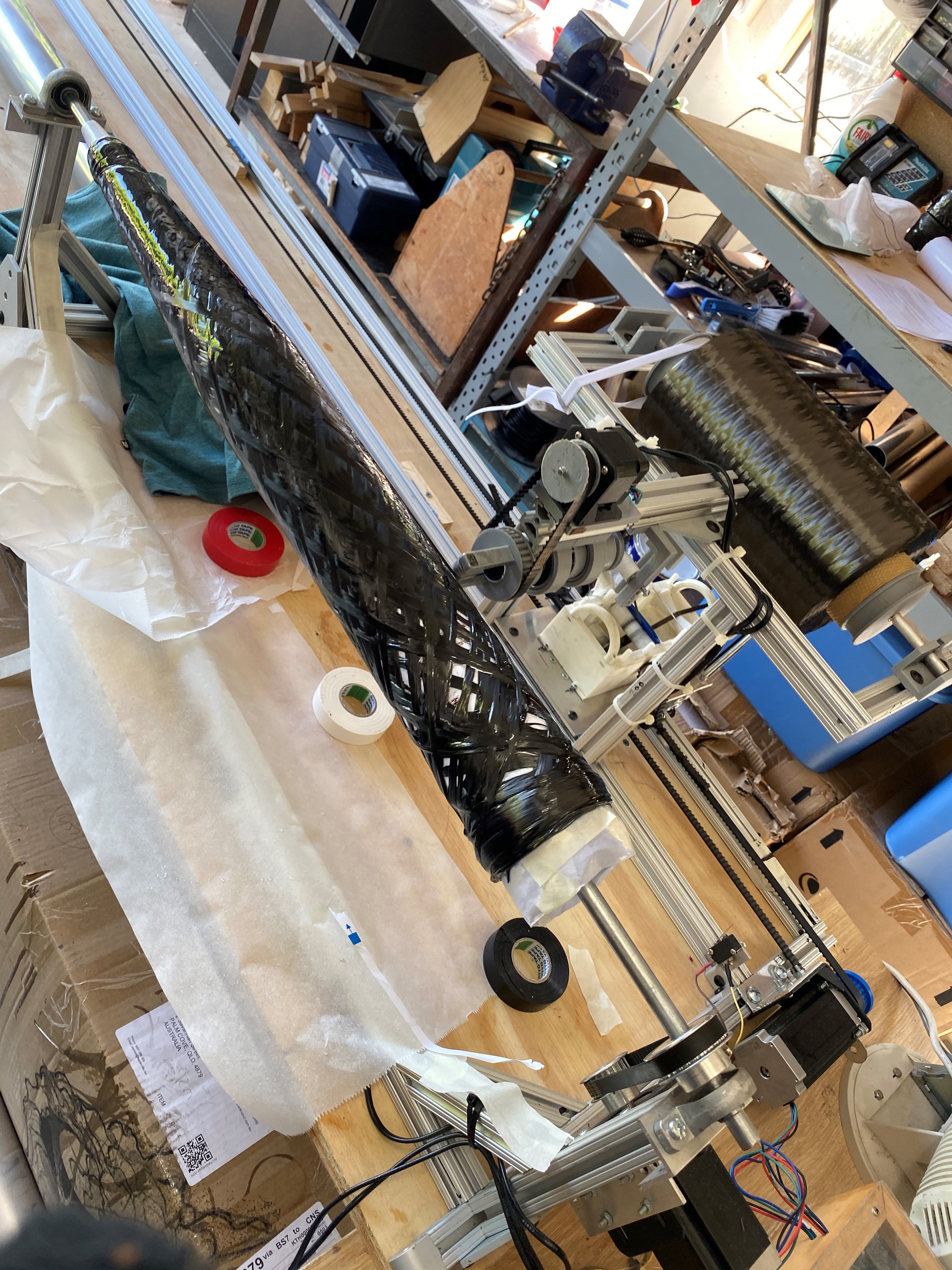
