The Centering rings are what we use to attach the Motor Mount to the Air-frame. The Centering rings provided did not fit the Motor mount, too tight (this is not bad). So I very carefully sanded them down by hand, as evenly as possible. Every few minutes I would check to see if they would fit. The top centering ring is notched, to slide over the Bridle cord. So I marked the top of the Motor mount as ‘Top’. And I marked the bottom of the Motor Mount as bottom.
Eventually after about 30mins of patient sanding I was able to slide both centering rings over the Motor Mount.
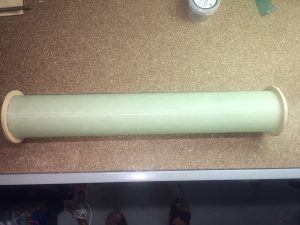