Preparation
Preparation is key to the success. I made sure we sanded the areas to be filleted with Grit 60 Sand paper, that they were then cleaned with Methylated spirits and then taped up.
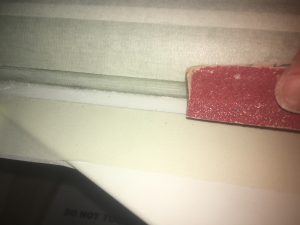
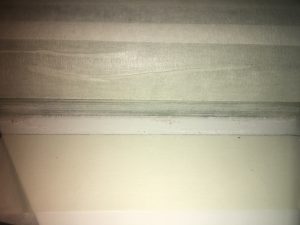
All practice external filleting I had done so far had neglected the ends; it was more focused on the the main stretch. The width of the fillets needs to converge to zero at both ends of the fin on the air-frame. I did a simple plot y = 2x^2 on my printer and printed it out and used it to create masking tape pieces to stick at the fin ends. What resulted looks as follows:-
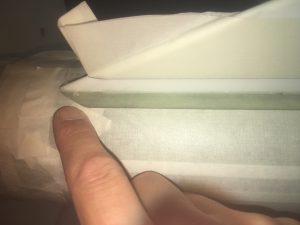
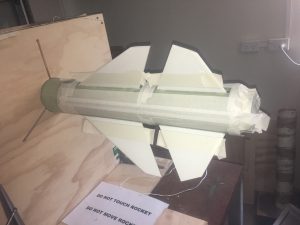
The Glue
We made a normal ‘peanut’ consistency batch of Epoxy. We decided to use the new syringes as the old ones are too sticky and hard to push.
We originally made 20ml/4ml of epoxy for one one side of fins (lower and upper fins). We found that there was probably about 6ml of epoxy left over – so wastage. In future Epoxy runs, we’ll make it up using 15ml/3ml of 105/206.
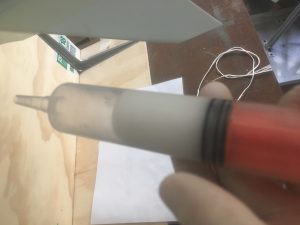
The result
Back fin.
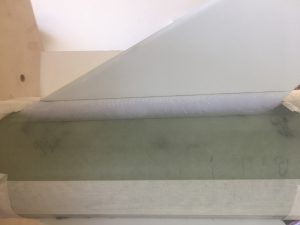
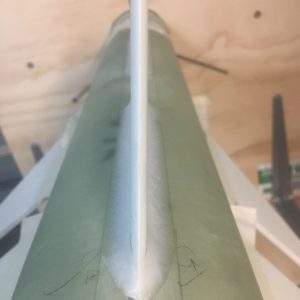
Fairly happy with it. I am going to need to build up the back/front of fins to ensure smooth transition. Not quite as good as I had hoped there.