Did a trial run doing a layup of Carbon Fibre on to G10 material on the weekend.
Layup consisted of:-
* Small piece of G10 material “roughed up” with Grit 60 sand paper,
* Two layers of CF
* Two pieces of Nylon Peel Ply
* K3600 Renlam Epoxy
The first piece of carbon fibre extended past the edge of G10 by about 15mm. The second layer was 5 mm within the edges.
I waited 5.5 hours after the layup to cut the excess off CF. It was easy to do.
Waited another 15 hours before I removed the Peel Ply. It was easy to remove the Peel Ply.
Below are some photos I took.
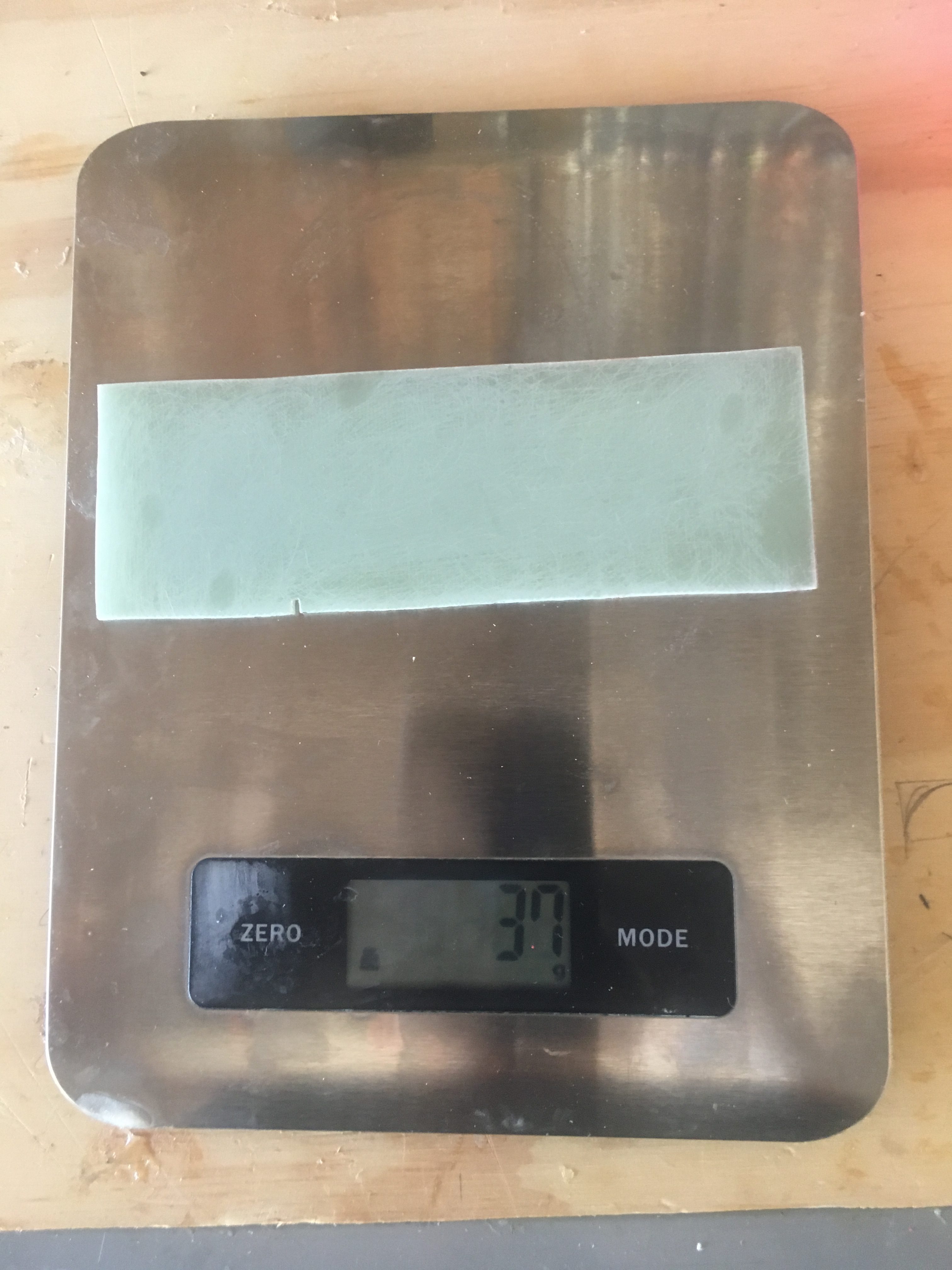
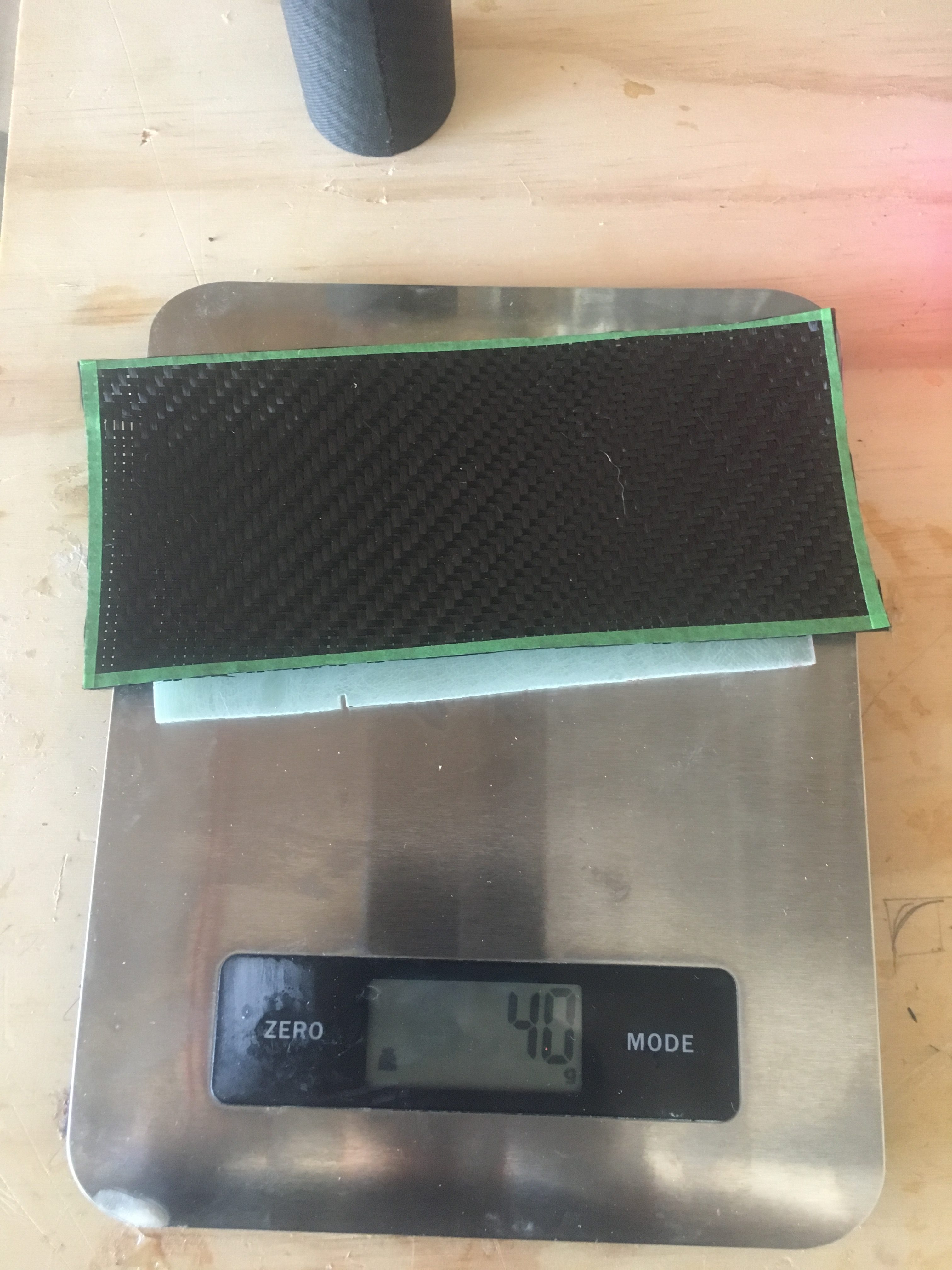
So therefore the large piece of carbon fiber weights ~3 grams.
