The success of the flight is reliant upon the ejection charges separate the components and this this all depends upon the integrity of the Avionics installation.
For this reason, we review the Avionics bay to ensure that risks are identified and addressed. Some of these counter measures are shown in previous posts and no mention was made of how we arrived at the design here. We do this here.
Risks with Counter Measures
Switch Terminals
We were going to solder tips of wire and screw them into the terminals of the lever switch. When screwing them in, it tends to twist the entire wire around. This is probably “fine” but I can imagine that there is stress on the wire. The washer/screw should remain in place, but it is far from ideal.
So, what I did was get some very thin copper plate and cut out a small strip, 5mm x 10mm. Then I drilled a 3mm hole at one end. I sanded down the copper pieces of both sides and on curled one end (not the end with the hole) a little. Then I soldered a wire to the copper, leaving a small gap at the end with the hole (so I don’t add excessive thickness). At the other end, (the curled end), I applied 5 minute epoxy to the wire/insulation. This provides a very strong connector which won’t turn around when being attached to the switch and minimal strain is put on the wire strands! The copper is a great conductor and is very easy to solder to. Copper can also be bent to whatever shape is required.
Below is a picture as it might be hard to visualize it from the description above.
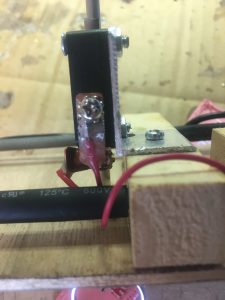
The curl is intentional. It reduces chance of wire rubbing against sharp edge.
Screws
Screws can rattle undone, so I applied LocTite equivalent to all screws. This includes:-
- Bulkhead powder wells (PVC caps)
- Bulkhead terminal blocks
- Raven 3 PCB screws
- Screw holding the switch right-angle
- Screws holding the 3 x 2 black terminal block
Glue to some components
A lot of the components that are attached only have one screw. They are tightened a lot, but there is always the risk they could loosen/rotate. To reduce the chance of this, I applied a few drops of CA glue to them. The parts that had this done were:-
- Bulkhead powder wells (PVC caps)
- Bulkhead terminal blocks
- MicroSwitch right-angle aluminium piece
Nine Volt battery Clip
I was concerned that the 9 volt battery clip was not of sufficiently strong construction and the clip I used was recycled from another project. So what I did was purchase a replacement one from Jaycar.
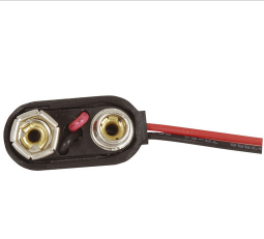
I was also concerned about the red/black wires getting into places they shouldn’t so I :-
- Cut the black wire to a length that meant it couldn’t possibly be a problem
- Applied small drops of CA glue to the red wire where I wanted it to rest, just to encourage it to stay there. It may come of in flight, but its insignificant weight means it should be okay.
The Dean-Plug
I wanted to ensure that Dean-Plug would not separate in flight. So I will install a small cable tie as shown below.
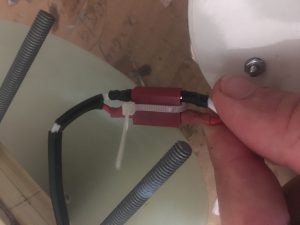
Wires into Raven3
I removed a little more insulation then i should have on some of the wires that are screwed into the Terminal block on the Raven 3. As a consequences, some of the wire was visible. While it is extremely unlikely that we could have some short, I decided to cut the wire a little, to reduce the amount of bare wire showing. See the picture below.
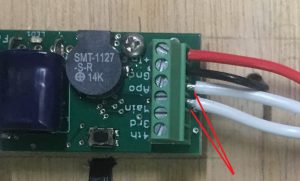
It is also about taking pride in the work that I do; keeping it look good as well.
SuperCap on Raven3
It is recommended that the SuperCap be glued down if the rocket is going experience high-G flights. My first flight of this rocket will not involve high-G’s, but subsequent flights may. Following instructions, I decided to apply a drop of Epoxy under the capacitor.