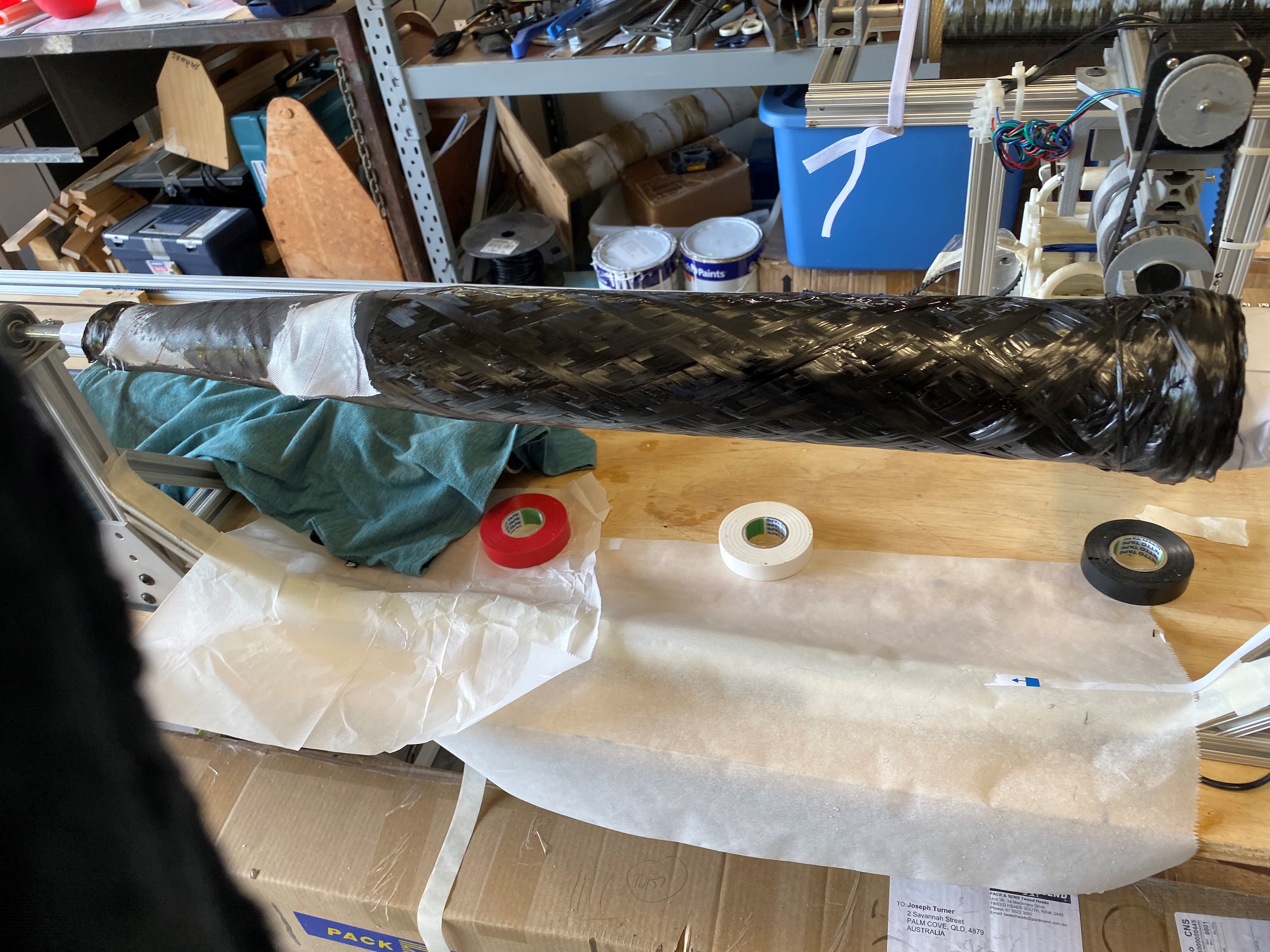
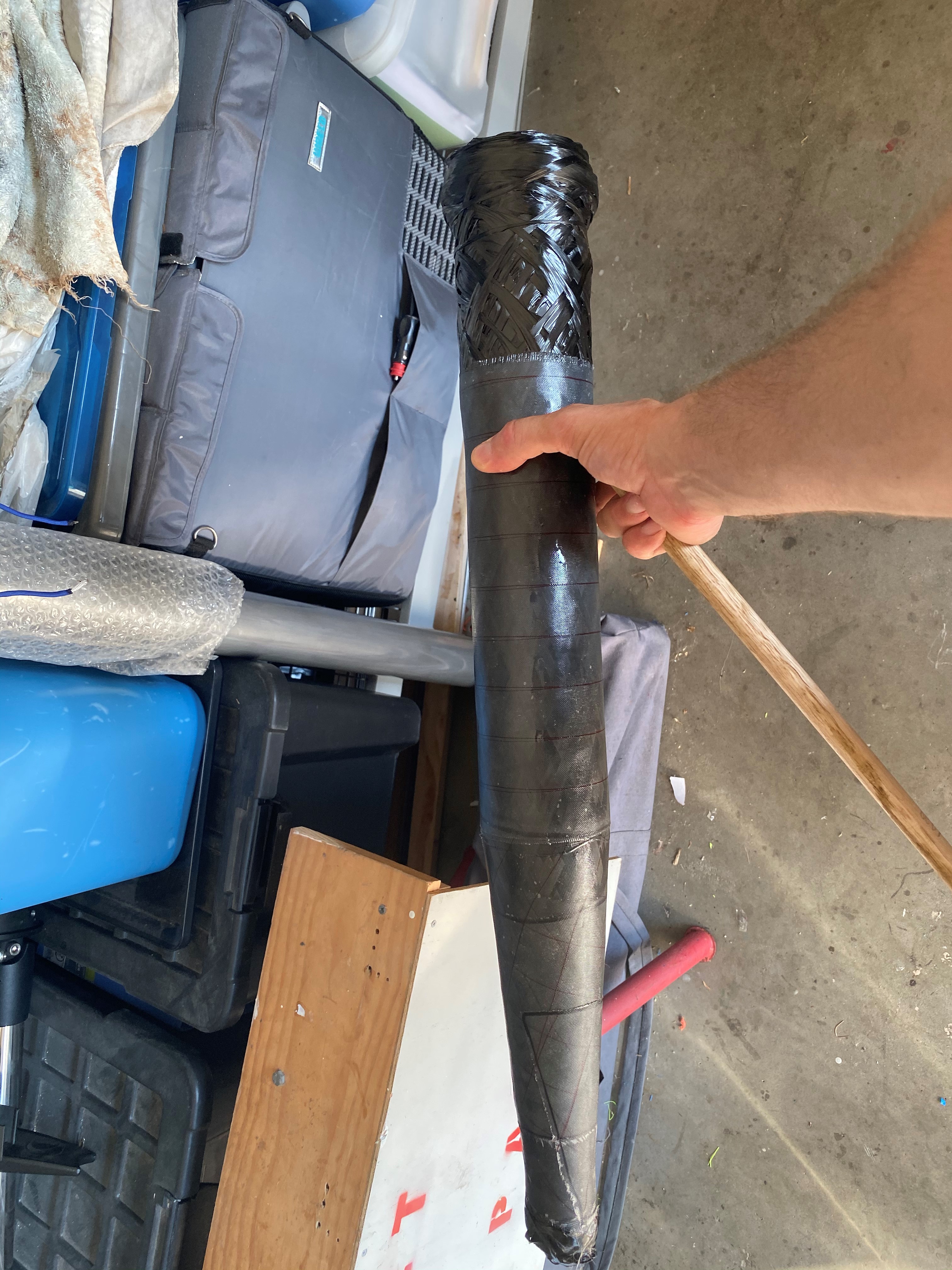