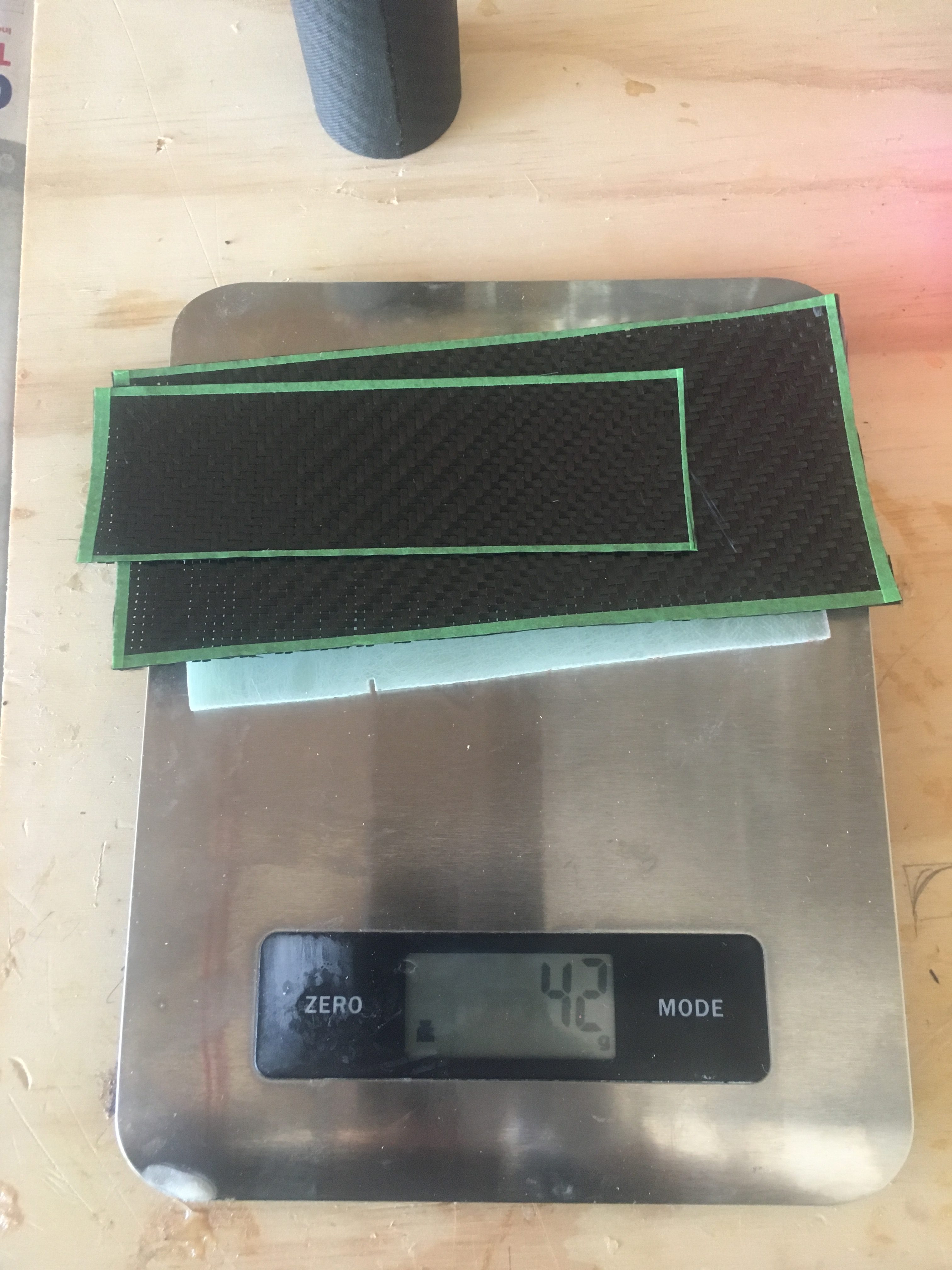
So therefore the smaller piece of carbon fiber weights ~2 grams.
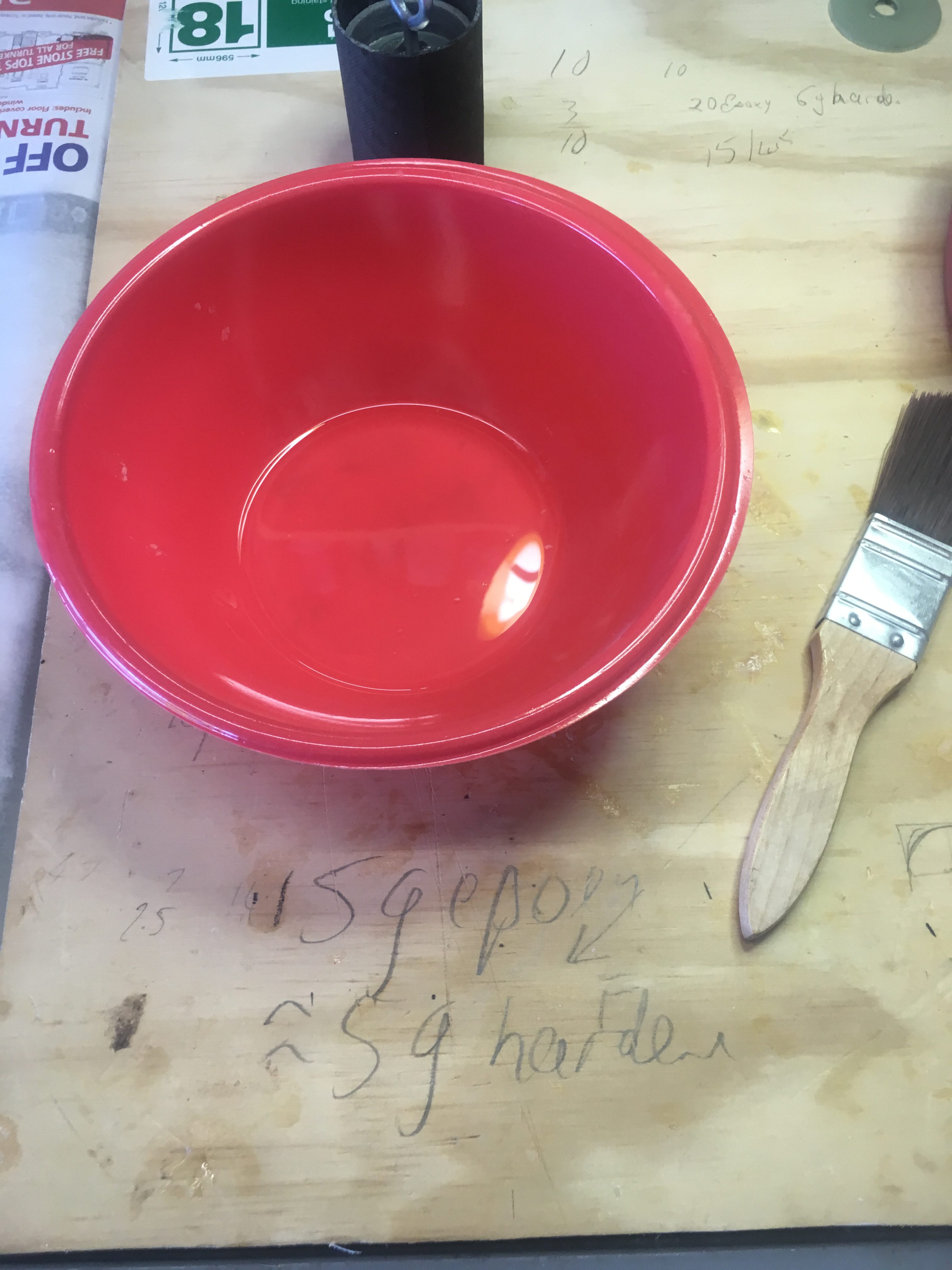