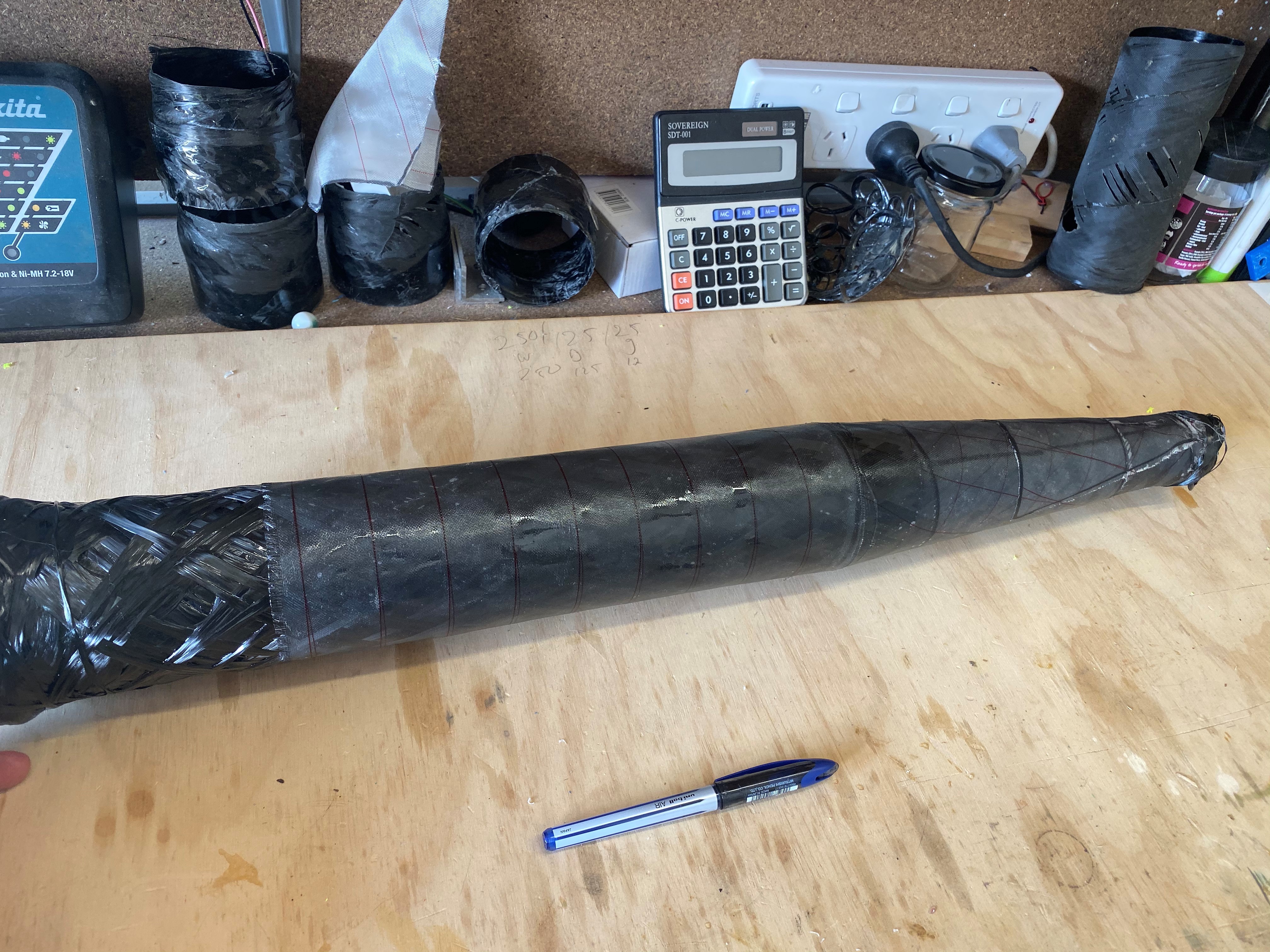
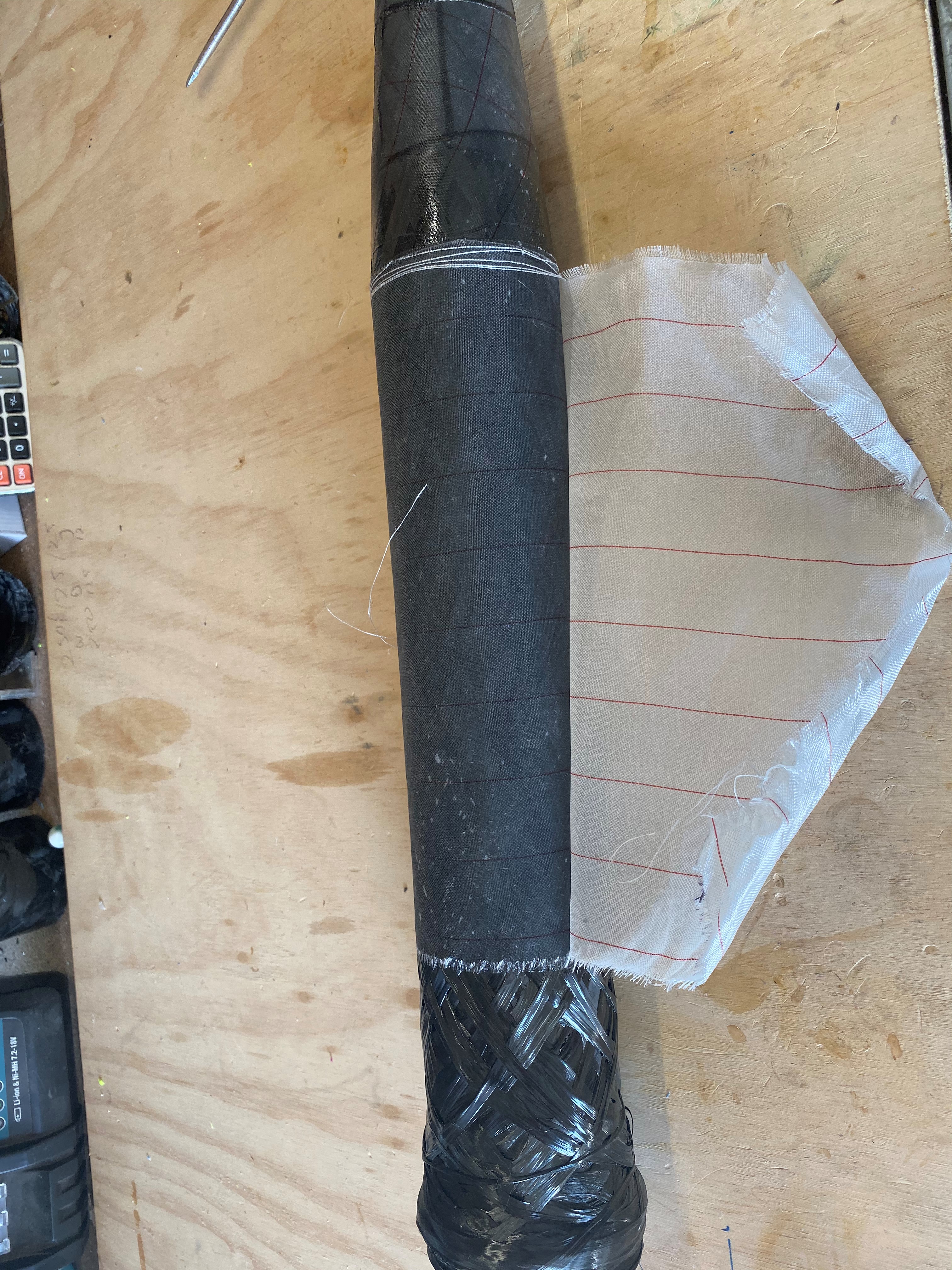
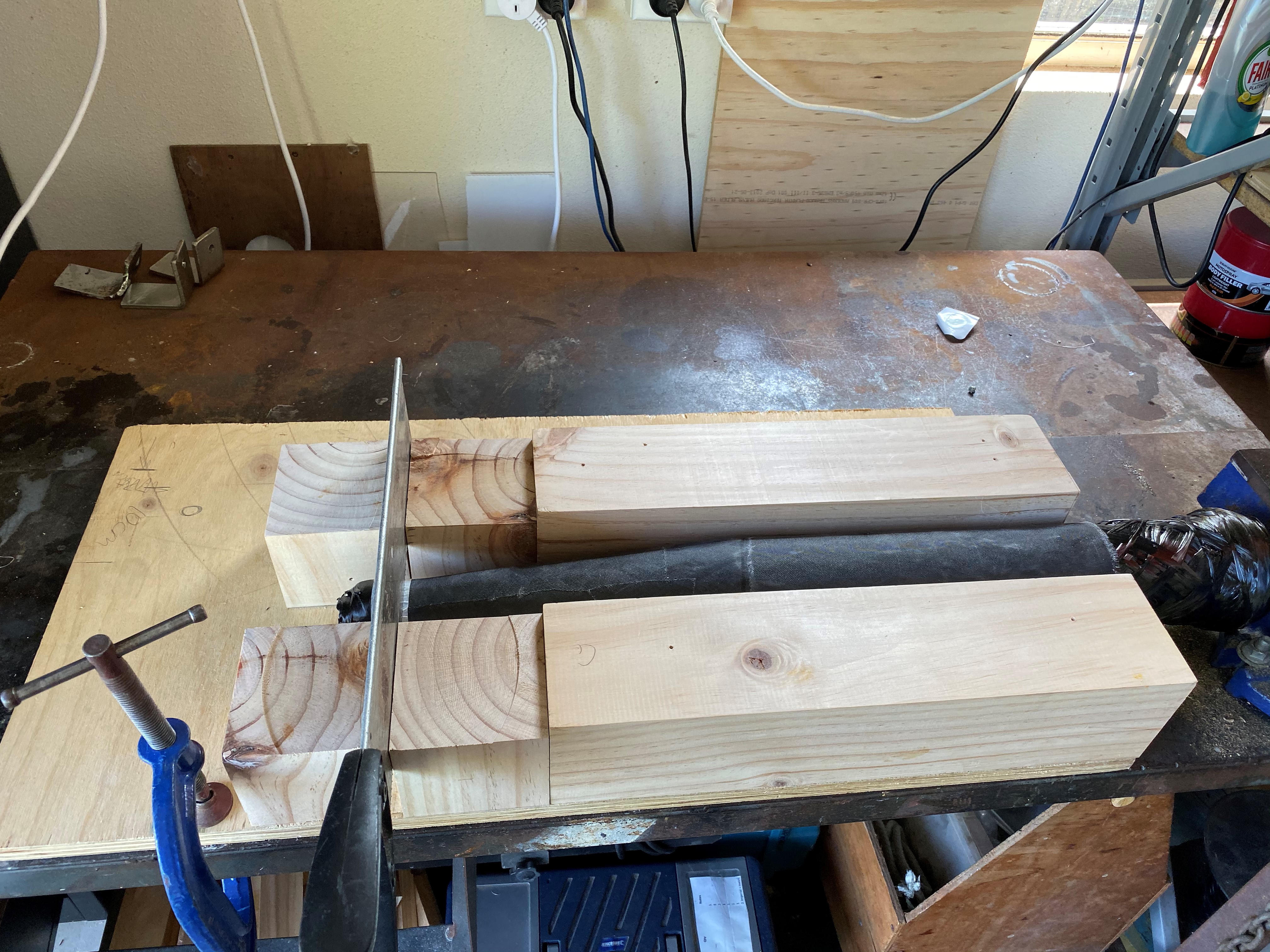