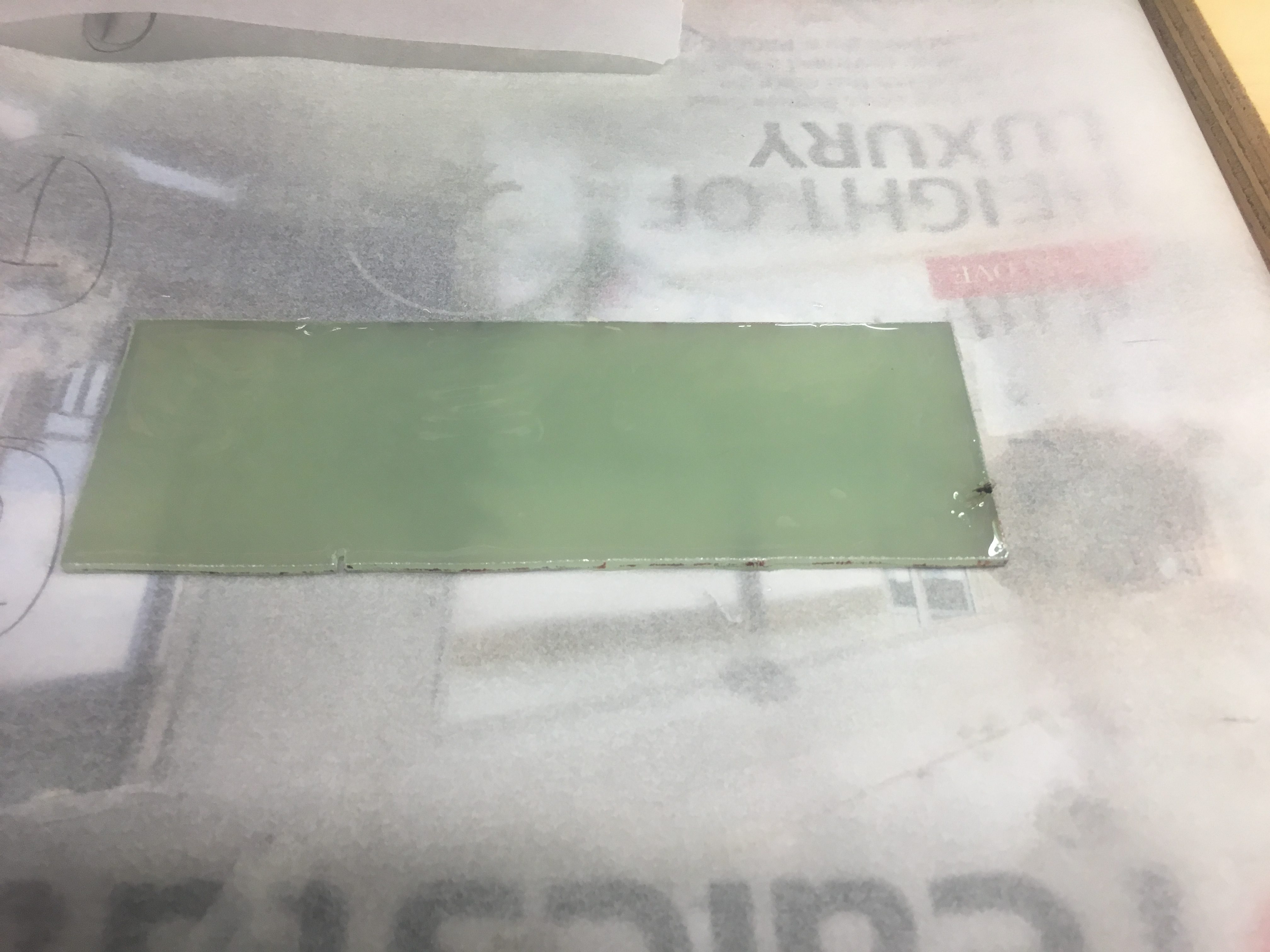
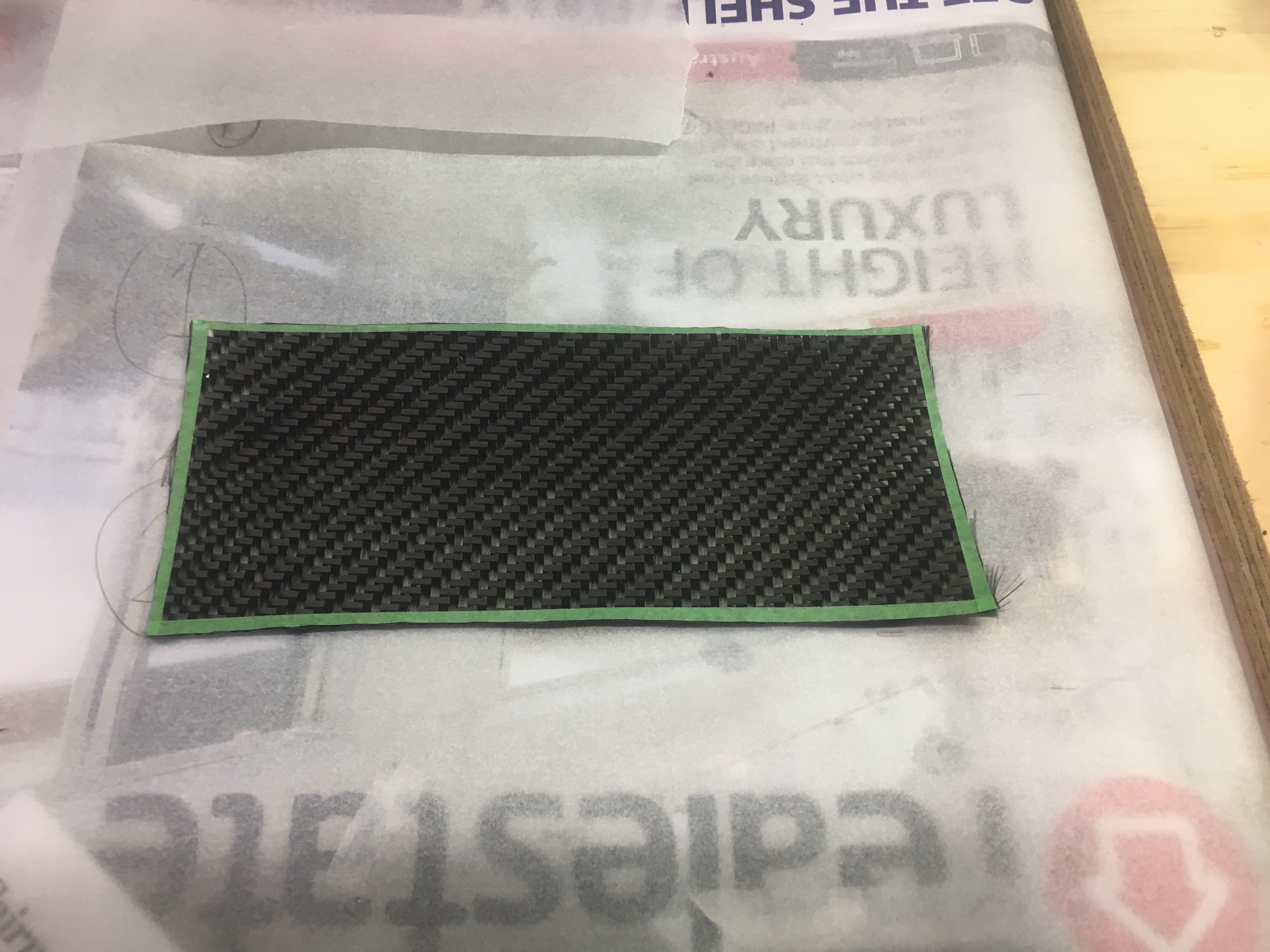
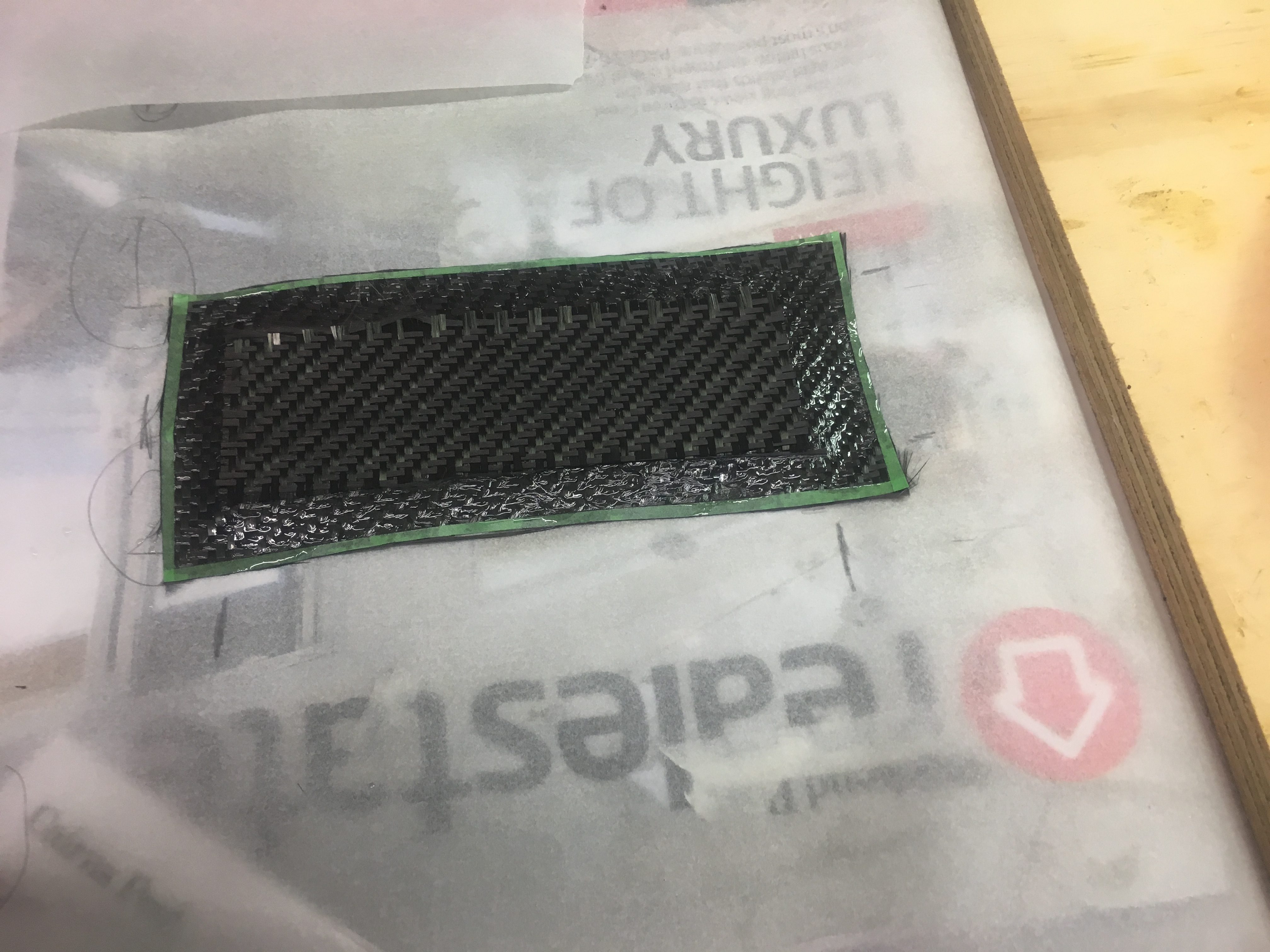
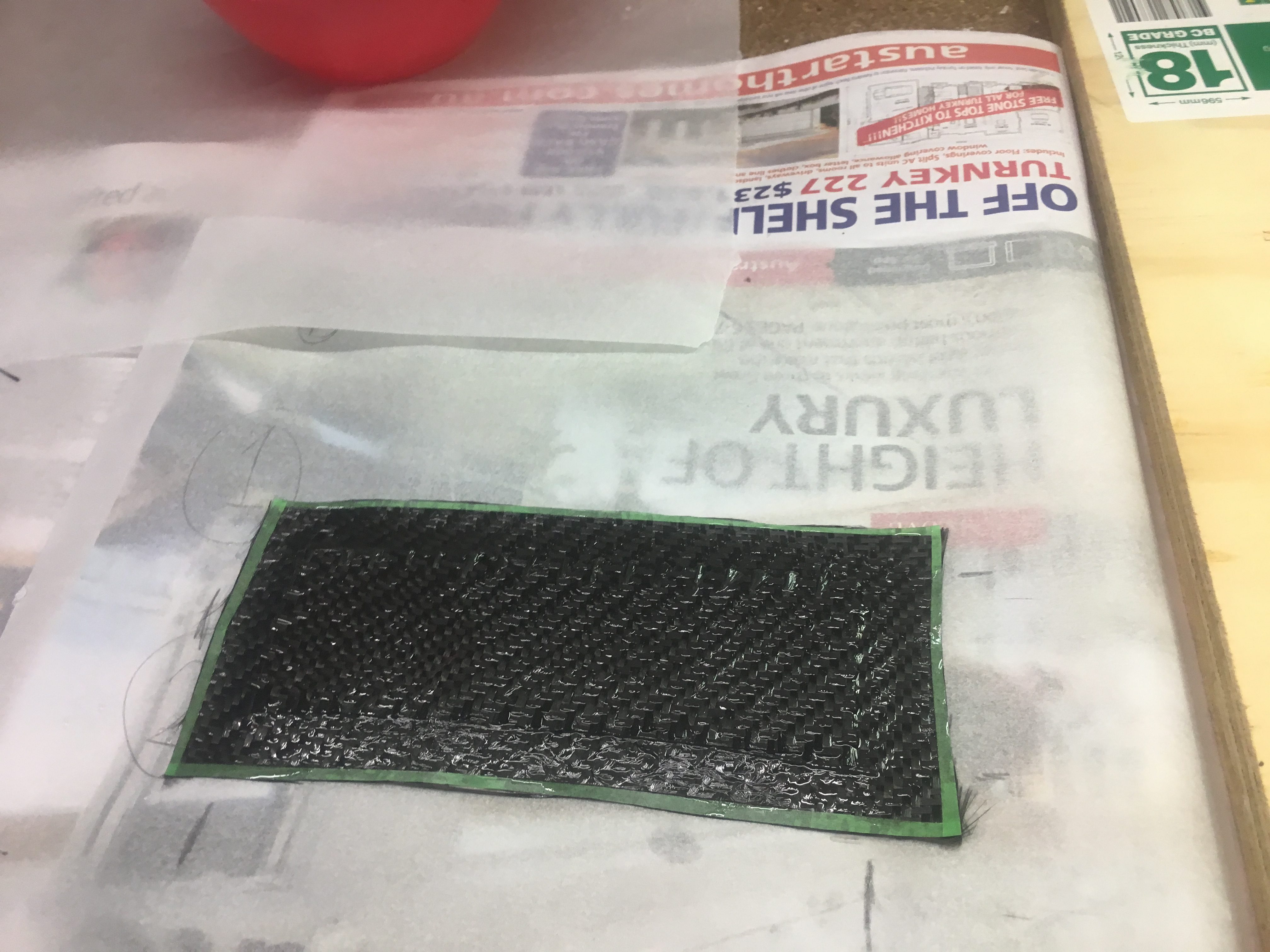
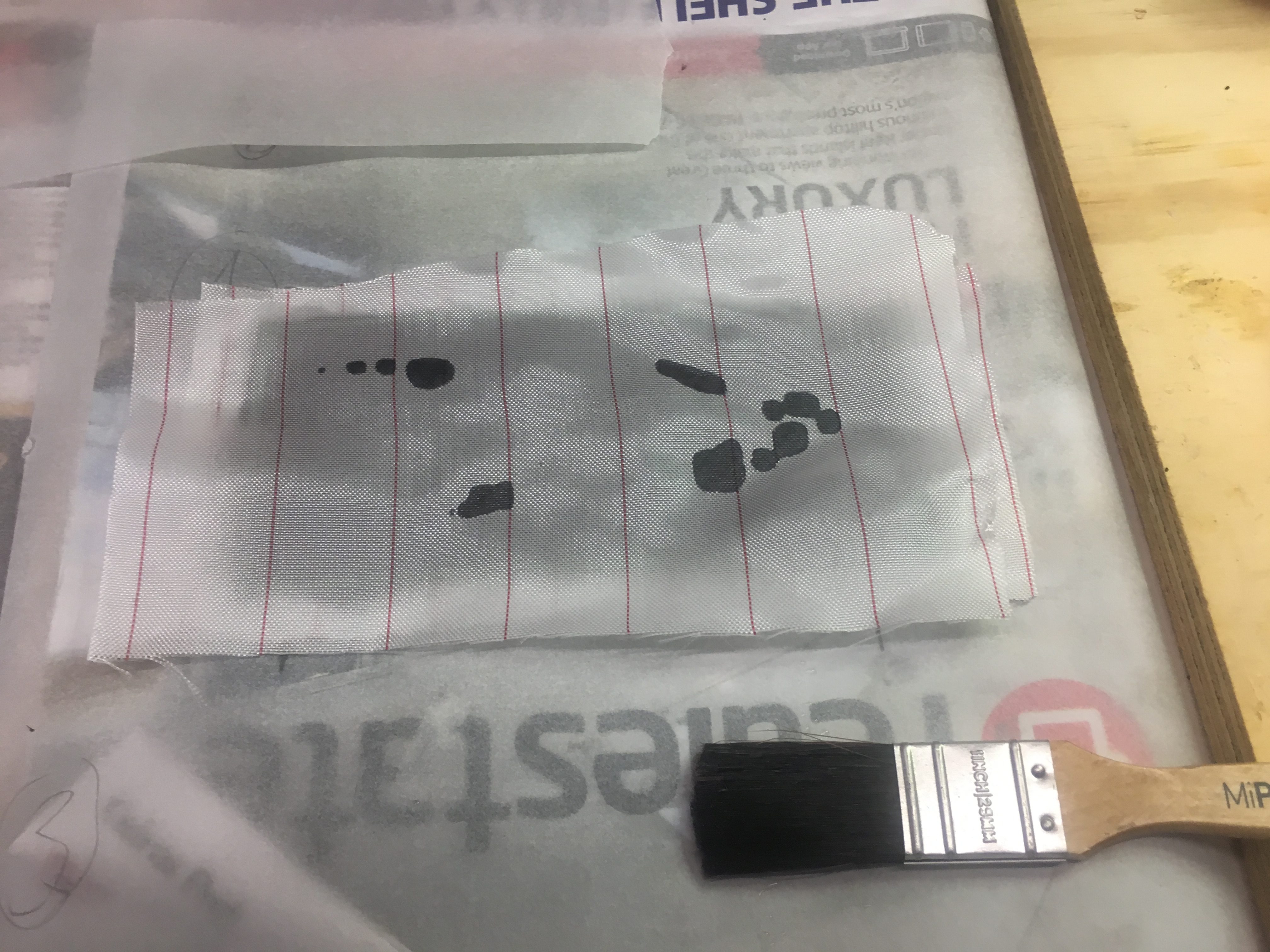
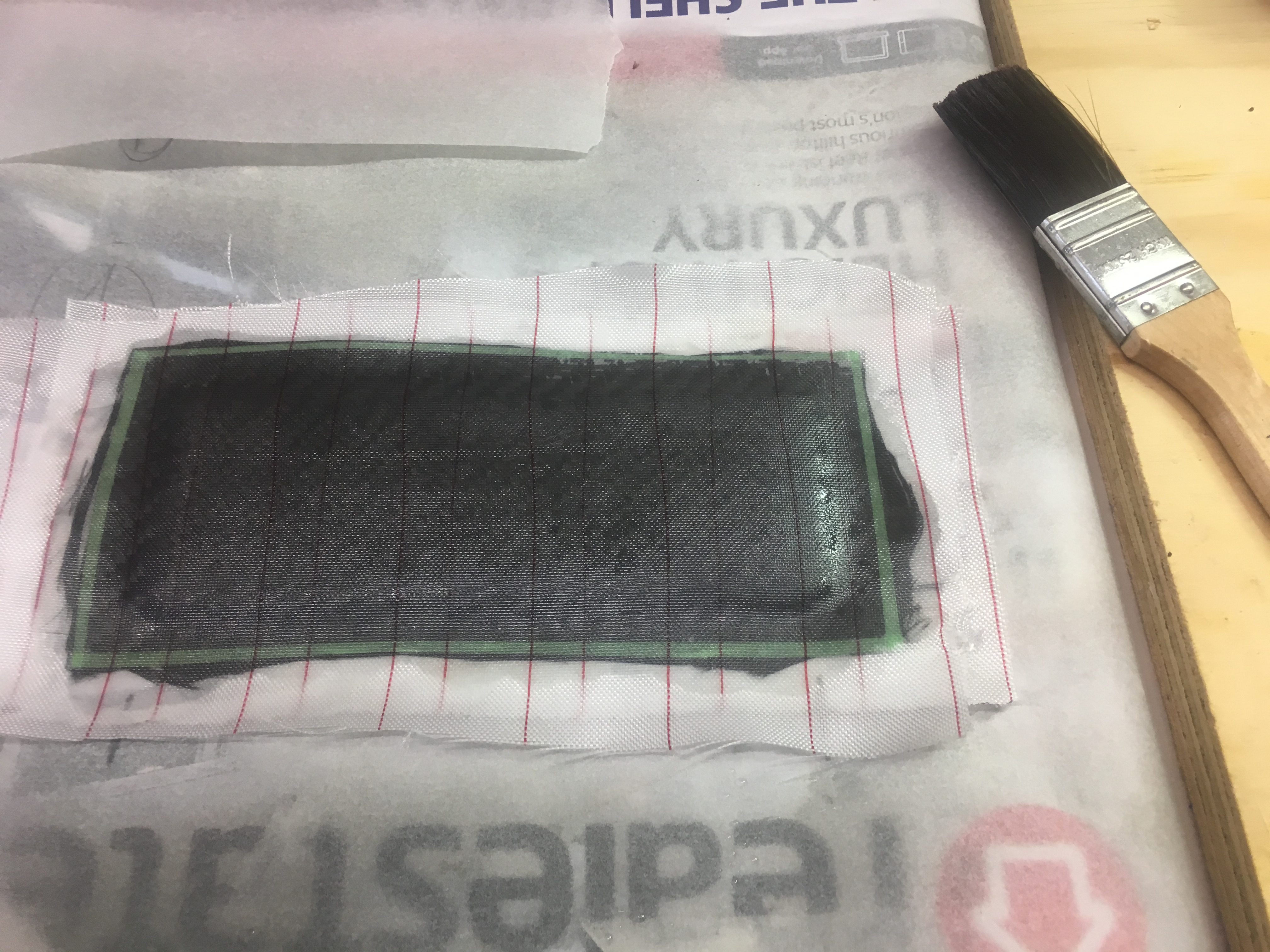
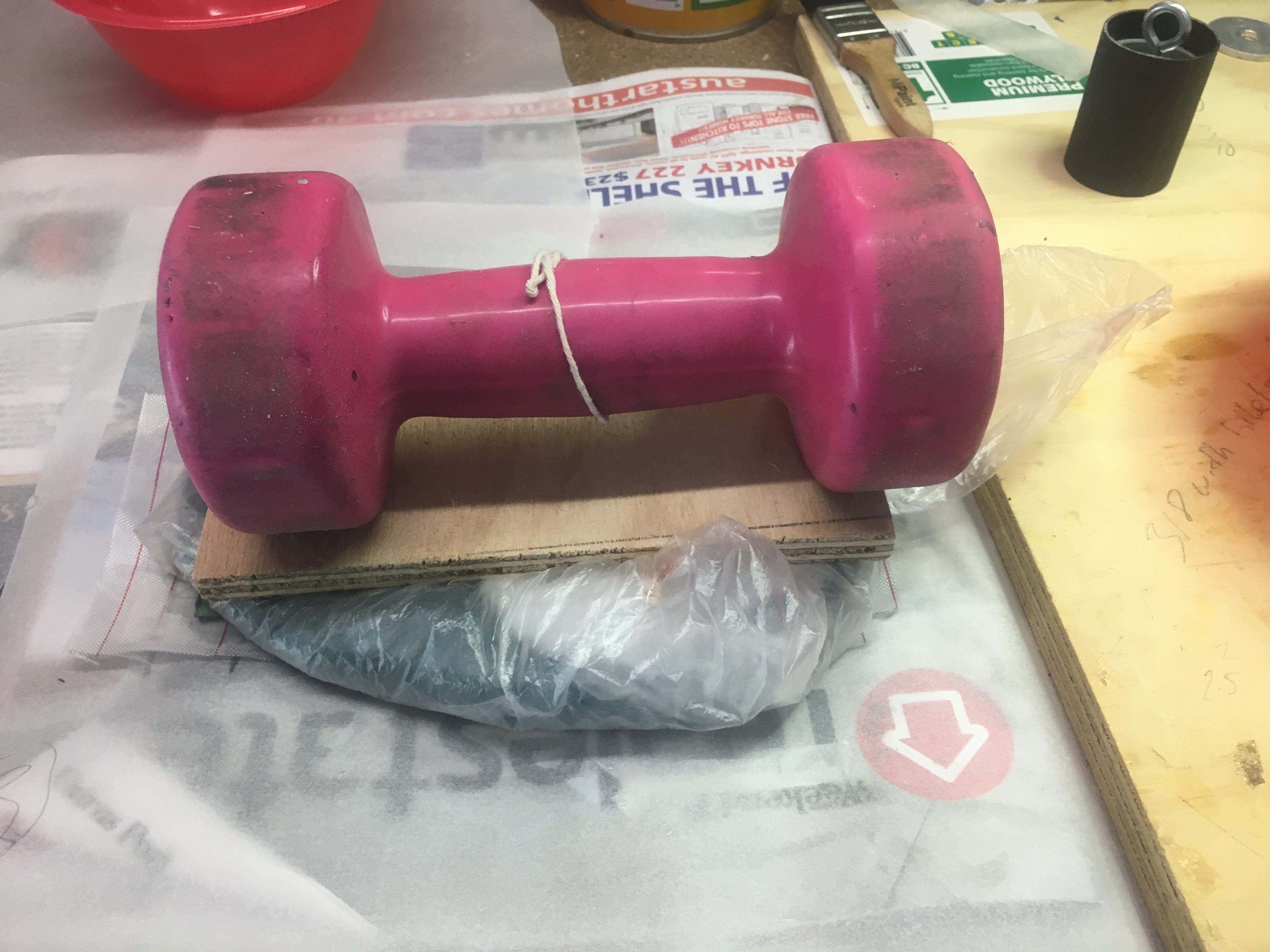