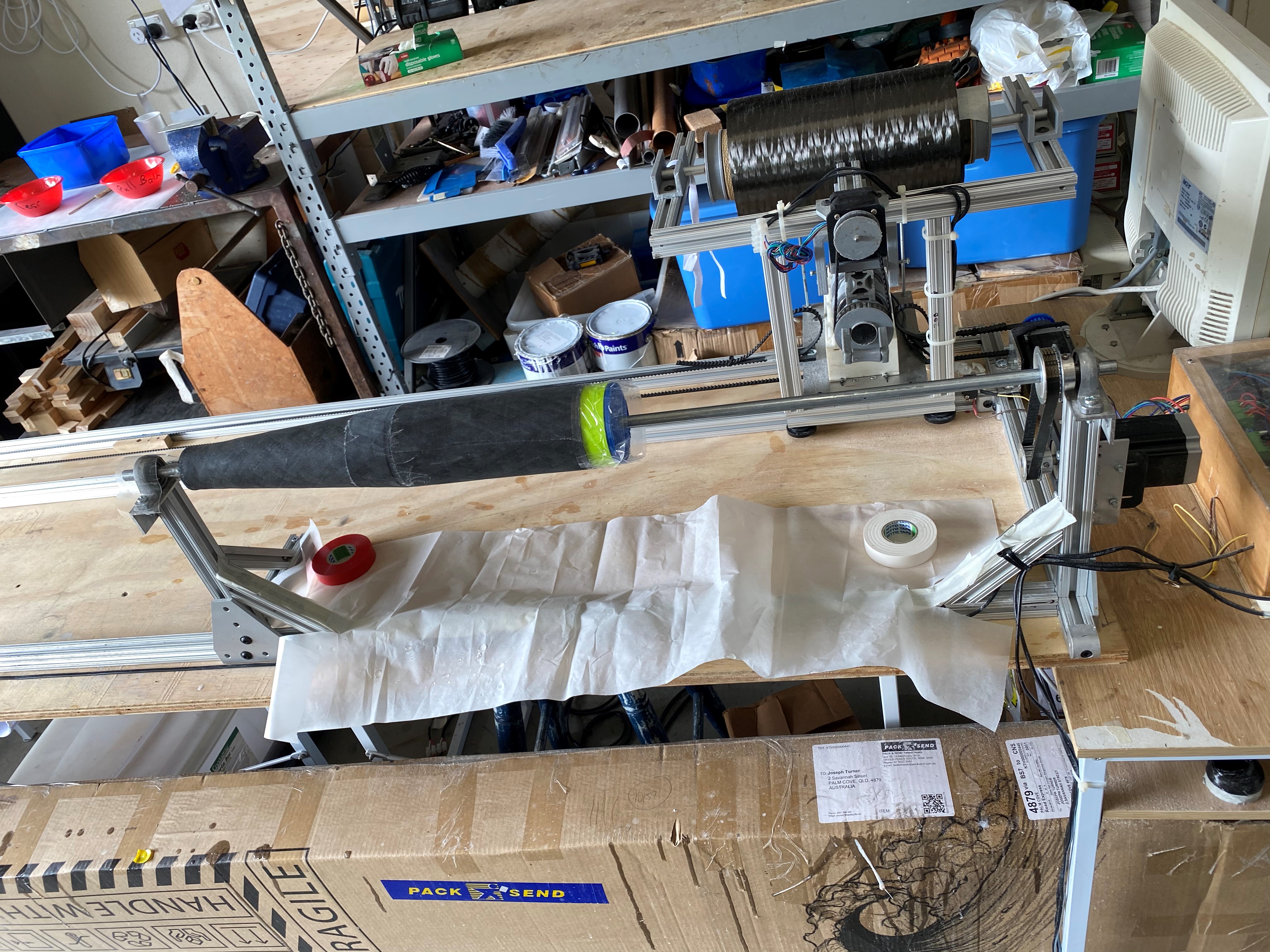