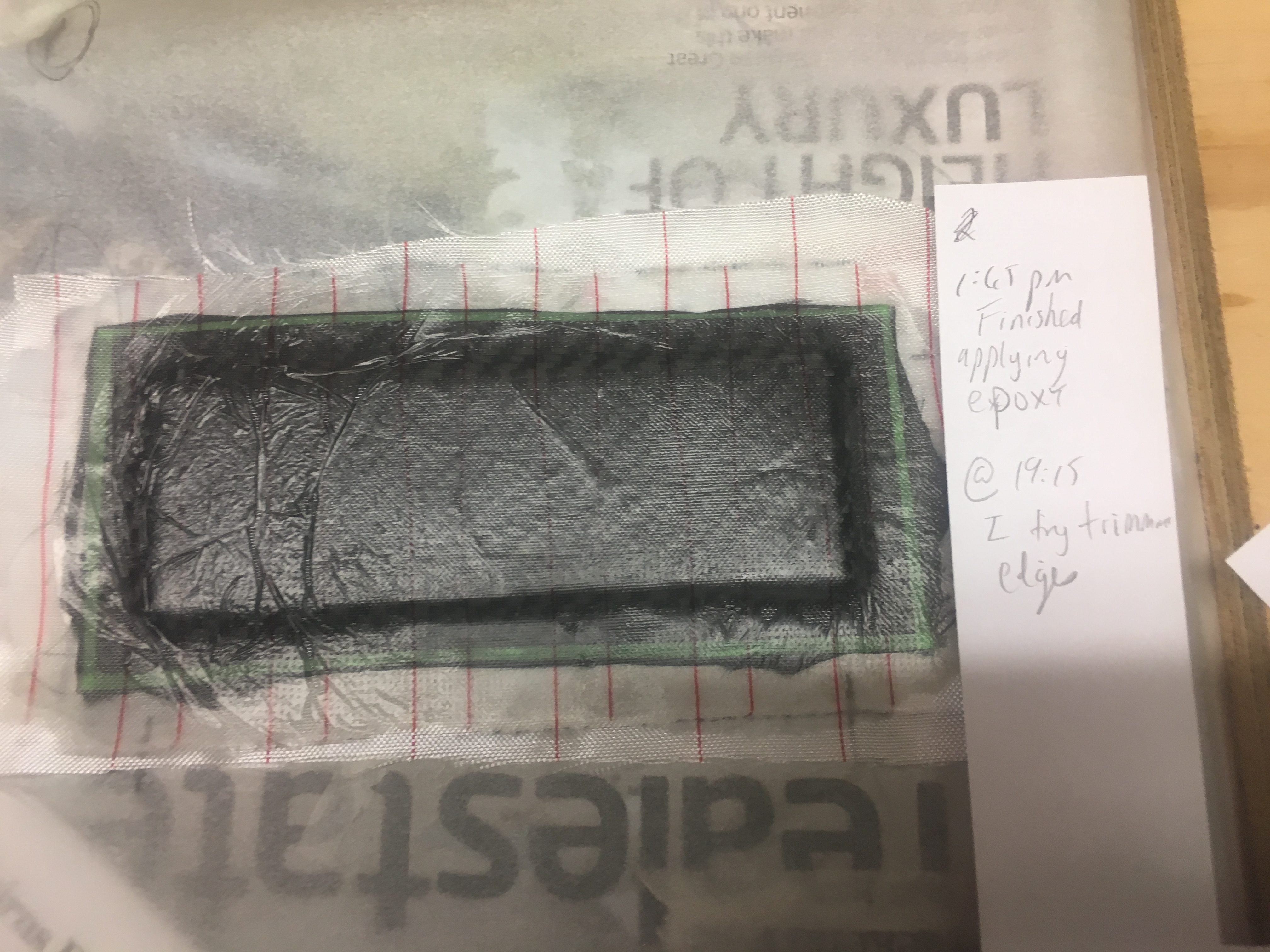
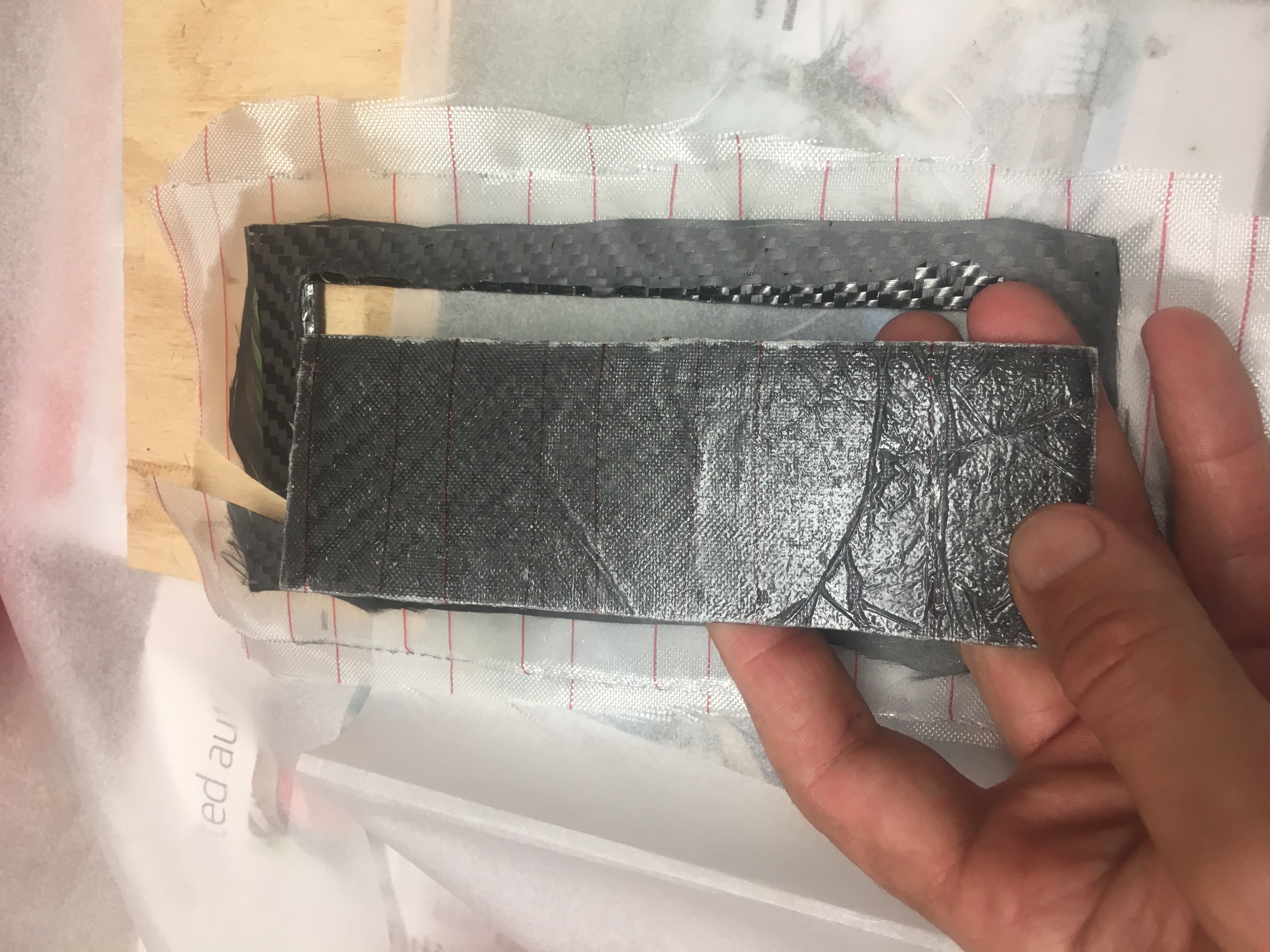
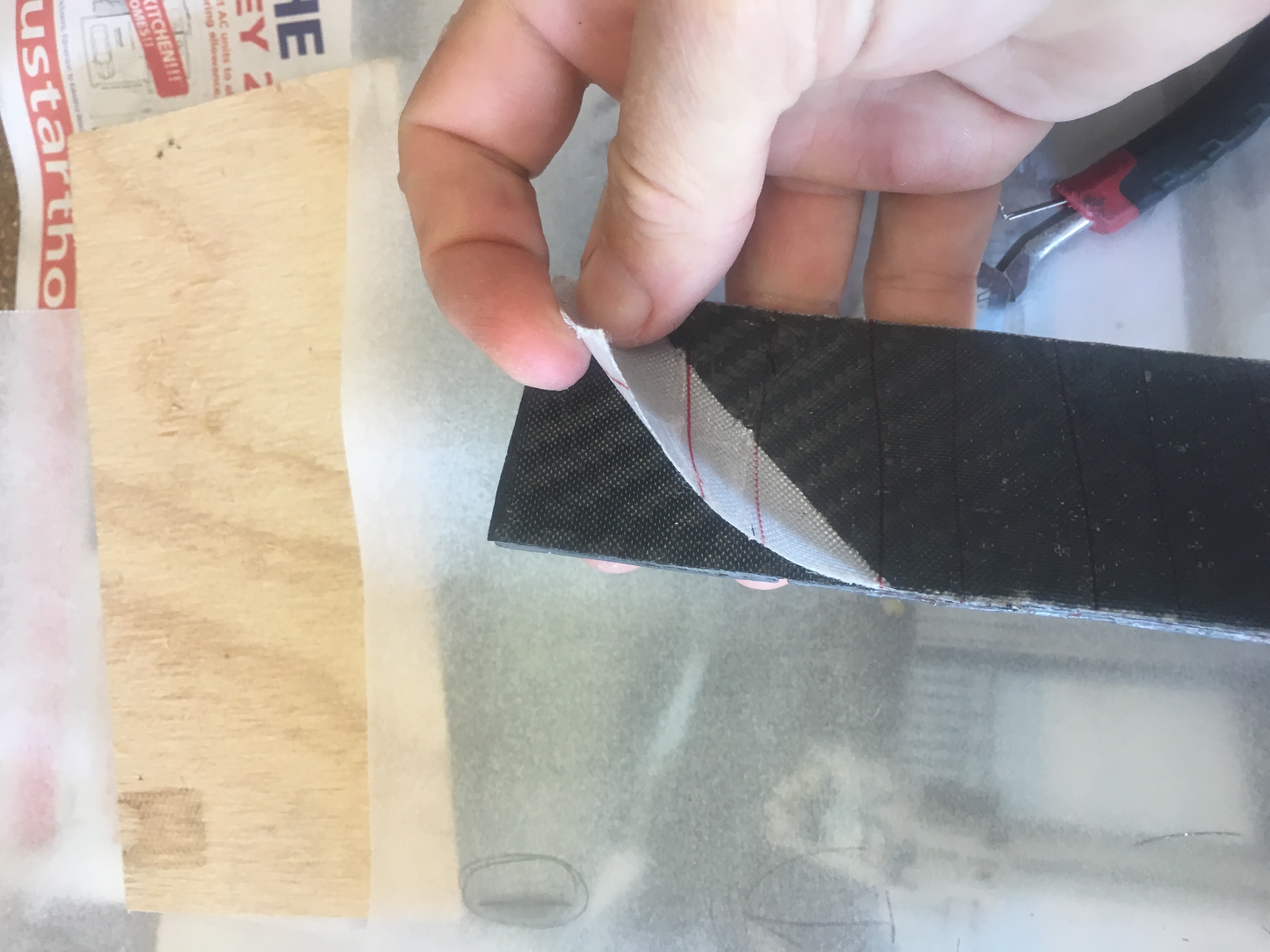
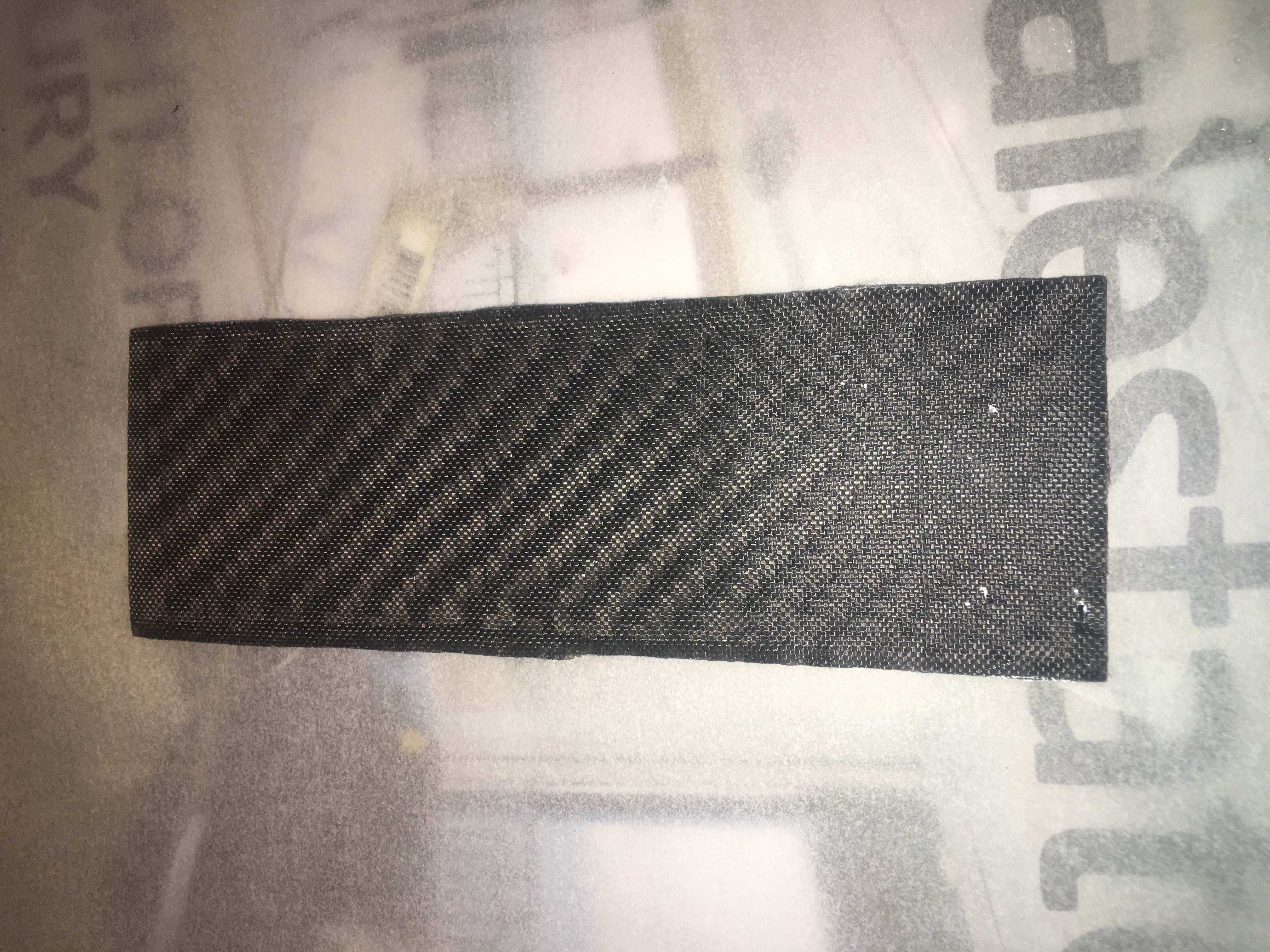
Final Weight: 44 grams
This means the Epoxy weight was approximately: 2 grams
So the total weight of the epoxy/CF is 3 + 2 + 2 = 7 grams. Very light!
The carbon fibre seems to have bonded well with the G10 material. The resultant piece is a lot stiffer.
My next step (if this was the real fin) would be to apply a very thing coat of K3600 and then sand with progressively higher grits.
Now considering a real fin layup this weekend.