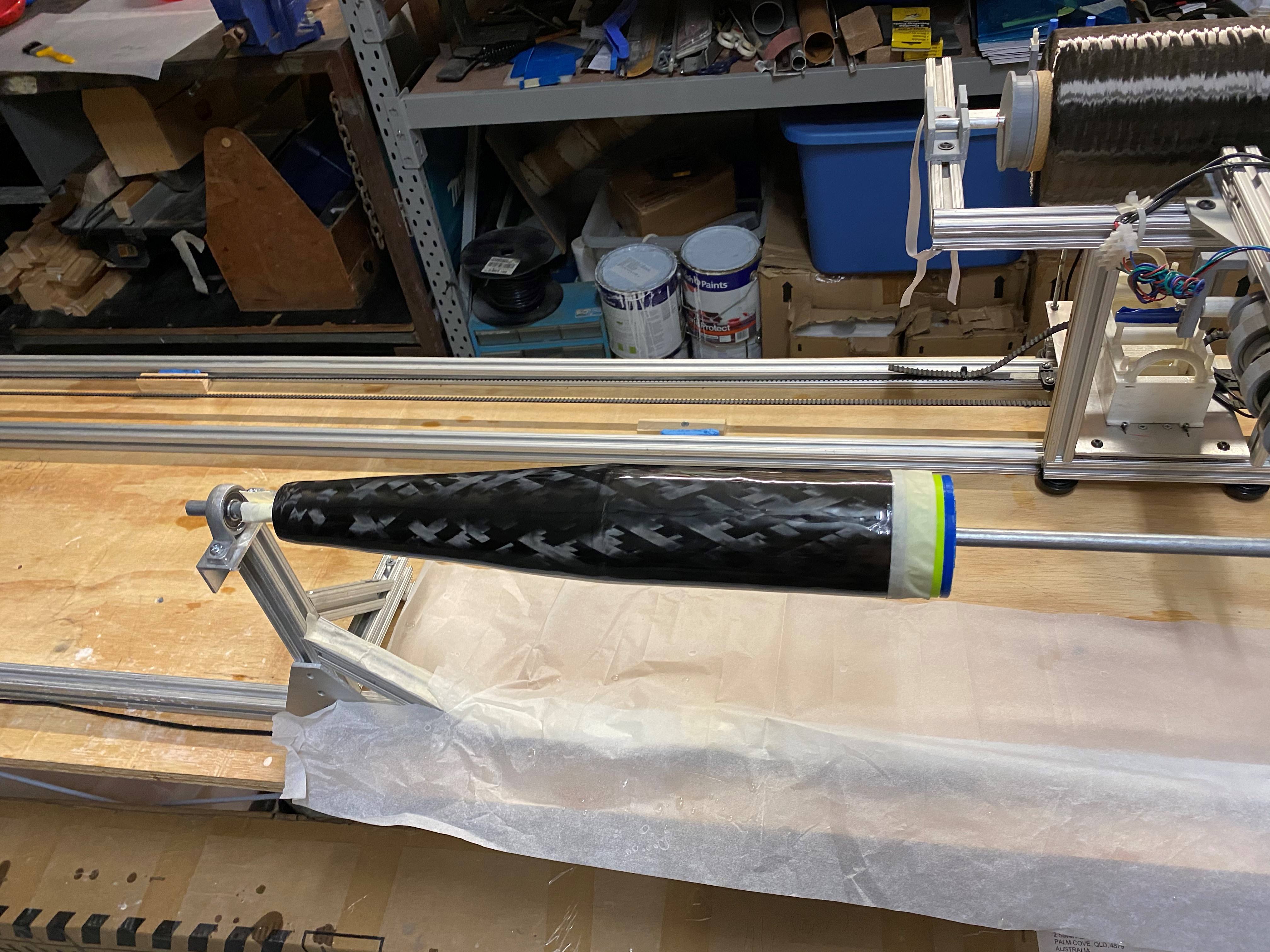
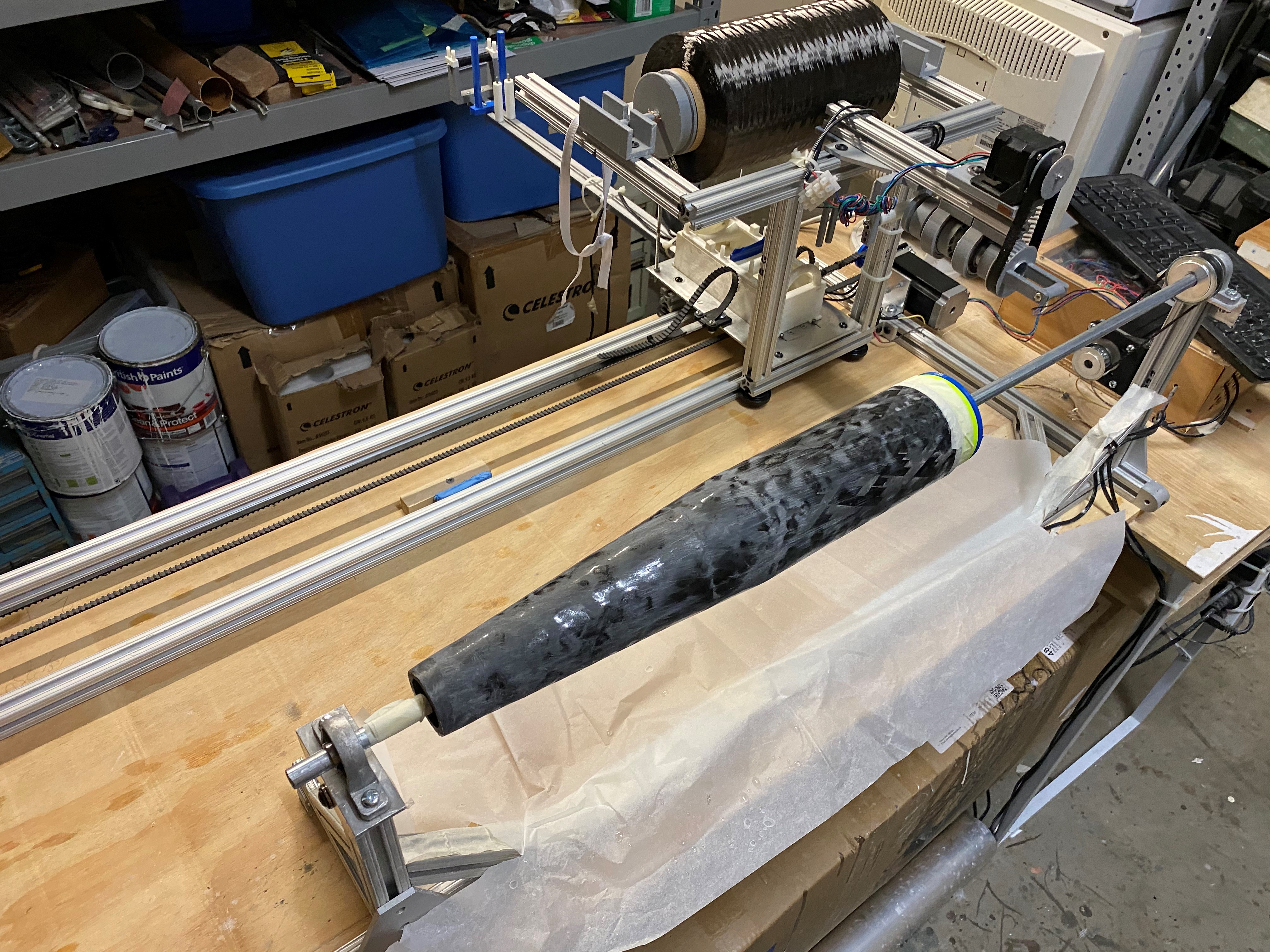
Repeated the above process two more times.
Then we 3-D printed a nose Cone tip – a parabolic one that results in a pretty good looking nose cone. I chose parabolic because it results in a rounded point and reduces the total length it would be, should it need to be conical (229 mm to about 108mm).
y = 0.238 * x * x
That x is between 0 and 22.3.
When the Epoxy shrinks, it is approx 0 to 21.65mm.
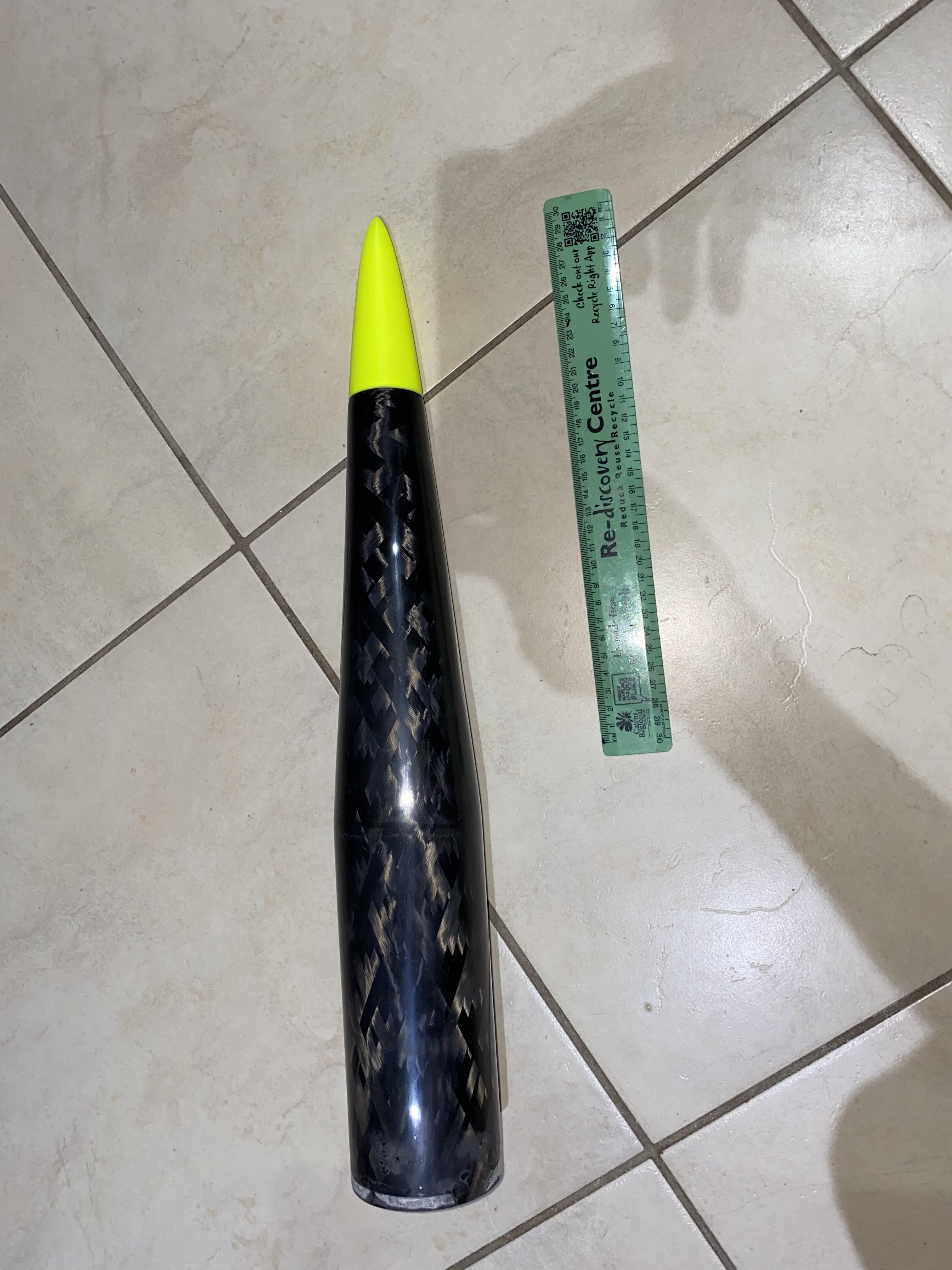
Obviously the final tip will be Aluminum and we will trim off some of the bottom of the Nose Cone – it doesn’t need to be that long.